Robotics Specialist Innok Robotics Uses MTi-30 motion tracker from Xsens In its AGVs For Outdoor Space

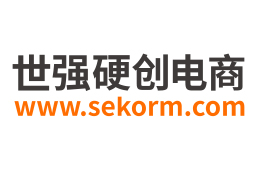

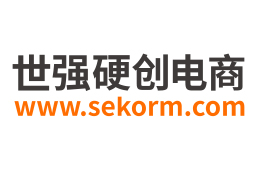
It is generally easier to design automated ground vehicles (AGVs) for indoor than for outdoor use. Inside a warehouse, for instance, an AGV moves on a smoothly finished, flat surface, in an area enclosed by walls, and along fixed, dedicated routes which are marked with barriers or guidelines for navigation, and which eliminate the risk of collision with people or other objects.
Few companies have successfully mastered the much more difficult challenge of making a robotic vehicle which can be deployed outside, on mixed terrain. Among the pioneers in this field is Innok Robotics, based in Regenstauf, Germany. And the solution which it uses for tracking the position of its AGVs with centimeter-level precision is a form of dead reckoning using the inputs from a sophisticated MTi-30 motion tracker from XSENS.
A teachable robot
Innok Robotics supplies modular development platforms which researchers and manufacturers can use as the basis of designs for application-specific AGVs. It is also developing a new range of standard AGVs for use in emerging applications, such as robotic ground transportation between warehouses in a campus or business park.
Innok Robotics’ designs have to solve both mechanical and computing problems. The mechanical problems arise from the operating conditions. A development platform for agricultural AGVs, for instance, must be able to climb and descend slopes, move as comfortably on soil or rock as on asphalt, and operate in all weathers and temperatures.
The Innok Robotics AGVs’ traction system can handle all types of terrain
Innok therefore pays close attention to the materials used in the manufacture of its AGVs, the environmental sealing, and the traction system.
The main computing problem which Innok Robotics solves is SLAM – Simultaneous Mapping and Localization. While a warehouse AGV operates in a stable, confined, flat environment, outdoors there are no boundaries, the terrain must be mapped and traversed in 3D, and the scene constantly changes as plants grow or are pruned, cars are parked or driven away, and so on.
Innok Robotics has developed a solution to this problem which can be applied in a wide variety of user-defined spaces. Its solution depends in part on an ability to continuously track in precise detail the movement of the AGV from a known starting point in all three dimensions. For this function, Innok Robotics has selected for its modular development platforms an Xsens MTi-30 AHRS (Attitude and Heading Reference System), a type of motion tracker which measures acceleration in 3D, and heading by reference to magnetic North. The AHRS fuses the raw acceleration data with data from its gyroscopes and magnetometers to produce estimates of roll, pitch and yaw which are updated at a rate of up to 400Hz.
A typical example of the way that Innok Robotics’ SLAM technology is implemented is a specialist AGV, Rainos – a fully automated system for watering the floral displays and flower beds planted at graves in graveyards.
This is a highly specialized application for robotics, but it has a high value for professional gardeners, who are typically employed by families to water the graves of their loved ones. Performed manually, this irrigation task is tedious, laborious and time-consuming, but is not paid well. This makes it an ideal application for robotics.
The Rainos AGV – an automatic system for watering graves
Innok’s Rainos AGV performs the task entirely autonomously – but it can only do so because it is a teachable robot: in the initialization phase, the gardener ‘shows’ Rainos how to perform the task. Using a remote control, the gardener guides the AGV along all permitted routes, and tags the locations of graves to be watered, and of water refill points. Crucially, the gardener will also record the AGV’s parking station – the known start point from which each irrigation session begins.
During initialization, the Rainos AGV will create its own map of the graveyard, using inputs from three sources:
· A LiDAR sensor which builds a 3D map of the scene
· Odometry – motion data derived from the turning of the wheels
· A motion tracker, which provides 3D motion data and heading information
After initialization is finished, the Rainos AGV has a complete 3D map of the graveyard, the routes by which it is able to travel round the graveyard, and the locations in which it must perform watering operations.
This is how Innok Robotics’ products solve the SLAM problem in real time: an Innok Robotics AGV can determine its position by a process of dead reckoning from a known starting position, using accurate, low-drift motion and heading data from an MTi-30 AHRS. And a combination of the stored map and real-time ranging inputs from a LiDAR sensor make it aware of its environment, even as the surroundings change due to factors such as the growth or pruning of vegetation, or the appearance or removal of obstacles. A powerful on-board computer enables the AGV to re-calculate its route continually to avoid obstacles while still completing its mission.
An Innok Robotics AGV showing the Xsens MTi-30 motion tracker on the center cross-bar
Innok Robotics’ Direct of Sales Alexander Hoegerl says that the company’s technological achievement depends on sensor fusion – combining multiple data inputs to create a more detailed and accurate picture of the environment around the AGV than any one sensor could provide on its own.
He says: ‘The data from the motion tracker is a crucial element of our AGVs’ position calculations, so the accuracy and low drift of the MTi-30 are really important attributes. It’s a robust device as well – its IP65 rating means that it is suitable for use outdoors, and that gives us the freedom to locate the sensor wherever the design requires.
‘What makes the MTi-30 particularly attractive for us is that it is also easy to implement in new designs. In our business, which involves constantly creating new prototypes and systems for specific applications, we have to manage development time carefully, and so it’s really helpful to us that the Xsens AHRS is easy to integrate into our system designs.’
- |
- +1 赞 0
- 收藏
- 评论 0
本文由宝丁转载自XSENS,原文标题为:Robotics Specialist Innok Robotics Uses Sophisticated Sensor Fusion To Locate AGVs In Outdoor Space,本站所有转载文章系出于传递更多信息之目的,且明确注明来源,不希望被转载的媒体或个人可与我们联系,我们将立即进行删除处理。
相关推荐
Xsens MTi-30 AHRS惯性传感器提供精确数据进行精准定位,以厘米级的精度追踪AGV的位置
生产出一款可以在室外混合地形上部署的AGV,很少有公司能完成这一艰巨的挑战。来自德国的Innok Robotics公司是这一领域的先驱之一。Innok Robotics使用Xsens MTi-30 AHRS惯性传感器提供的精确数据来进行精准定位,以厘米级的精度追踪AGV的位置。
Advanced HamiltonJet Propulsion Control System Uses MTi Motion Tracker to Keep A Boat Still on Moving Water
HamiltonJet‘s JETanchor product for station keeping, or providing a ‘virtual anchor‘, is an optional feature of the AVX propulsion control system. Playing a vital role in the JETanchor‘s position sensing system is an MTi-2 Vertical Reference Unit (VRU) from Xsens. The accuracy and stability of the MTi-2 VRU enable the JETanchor product to achieve high performance. It can typically maintain a vessel‘s position to within 1m at sea. System tests have demonstrated the system‘s ability to maintain a cargo vessel‘s station 1m from a wharf while a 1 tonne load of bricks was lifted by crane to shore.
【应用】ACSL公司自主航空无人机选择Xsens MTi-30运动传感器提供快速精准的姿态和运动数据
ACSL公司全自主航空飞行无人机MS-06LA通过采用Xsens MTi-30运动传感器,为飞行控制提供快速精准的姿态和运动数据,并为创新技术提供传感器数据。
Xsens IMU惯性测量传感器选型指南
目录- IMU
型号- MTI-1,MTI-2,MTI-600,MTI-300,MTI-7,MTI-100,MTI-200,MTI-G-710,MTI-3,MTI-680,MTI-670,MTI-610,MTI-620,MTI-630
XSENS MTi系列MEMS惯性传感器选型指南
型号- MTI 100-系列,MTI 1-系列,MTI-G-710,MTI 1系列,MTI 600系列,MTI 600,MTI-670,MTI 1,MTI-610,MTI-630,MTI 100,MTI-1,MTI-680G,MTI,MTI-2,MTI-670G,MTI-7,MTI系列,MTI-3,MTI 600-系列,MTI-680,MTI-200,MTI-100,MTI 100系列,MTI-620,MTI-300
XSENS Motion Tracker Helps Innok Robotics Pioneers Sensor Fusion Agv Location In Complex Outdoor Terrains
It is generally easier to design automated ground vehicles (AGVs) for indoor than for outdoor use. Inside a warehouse, for instance, an AGV moves on a smoothly finished, flat surface, in an area enclosed by walls, and along fixed, dedicated routes which are marked with barriers or guidelines for navigation, and which eliminate the risk of collision with people or other objects.
Xsens MTi系列MTi系列参考手册的一般信息
描述- 本资料为Xsens MTi系列产品的参考手册,主要介绍了MTi系列产品的硬件平台、系统概述、安装技巧、保修和责任等内容。手册详细阐述了MTi系列产品的功能、特点、使用方法以及与Xsens软件套件(MTSS)的配合使用。此外,还提供了MTi产品的技术参数、数据输出协议、接口选项等信息。
型号- MTI 600-SERIES,MTI SERIES,MTI-G-710,MTI-670,MTI-610,MTI-630,MTI 10-SERIES,MTI-30,MTI-10,MTI-680G,MTI-1,MTI,MTI-2,MTI-7,MTI 1-SERIES,MTI 100-SERIES,MTI-3,MTX,MTW,MTI-200,MTI-100,MTI-G,MTI-620,MTI-300,MTI-20
【产品】基于MEMS的惯性IMU单元MTi 10系列,可提供IMU,VRU和AHRS三种集成度的产品
Xsens推出的MTi 10系列是基于MEMS的惯性IMU单元,能够提供可靠及灵活的解决方案。借助AHRS,VRU和IMU,该系列产品为系统集成商提供了三种不同的集成级别。该模块基于行业认可的,具有成本效益的,基于MEMS的方向传感器,并具有集成的、功能齐全的传感器融合算法和易于使用的SDK。
所有MT设备的MT Manager用户手册
描述- 本手册为Xsens MT Manager用户指南,适用于所有MT设备。内容涵盖MT Manager的安装、配置、基本功能、操作指南、系统要求等。MT Manager是一款易于使用的软件,具有Windows用户界面,可实时查看3D方向、惯性传感器和磁力传感器数据,实时查看纬度、经度、高度,通过消息终端与设备进行通信,导出日志文件到其他格式,更改和查看各种设备设置和属性,运行自检以检查惯性传感器和磁力计的机械功能。支持多种MT设备,包括MTi 1系列、MTi 10/100系列、MTi 600系列等。
型号- MTI 600-SERIES,MTI-680G,MTI,MTI-7,MTI-G-710,MTI 1-SERIES,MTI 100-SERIES,MTX,MTW,MTI-670,MTI-G,MTI-300,MTI-20,MTI-30,MTI 10-SERIES
ISM简介
型号- 1-SERIES,100-SERIES,MTI-6#0,MTI-#00,MTI-G-710,MTI-#0,MTI-670,MTI-610,MTI-630,MTI-#,MTI-30,MTI-1,MTI-680G,MTI-2,MTI-SERIES,MTI-630-DK,MTI-SERIES™,MTI-3-DK,MTI-7,10-SERIES,MTI-680R,600-SERIES,MTI-3,MTI-7-DK,MTI-#00-DK,MTI-680,MTI-670-DK,MTI-200,MTI-100,MTI-620,MTI-300,MTI SERIES™
MTI-300高性能姿态航向和基准系统(AHRS)
描述- MTi-300是Xsens公司的高性能姿态和航向参考系统(AHRS),具备高精度的姿态和航向测量能力,适用于复杂环境下的惯性数据采集。该产品支持优化温度校准、高频输出,并可通过配置输出设置与第三方设备同步。MTi-300是MTi 100系列的一部分,由MT软件套件支持,包括MT Manager(Windows/Linux的GUI)、SDK、示例代码和多个平台的驱动程序。
型号- MTI-300,MTI 100-SERIES
厘米级精度、集成RTK的惯导产品MTi-680G的应用
描述- 该资料介绍了Xsens公司生产的MTi-680G惯性导航产品,该产品集成了厘米级精度的RTK技术,适用于小型自主车辆和机器人。MTi-680G具备GNSS/INS定位功能,支持GPS、GLONASS、Galileo、北斗等卫星系统,并提供了CAN、RS232/USB接口。资料还详细说明了RTK校正消息的获取方式,包括使用NTRIP服务器或自建基站,并提供了客户集成指南。
型号- MTI-680,MTI-680G,MTI-G-710,MTI 100-SERIES,MTI SERIES™,MTI 10-SERIES,MTI-680G-SK
现货市场
登录 | 立即注册
提交评论