The Inside Story on a Solution for Evaluating 300A~4800A High-Power Battery Performance
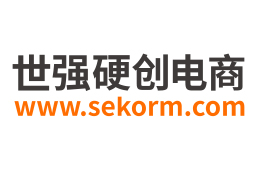
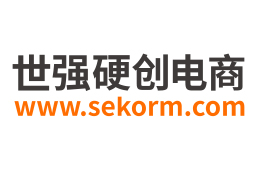
In a bid to develop electric vehicles (EVs) that offer both safety and high performance, battery researchers are dedicated to improving the energy density, cycle life, and safety of automotive battery cells. To ensure these development efforts comply with regulations and performance standards, engineers must rely on professional and efficient equipment to perform a range of rigorous battery tests.
Q1. Important ways of verifying the performance of automotive battery cells include fixed-load and high-speed dynamic load evaluation. What aspects should users take into account when choosing the appropriate equipment for such high-current tests?
A1. With the development of fast charging and racing modes for electric vehicles, the battery cells require a higher current capability. Coupled with the increased capacity of individual battery cells, test currents can reach several hundreds or even thousands of amperes. If your equipment specification is defined based on the peak testing current, you’re looking at much higher equipment prices. However, as the high-rate current mode tests involve short-duration high-current pulses, by purchasing test equipment capable of outputting such pulses you can significantly reduce your equipment procurement costs.
Q2. What benefits does energy recovery (regenerative) design in battery cell charge-discharge equipment offer in terms of battery cell testing?
A2. To be sure, the conversion efficiency of energy recovery in battery cell charge-discharge equipment is not as high as that of battery packs due to the low operating voltage of battery cells. However, battery cell testing involves numerous test items and long verification cycles, often requiring a large number of channels to perform validation of battery products. Over time, a significant amount of the energy discharged during this process can be recovered. The energy recovery design not only saves long-term operational costs but also reduces the costs associated with facility power distribution and air conditioning. Furthermore, the high power density of energy recovery-based charge-discharge equipment can reduce the overall equipment footprint and lower carbon emissions, helping manufacturers achieve efficient and sustainable production.
Q3. What conditions should the charge-discharge test equipment meet when used for evaluating the performance of automotive batteries and ensuring compliance with the test requirements of international vehicle manufacturers?
A3. The evaluation of automotive battery cells focuses on dynamic performance testing, such as the Hybrid Pulse Power Characteristic (HPPC) test defined by USABC, the dynamic stress test according to IEC 62660, etc. Test equipment with short current response time and charge-discharge switching time is preferable. The faster the response speed, the higher the output fidelity. There should not be any significant current overshoot, as this can cause transient over-potential and result in varying degrees of damage to the battery, affecting the final experimental results. In addition, crossover delay between charge and discharge transitions should be avoided, as the crossover time directly affects waveform distortion. In terms of measurement, a fast sampling rate reduces errors in the calculation of dynamic capacity, while a shorter data recording cycle can better capture the dynamically changing characteristics, improving the accuracy of internal resistance and power calculations. The accuracy of voltage/current measurement should be as high as possible, but attention should also be paid to the specifications for accuracy and data smoothing cycles. While smoothing enhances precision, it can distort dynamic measurements, so it should be consistent with the minimum recording cycle. Additionally, high-current test equipment should have multiple current ranges to reduce errors in low-current measurements.
Q4. Are there any other key points to consider with respect to testing automotive battery cells?
A4. Safety testing should incorporate the appropriate safety mechanisms based on the EUCAR Hazard Level defined for the product development stage of the battery cells. The equipment should also have abnormal data detection capabilities to identify any anomalies and prevent further testing of faulty cells. The test equipment itself should also have a multi-layer protection mechanism to ensure safety even in the event of a single circuit failure. Additionally, it is important to integrate external safety mechanisms such as fire suppression systems and safety chambers equipped with smoke, gas, and temperature detection capabilities. These external safety measures, along with appropriate protective action mechanisms based on safety engineering design, help minimize potential damage.
Q5. What value does CHROMA’s new product bring to users?
A5. Chroma's new charge-discharge testing system, the 17010H, has been developed specifically for high-current performance testing applications above 300A. As traditional non-regenerative charge-discharge test equipment consumes a significant amount of energy and generates substantial waste heat in this range, it is bound to be phased out due to global decarbonization trends. Still, non-regenerative equipment does offer some advantages, such as rapid current response and high accuracy. The Chroma R&D team has been hard at work to design regenerative circuitry that achieves performance comparable to non-regenerative systems. We are proud to announce that the result is a high-performance and superbly efficient solution for high-current testing of automotive battery cells. Two technological advancements are especially notable: (1) the Super Mode function and (2) a 10% increase in energy conversion efficiency.
- |
- +1 赞 0
- 收藏
- 评论 0
本文由翊翊所思转载自CHROMA News,原文标题为:The Inside Story on a Solution for Evaluating 300A~4800A High-Power Battery Performance,本站所有转载文章系出于传递更多信息之目的,且明确注明来源,不希望被转载的媒体或个人可与我们联系,我们将立即进行删除处理。
相关推荐
【经验】使用Chroma 66205数位功率表测试产品直流功耗操作详细介绍
电子产品设计中,经常会需要功率和功耗的测试,测试直流低功耗可以使用专业的功耗分析仪N6705C+N6781A,这个价格比较高。如果暂时没有功耗分析仪,一般的交流功率表也可以测试功耗,精度略低一点。今天我们以CHROMA的数位功率表66205为例,来实际测试一下产品功耗。
【经验】如何解锁直流电子负载Chroma 63600的UDW功能操作
UDW功能主要应用在一些特殊电流波形拉载。通过直流电子负载Chroma 63600 Soft Panel软件Download到负载中。例如电动车通过不同路况下电池使用情况,我们可以通过示波器抓取电流波形,将数据保存为“CSV”格式,回到实验室将波形Download到负载来模拟。例如功放电源测试时,电流波形类似“馒头波”,可以通过处理正弦波来得到类似“馒头波”,然后Download到负载来模拟。
【经验】Chroma 8000用在电动车交流车桩交互流程测试的教程
如今,电动车已经成为现代人出行的重要交通工具,Chroma深耕电动车测试领域,今天小课堂为大家带来——GB标准交直流车桩交互应用介绍。
Chroma携新型电驱动总成测试系统1210等产品重点亮相2024上海汽车测试及质量监控博览会
Chroma推出新型电驱动总成测试系统1210,应用在纯电动乘用或商用车与氢燃料电池混合等车型之动力系统,提供新能源汽车动力系统模拟测试,试验件涵盖电机、电机控制器、变速箱及电力驱动系统等。Chroma携一系列新热产品重点参展2024上海汽车测试及质量监控博览会。
Chroma 17010H Battery Reliability Test Solution for Lithium Batteries with Ultra-low DC Internal Resistance, Achieving 200% Pulse Current Output
The single channel current capacity of Chroma 17010H is 300A, which can be amplified with Super Mode to output 200% current (600A) within 30 seconds, especially suitable for pulse current performance testing.
CHROMA一站式电池芯充放电测试解决方案,为测试安全性加强把关
CHROMA 17010/17010H电池芯充放电测试系统多年来在世界各大知名电芯厂、车厂、储能系统厂中之所以获得采纳与肯定,除了在充放电量测性能上的高精准度、低输出噪声、以及软件和硬件多重安全保护以外,可弹性整合安全型环境箱的控制指令,基于安全管制矩阵构建一站式测试系统,发生测试危害时,让温箱与充放电设备透过讯号交联来即时限缩危害范围,协助客户安全地完成电池测试任务。
电池测试解决方案电池单元/电池模块/电池组
描述- Chroma ATE Inc.作为全球领先的自动化测试设备供应商,提供电池测试解决方案,包括电池单体、模块、包、管理系统(BMS)、车载充电器、直流转换器、电动汽车充电站(EVSE)、无线充电器和电气安全测试。公司提供全面的测试解决方案,涵盖电池生产线的自动化测试系统,包括形成、分级、预充电、OCV/ACIR站、DCIR站等测试设备,以及自动化堆垛起重机、输送带、物流控制系统、分组、分类和返工站等自动化设备。Chroma还提供电池实验室管理系统的解决方案,包括电池测试监控系统(BTMS)和电池实验室管理解决方案。此外,Chroma还提供电池模块/包维护自动化测试系统,以及电池功率HIL测试解决方案。
型号- 8630,19311 SERIES,17216M-6-12,17010H,17020,17040E,17000,17020E,8610,63200A,17040,19055-C,63200E SERIES,17208M-5-12C,63200A SERIES,17000 SERIES,17208M-6-30,17212M-6-100S,A170103,63200E,17216-6-6,A190362,17010,8700,19311,8720,62000D SERIES,62000H,19311-10,62000D,62000E,17091,17216M-10-6,17216-6-12,62000E SERIES,17010H_6-300S,62000H SERIES,11210,17010H_6-300,17010H_6-300U,19032-P,A112100,17208M-6-60,87001,17010H_6-300Z
【应用】基于致茂锂电池芯17010H的锂电池测试解决方案,体积减小50%,比满功率设计方案直接降本30%
CHROMA锂电池芯17010H单通道电流能力300A,超级模式30秒内能输出电流200% (600A),此项新设计聚焦于电池脉冲电流应用进而优化功率输出模式,具有体积减小50%、相较满功率设计方案直接成本降低30%的优势。
Chroma携创新电池测试解决方案亮相2024年CIBF展会
2024年CIBF展会(4/27~29)即将在美丽的山城——重庆盛大开幕!汇聚2200家行业内知名企业,交流行业信息,探讨电池技术发展方向。Chroma深耕电池行业多年,将携最新的电池测试相关解决方案参与此次盛会,愿与广大行业内先进一起学习交流。
17010H型电池可靠性测试系统
描述- Chroma 17010H电池可靠性测试系统是一款高精度充电放电测试设备,专为高性能和高电流测试设计。该系统适用于大型锂离子电池单元(LIB)、超级电容器(EDLC)和锂离子电容器的性能评估、寿命周期测试和产品选择。
型号- 17010H,17010H-6-300Z,MODEL 17010H,17010H-6-300,17010H-6-300S,17010H-6-300U
【产品】Chroma新推可达4800A的电池芯倍率电流测试解决方案17010H,提升能源回收效率达75%
电池在储能应用方面肩负电力调节任务,大容量与倍率电流能力同样被要求,但大容量且高电流倍率的电池芯常受限于设备而无法进行完整的测试,Chroma推出全新的17010H电池信赖性测试系统,为您提供200%的脉冲输出能力与信道并联功能满足4800A以下的电池芯测试需求。
電池信賴性測試系統 BATTERY RELIABILITY TEST SYSTEM MODEL 17010H
描述- Chroma 17010H电池芯信赖性测试系统是一款专为高电流/高功率性能测试设计的专业充放电测试设备,适用于大型锂离子电池芯(LIB Cells)、电气二重层电容器(EDLCs)和大量产热的控制电路。该系统具备高测量精度、高供通道并联功能、快速电流响应、放电能源回收等功能,旨在提高实验室内电池芯试验的电容量测试精确度和性能参数辨别。
型号- 17010H,17010H-6-300Z,MODEL 17010H,17010H-6-300,17010H-6-300S,17010H-6-300U
电池测试解决方案 电池芯/电池模组/电池包
描述- Chroma ATE Inc. 提供全面的电池测试解决方案,涵盖电池芯、电池模组、电池包等各个阶段。公司提供包括电池芯化成、分容、预充等测试系统,以及电池模组和电池包的充放电测试系统。此外,Chroma还提供电池管理系统(BMS)功能性测试系统、电池包生产线测试方案、电池模组和电池包维护保养测试系统等。公司产品广泛应用于电动汽车、储能系统等领域。
型号- 17040E,17000,17020E,8610,63200A,17040,17010系列,17212M-6-100S,62000H 系列,63200E,62000D 系列,17216-6-6,17010,8700,19311,62000H,62000D,62000E,17091,17216M-10-6,17010H_6-300S,17010H_6-300,17010H_6-300U,17010H_6-300Z,8630,17010H,17020,17216M-6-12,19055-C,17208M-5-12C,17208M-6-30,32S,96S,A170103,A190362,8720,19311-10,19311系列,17000系列,63200A系列,63200E 系列,17216-6-12,11210,62000E 系列,19032-P,87001,A112100,17208M-6-60,A112101
Chroma携17010/17010H电池信赖性测试系统以及电池测试相关明星机种,精彩亮相CIBF 2023
本次CIBF,Chroma展出了电池信赖性测试系统/电池综合性线下测试系统(EOL)/电池包整合测试台架系统(PHiL),以及电池测试相关的明星机种,获得新老客户好评如潮。Chroma 17010/17010H电池信赖性测试系统是专为锂离子电池芯、电气二重层电容器与锂离子电容器等储能元件测试而开发的专业充放电测试设备,适用于产品开发、性能评价、寿命验证与产品选型等用途。
MODEL 17010H 电池信赖性测试系统 BATTERY RELIABILITY TEST SYSTEM
描述- Chroma 17010H电池芯信赖性测试系统是一款专为高电流/高功率性能测试设计的专业充电放电测试设备,适用于大型锂离子电池芯(LIB Cells)、电气二重层电容器(EDLCs)和大量产热的控制电路。该系统具备高测量精度、高供通道并联功能、快速电流响应、放电能量回收等功能,旨在提高电池芯实验的电容量测试精确度和性能参数验证。
型号- 17010H,17010H-6-300Z,MODEL 17010H,17010H-6-300,17010H-6-300S,17010H-6-300U
电子商城
登录 | 立即注册
提交评论