Renesas MCU Families Developed with Robust & Reliable Motor Control for Industrial Domain

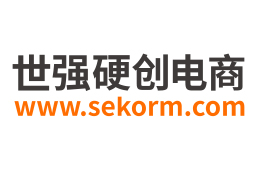

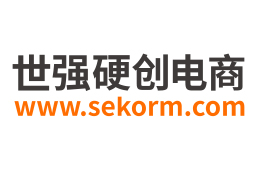
Industry 4.0 enables stakeholders to optimize facilities and increase productivity through interconnected industrial equipment and enhanced computation. It presents an excellent opportunity to assist stakeholders in utilizing converging technology to create a sustainable, human-centered future, where motors stand as vital contributors across industries. Figure 1 illustrates the process of identifying and implementing Industry 4.0, where the Internet of Things (IIoT) enables devices to link, creating a virtual duplicate of real-world data. This facilitates operators to visualize and analyze processes, enabling them to make decisions to autonomously perform tasks as efficiently as possible.
Figure 1. Design Principles of Industry 4.0
Induction motors (IM) play a crucial role in Industrial domains as the main workhorse for maintaining efficient movement. Their proven reliability, versatility, and economic advantages make them the preferred choice for industrial applications. In the past, IMs were primarily used for single operating point applications, operating at rated torque and speed. However, advancements in motor control have expanded their usability across a wide range of torques and speeds, making them highly adaptable to different industry needs. Nowadays, almost all motion solutions have transitioned from pneumatic or manual operation to motorized systems.
The key requirements for motor controls across industries include:
Maintaining stable operation across a wide range of loads.
Ensuring quick and precise response.
Supporting various position feedback sensors like encoders, resolvers, hall sensors, etc.
Handling electrical noise and interference in feedback signals (current, voltage, temperature).
Achieving high efficiency.
Meeting the highest standards of reliability and functional safety.
Being compact and lightweight.
Supporting different industrial communication protocols such as UART, I2C, CAN, etc.
The induction motor operates on the principle of electromagnetic induction. The rotating magnetic field created by the stator excitation induces an electromotive force (EMF) in the rotor. As a result, currents flow through the rotor, producing torque and facilitating rotation. Thus, precise control of the stator excitation becomes crucial for effective induction motor control. Speed control for induction motors is typically classified into two main categories:
1. Scalar control. The majority of existing variable speed drive systems are low-performance drives that control the magnitude of the frequency of the stator voltage or current. The control is achieved by maintaining a constant magnetic field in the motor. The most commonly used scalar control method is Constant Volts/Hertz (V/f) control, wherein the magnitude of the stator voltage is adjusted in proportion to the frequency, thus keeping the stator flux constant in the motor. Although scalar control methods are relatively easy to implement, they are not suitable for applications involving transients on the load side. Below are shown the typical motor characteristics achievable with V/f control.
Figure 2. Torque speed characteristic of IM with V/f control
2. Vector control. In contrast to scalar control, vector control of IM is based on field-oriented control (FOC) schemes. This method provides control of the phase and magnitude of vector quantities of the motor. Vector control drives are considered high-performance drives with control over instantaneous torque and magnetic field of the motor both under steady-state and transient conditions. Despite being computationally demanding, vector control outperforms scalar control, particularly in dynamic conditions. Vector control implementation involves estimation of rotor flux from either stator voltage or currents using flux observers which requires accurate sensing and fast computation.
Figure 3. Vector control system for an induction motor with flux estimation
For modern applications, motors must operate on a wide operating range and under dynamic conditions, requiring vector control schemes to meet these demands effectively. Given the sensing and computational requirements, the careful selection of the appropriate microcontrollers (MCUs) is crucial for developing a robust induction motor control solution.
Figure 4. Typical block diagram of induction motor drive with RENESAS microcontrollers
Figure 4 illustrates a typical induction motor drive and its major components. The induction motor drives receive power from a 3-phase AC input supply, which undergoes conversion into DC voltage through a rectifier unit. To reduce voltage ripple, DC link capacitors are placed across this output DC voltage. The DC voltage is then fed into the inverter, which converts it back into AC for the induction motor, based on the switching signals received by the MCU. The MCU, being the brain of the drive, plays a vital role in determining the performance and efficiency of the induction motor drive. For IM drive applications, the Renesas RA-T and RX-T MCU series have been meticulously designed with specific functions that help in the development of high-performance drive systems. Let's explore some key features of these MCUs below.
PWM generation. High-frequency PWM generation is critical for achieving lower THD in current waveforms and smooth control of any motor. RA-T and RX-T MCUs can support up to 200 MHz frequency 3-phase complimentary PWM generation. These high-frequency PWM generations make them ideal for inverters with advanced GaN and SiC-based power switches, capable of operating on very high switching frequencies.
Trigonometric functions. Any advanced control scheme like vector control or other FOC control requires computation of torque and flux in real time which involves the implementation of many trigonometric functions. Renesas MCUs offer dedicated arithmetic units for trigonometric functions (TFU) which greatly reduce the computational time and increase the accuracy of the calculation. Other floating point operations required for motor control applications can be performed at a processing speed of 200 MHz.
Feedback control. RA-T and RX-T MCUs have in-built 12/16-bit A/D converters. These ADCs can sample 3 currents simultaneously for accurate current control and switching state determination. To read feedback from encoders, dedicated phase counting modes ensure the capability to read encoder input up to 32-bit resolution.
Communication interface. Motor drives play a vital role within automation and processing industries as they are integral components of larger control systems and facilitate communication with master controllers and peripheral devices. Therefore, MCUS must be compatible with industry-standard communication protocols. Renesas MCUs can be integrated with larger systems seamlessly using communication interfaces such as SCI, CAN, I2C, RSPI, USB, and extended industrial protocols like Ethercat & Ethernet-IP.
Renesas offers a complete development environment for rapid and reliable product development. The development environment provides dedicated solutions for every important stage of software and hardware development along with technical support provided by the Renesas team.
Figure 5. Renesas rapid development tools for motor control solutions
Recent times have witnessed an unprecedented acceleration in technological development, primarily driven by advancements in information technologies and digital computations. These developments are not mere incremental progressions but rather mark the inception of a new technological revolution known as Industry 4.0 (IR 4.0). At the center of this revolution lie the game-changing technologies of Artificial Intelligence (AI), machine learning, and data analytics.
In summary, the future is a seamless integration of the cyber-physical world. Considering the importance of motor controls for industrial applications, the new solutions have to complement these aspirations, and the capabilities of MCUs to play a vital role in achieving this goal. Renesas RX-T and RA-T MCU families have been developed with dedicated motor control features along with secure and fast data communication capabilities to meet the requirements of IR 4.0 and thus make an ideal choice for a robust industrial motor control system.
- |
- +1 赞 0
- 收藏
- 评论 0
本文由玄子转载自RENESAS Blogs,原文标题为:Robust & Reliable Motor Control for Industrial Domain,本站所有转载文章系出于传递更多信息之目的,且明确注明来源,不希望被转载的媒体或个人可与我们联系,我们将立即进行删除处理。
相关推荐
Geehy APM32F407 Industrial-grade MCU Used for Power Optimizer Solution Safeguards PV Power Generation Efficiency
The APM32F407 industrial-grade high-performance MCU not only has the high computing and high security required for complex applications in new energy but also offers a variety of ways to simplify the complex design.
Geehy APM32F407 Low-Voltage Servo Drive Solution that Can Operate Reliably in A Variety of Industrial Applications
Geehy Semiconductor APM32F407 low-voltage servo drive solution is a high-performance and compact solution that can operate reliably in a variety of industrial applications. The main control MCU supports integrated design for servo motor systems and provides a wide range of peripheral interfaces.
Renesas RX72M Microcontroller Wins the “2021 Intelligent Manufacturing MCU Outstanding (Product) Solution“ Award of China Electronics News
Renesas RX72M Microcontroller Wins the “2021 Intelligent Manufacturing MCU Outstanding (Product) Solution“ Award of China Electronics News. Award-winning MCU RX72M has a wealth of built-in analog circuitry, such as the 12-bit ADC with over 20 channels, three independent sample-and-hold circuits, operational amplifiers, PWM timers, and the 24-bit Delta-Sigma ADC for motor drive control.
Silicon Labs(芯科科技)EFM8™ 8位MCU选型指南
型号- EFM8UB20F32G,EFM8UB20F64G,EFM8,EFM8SB20F64G,SLSTK2000A,SLSTK2022A,SLSTK2010A,SLSTK2020A,SLSTK2030A,EFM8UB10F8G,EFM8SB20F32G,EFM8SB20F16G,SLTB005A,EFM8LB11F32E,EFM8UB11F16G,EFM8SB10F2G,EFM8BB21F16G,EFM8SB10F4G,EFM8LB11F16E,EFM8BB10F2G,EFM8SB10F8G,EFM8 FAMILY,EFM8LB12F64E,EFM8LB10F16E,EFM8LB12F32E,EFM8UB10F16G,EFM8UB31F40G,EFM8BB31F32G,EFM8BB31F64G,SLSTK2001A,SLSTK2011A,SLSTK2021A,EFM8BB10F4G,EFM8BB31F16G,EFM8UB30F40G,EFM8BB10F8G,EFM8BB22F16G
Cmsemicon Newly Launches 32-bit Industrial-Grade MCU BAT32G439 Series Operating at a Frequency of 128MHz
Cmsemicon recently expanded its BAT32G series with the addition of the 32-bit industrial-grade MCU family member, BAT32G439. It supports an industrial temperature range of -40℃ to 105℃, offering high reliability, rich peripheral resources, and powerful digital signal processing capabilities.
Silicon Labs(芯科科技)Gecko系列32位MCU选型指南
目录- Gecko™MCUs Energy-friendly microcontrollers
型号- EFM32G,EFM32LG,EFM32GG11B,EFM32GG12B,EFM32PG,EFM32TG,EFM32TG11B,EFM32HG,EFM32GG,EFM32WG,EFM32ZG,EFM32JG
Geehy‘s First Motor Control Dedicated MCU - APM32F035: Operating at a Frequency of 72MHz
Based on the Arm® Cortex®-M0+ core, operating at a frequency of 72MHz, Geehy Motor Control Dedicated MCU APM32F035 supports MDU+Cordic and CRC for superior motor processing performance. With 64KB Flash and 10KB SRAM, it fulfills various embedded motor application algorithm requirements.
Cmsemicon Officially Launches Industrial-Grade MCU Chip BAT32G113 for Space-Constrained Applications
Cmsemicon has officially launched the industrial-grade MCU BAT32G113. The chip operates at a temperature of ranging from -40℃ to 125℃ and is available in QFN24 (3mmx3mm) and QFN32 packages. It is primarily targeted at space-constrained applications such as optical modules.
基于Z16FMC单片机的无位置传感器无刷直流电机控制
描述- 本资料探讨了使用Z16FMC微控制器对三相无刷直流电机进行闭环控制的方法。Z16FMC系列微控制器专为电机控制应用设计,具有片上集成的应用特定模拟和数字模块,使用MultiMotor开发套件,实现快速精确的故障控制、高系统效率、实时速度/扭矩和方向控制,以及易于为定制应用开发固件。资料详细介绍了使用相位锁定环和反电动势传感实现无传感器反馈控制系统的方法,并提供了基于MultiMotor开发套件和Z16FMC微控制器模块的测试结果。
型号- Z16FMC
Cmsemicon Launches CMS8S589x of High-Capacity 8051 Series Microcontrollers with Arbitrary GPIO Mapping
The new microcontroller CMS8S589x is designed for all digital functions to be arbitrarily mapped to GPIOs, making hardware design easier, while providing rich communication interfaces for consumer electronics, industrial, energy storage, IoT, and other applications.
Geehy‘s Industrial-Grade Cost-Effective MCU APM32F003 Attains Functional Safety Certification Meeting IEC 60730/60335 Standards
Based on the Arm® Cortex®-M0+ core, operating at an operating frequency of 48MHz, the APM32F003 MCU boasts a wide temperature range, high precision, low-temperature drift, and an impressive ESD level of up to 8KV, showcasing robust anti-interference capabilities.
Cmsemicon Launches the New Industrial-Grade Low-Power MCU BAT32G127 with 32MHz Operating Frequency For Low-Power LCD Display Applications
Cmsemicon has officially released the new industrial-grade low-power MCU BAT32G127, which is designed to simplify battery-powered LCD display applications with strong resource scalability and excellent low power consumption.
MindMotion Announces the High Performance Motor Specific MM32SPIN0280 Series Microcontrollers with a Frequency of up to 96MHz
MindMotion new high-performance motor-specific MM32SPIN0280 series microcontrollers are 32-bit microcontrollers based on the high-performance Arm® Cortex®-M0 core, operating at a frequency of up to 96MHz, with built-in high-speed memory, an extensive range of enhanced I/O ports, and peripherals.
MindMotion Published New 12-Inch Microcontrollers MM32F0020 Series Offering 32KB Flash and 2KB SRAM
The MM32F0020 series MCU is suitable for a wide range of automotive, industrial, and consumer markets. Typical applications include chargers, battery management, cooling fans, smoke sensors, toys, motors, and 8/16-bit MCU upgrades and replacements.
基于Z8FMC16100单片机的无刷直流电机正弦PWM调制控制
描述- 本应用笔记介绍了使用Zilog Z8FMC16100系列微控制器(MCU)在正弦PWM调制模式下控制三相无刷直流电机的技术。该笔记详细讨论了如何实现正弦PWM调制和相位角同步,并基于Z8FMC16100 MCU模块、三相MultiMotor开发板和带内部霍尔传感器的三相24VDC 30W 3200RPM BLDC电机进行操作。内容涵盖了电机控制、速度/扭矩控制、故障保护和系统效率等方面。
型号- Z8FMC16100,Z8FMC16,99C1395
电子商城
现货市场
服务
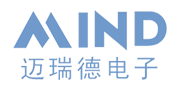
可定制显示屏的尺寸0.96”~15.6”,分辨率80*160~3840*2160,TN/IPS视角,支持RGB、MCU、SPI、MIPI、LVDS、HDMI接口,配套定制玻璃、背光、FPCA/PCBA。
最小起订量: 1000 提交需求>
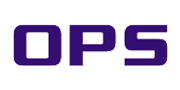
可烧录IC封装SOP/MSOP/SSOP/TSOP/TSSOP/PLCC/QFP/QFN/MLP/MLF/BGA/CSP/SOT/DFN;IC包装Tray/Tube/Tape;IC厂商不限,交期1-3天。支持IC测试(FT/SLT),管装、托盘装、卷带装包装转换,IC打印标记加工。
最小起订量: 1pcs 提交需求>
登录 | 立即注册
提交评论