碳化硅器件封装进展综述及展望相关文章集锦

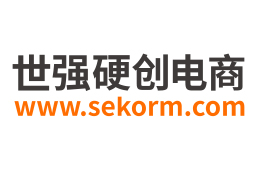

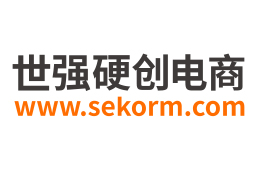
碳化硅器件封装进展综述及展望
杜泽晨 张一杰 张文婷 安运来 唐新灵 杜玉杰 杨霏 吴军民
(全球能源互联网研究院有限公司 先进输电技术国家重点实验室)
碳化硅(SiC)具有禁带宽、临界击穿场强大、热导率高、高压、高温、高频等优点。应用于硅基器件的传统封装方式寄生电感参数较大,难以匹配SiC器件的快速开关特性,同时在高温工况下封装可靠性大幅降低,为充分发挥SiC器件的优势需要改进现有的封装技术。针对上述挑战,对国内外现有的低寄生电感封装方式进行了总结。分析了现有的高温封装技术,结合新能源电力系统的发展趋势,对SiC器件封装技术进行归纳和展望。
1引言
随着我国的能源占比和能源消费方式由以化石能源为主转变为以电能、氢能等清洁能源为主,2020年9月,习近平主席在联大宣布:中国将采取更加有力的政策和措施,二氧化碳排放力争于2030年前达到峰值,努力争取2060年前实现碳中和。2021年3月,中央财经委员会第九次会议提出构建以新能源为主体的新型电力系统。
碳化硅(SiC)禁带宽、临界击穿场强大、热导率高,是第三代半导体的典型代表,SiC材料、器件已经列入国家“十四五”科技规划,其具有电压高、损耗低、耐高温工作等优势,对于电力电子装备高效化、小型化具有重要作用。
SiC材料的这些优良特性,需要通过封装来实现功率和信号高效可靠的连接,才能在电力电子装备中得到完美展现,而传统的硅基器件封装技术在应用于SiC器件时面临着如寄生电感过高和高温下性能退化等问题。本文总结了几种低寄生电感封装技术及高温封装技术,并对SiC器件在新能源电力系统中的发展进行了分析和展望。
2低寄生电感封装技术
2.1芯片无应力封装
为降低高压SiC模块的寄生电感,同时消除芯片表面的应力,全球能源互联网研究院提出了一种寄生电感极低的封装结构ZPOC(ZeroPressureonChip)封装,ZPOC封装示意图如图1所示;随后联研院采用ZPOC封装结构,基于正向参数匹配与芯片并联,研制了6.5kV/100ASiCSBD器件;结合SiCSBD串联技术,实现6支器件串联,研制了39kV/100ASiCSBD
组件,并在24kV换流阀功率模块中得到应用。
应用ZPOC封装技术的模块使用了焊接与压接相结合的封装形式,具有双面散热、易于串联、电磁兼容等优势,可以有效降低模块在封装过程中引入的寄生电感,经实验测得封装寄生电感为3.56nH,对改善模块的开关特性具有显著优势。
2.2三维(3D)封装
3D封装(示意见图2)技术将SiC模块的上桥臂直接叠加在下桥臂,上下叠加后可以减小桥臂中点的连接线(见图3),该封装技术可将模块寄生电感降至1nH以。
2010年格勒诺布尔电气工程实验室VAGNON[9]利用3D封装技术搭建了单相400V/40A高频(HF)整流器及Buck变换器模块。实验结果表明采用3D封装技术后IGBT在关断时仅有10%的电压过冲,且在导通时几乎没有欠压。因此3D封装技术可以基本消除共源极电感,同时共模电流也得到了很好的抑制。
2015年,欧洲研发中心的REGNAT[10]提出了一种基于印刷电路板(PCB)嵌入式芯片技术的新型3D封装。利用PCOC(片上电源)技术将SiCMOSFET芯片嵌入PCB内部实现较低的电感路径和共模电容。
文献搭建了如图4所示的模块,该模块具有30mm×30mm×2mm厚的PCB,上下表面为105μm铜平面,模块边缘有16个去耦电容。为了在阻抗测量期间对开关状态下的换向单元进行建模,在前环和后环中未填充的芯片位置通孔的加和减端之间实现了短路。测量连接器位于两个自由边上,因此只需反转模块即可测量前换向环路和后换向洛普阻抗。测量结果为前环的功率环路电感为0.23nH,后环的电感为0.21nH,因此采用嵌入式芯片技术的PCOC模块可实现紧凑、高密度的功率模块,同时可大幅降低回路的寄生电感,使其适用于具有快速导通和关断时间的宽禁带半导体器件(如SiC等)。
3D封装技术消除了模块中的键合线,可以有效提高器件的功率密度,充分发挥SiC器件的高频优势。同时采用3D封装技术可以降低回路的寄生电感值,减小模块体积,从而推进电力电子器件走向高频、高效、高功率密度。
2.3DBC+PCB混合封装
传统焊接型模块封装使用覆铜陶瓷板(DirectBondedCopper,DBC),芯片只能在表面上布局,大电流回路面积使得降低模块的寄生电感变得非常困难。因此CPES、华中科技大学等将DBC工艺和PCB板相结合,在芯片上通过键合线的连接方式引到PCB板上,这样可以直接在PCB层间实现控制换流回路,通过减小模块电流回路来减小寄生电感参数。
弗吉尼亚理工大学的陈正等人采用如图5所示的DBC+PCB混合封装的横截面结构,使用多层PCB来代替原有的聚酰亚胺-铜。通过切割PCB来嵌入半导体芯片,使得PCB和器件都可以连接到相同的DBC基板上,随后使用键合线将器件的顶部电极连接到PCB上的顶部铜排。
与传统工艺相比,DBC+PCB混合封装具有许多优点。1)封装的PCB层可以采用标准的PCB制造工艺,并且可以在单个回流焊工艺中与半导体芯片一起焊接到基板上,这大大简化了混合模块的制造工艺。2)通过增加电路板的铜层和使用通孔、盲孔甚至埋孔通孔,可以在PCB上实现更复杂的布线,使得开关电流路径可以更灵活地控制,同时提供了在模块中嵌入栅极驱动器电路的可能性。3)混合封装技术通过减小电流回路面积来降低寄生电感参数。混合模块的寄生电感仅为分立式TO-247封装方式的10%~20%。同时与传统的引线键合模块相比,环路电感降低35%,模块体积减小约40%。
华中科技大学的黄志召设计了如图6所示的混合模块,该结构包括AlN陶瓷基板、FPC和SiC芯片。芯片通过FPC上的窗口焊接在底层DBC上以提升散热能力;芯片和FPC同时焊接在DBC上,芯片的上表面电极经由键合线连接在FPC上,通过过孔来连接FPC的上下层铜箔。由于换流回路经过的导体存在于FPC的不同导体层,且电流流向相反形成互感抵消回路;采用薄FPC增强互感作用,从而可极大地降低主回路的寄生电感。
该混合模块通过下管换流回路的阻抗测试结果,由该结果计算出主回路总电感为3.8nH。同时开通关断的du/dt分别为37.38V/ns和37.65V/ns,可证明使用DBC+PCB混合封装技术降低了模块驱动回路的寄生电感和共源电感。
两种混合封装形式均可以有效降低模块的寄生电感参数并提升模块的散热能力。
2.4适用于单芯片的翻转贴片封装
目前商业化的SiC功率芯片多为垂直型芯片,因此基于BGA的封装技术,阿肯色大学的SEAL团队提出了一种适用于单芯片的翻转贴片封装技术,将芯片背面电极通过金属连接件翻转到和芯片正面电极同一平面,使用焊锡固定各自电极(见图7)。
翻转贴片封装省去了键合线和功率端子,可以有效降低模块的体积,从而减小封装中的材料成本。与常用的TO-247封装相比,该封装的体积减小至原体积的7.02%,导通电阻降低24%。
2.5 柔性 PCB+ 双面烧结混合封装
双面烧结技术与传统的芯片焊接和引线键合组件相比可靠性更高。塞米控公司的 KASKO通过栅极和源焊盘布局、栅极焊盘位置和隔离、栅极电阻和芯片金属化的调整,组装了如图 8 所示的具有极低电感(1.4 nH)的新型 1200 V/400 A SiC MOSFET 模块。
混合封装模块中芯片和柔性箔的DBC间的寄生电感为0.45nH,柔性箔到带有螺旋弹簧的直流母线的连接间的寄生电感为0.85nH。
柔性PCB+双面烧结混合封装与相同功率等级的传统模块相比,总寄生电感下降91.3%。而在动态特性方面,混合封装模块开通关断过程中的du/dt和di/dt分别为53kV/μs和67kA/μs。同时与相同功率等级的62mmIGBT模块相比,混合封装模块的总开关损耗仅为IGBT模块的20%。
2.6平面互连技术
为降低器件的导通电阻和寄生电感,西门子公司开发了平面互连技术SiPLIT(SiemensPlanarInterconnectTechnology)[20]。采用平面互连技术的SiC器件如图9所示。
与引线键合方式相比,平面互连技术的芯片接触面积高达90%,并提供了更大的横截面。因此,采用平面互连技术芯片的封装电阻降低了25%;此外与引线键合跨越的环路相比,互连的共面结构仅覆盖了很小的电流环路区域,从而使互连的寄生电感降低了50%。SiPLIT技术能够克服厚铝线键合带来的性能和可靠性限制。实验结果证明该技术可以有效降低封装中的电阻、电感和热阻,并有效改善EMI性能。
3高温封装技术
3.1双面散热技术
双面封装工艺通过在模块芯片上下表面均焊接DBC板或者使用银烧结技术将芯片一面与DBC焊接、另一面连接铝片来实现更好的散热。双面封装技术不仅可以改善电路板边缘场强分布,还可以降低EMI及桥臂中点的对地寄生电容,因而在新能源电动车内部的模块中有着较强的应用需求。
株洲中车的王彦刚等研发了具有双面冷却的650V/600ASiC半桥DSC汽车电源模块,将功率芯片的两侧粘合到具有隔离能力的平面部件上,金属垫片直接粘合在芯片顶部,粘接界面通过焊接或银烧结工艺形成。与单面冷却无底板模块相比,热阻减少了30%。
田纳西大学的YANG等设计了一种具有双面散热的低寄生电感SiC功率模块(如图10所示),采用岛式基板布局,与传统封装相比,新封装的功率环路电感从6.59nH降低到2.6nH,降幅达到60%以上。
CREE的LIANG设计了如图11所示的双面散热模块,两个冷板(冷却器)直接粘合到这些基板外部,从而允许模块双面集成散热。采用相位桥接线电气拓扑结构的电源开关采用面朝上/面朝下互连配置。与传统模块相比,这一模块将这些寄生效应相关的损耗降低了75%,模块组件的双面散热将比热电阻率降低到0.33cm2·℃/W,与传统模块相比降低了38%。该模块的电流密度达到220A/cm2,达到传统模块的1.52倍。
与传统封装相比,双面散热技术的优点在于可以有效降低模块的热阻,从而提升模块的散热能力及电流密度;进而可以有效降低系统中散热组件的体积,提升系统整体的功率密度。
3.2低压烧结工艺+铜线键合技术
SiC的高温特性在带来诸多便利的同时,也对封装材料和工艺提出了新的要求。丹佛斯公司的HAUMANN提出了一种低压烧结工艺实现芯片连接,工艺上通过金属化、顶部连接的金属缓冲板(丹佛斯键合缓冲器DBB)以及铜线键合3种创新解决方案来实现。其中低压烧结过程为:在连接部件间涂上银浆,随后施加压力,在致密银层和连接件(例如DCB基板)之间产生稳固的连接;其次,采用铜线键合使电流容量增加37%。应用该技术的400V/150A模块功率循环能力提高了1.5倍,达到600000次循环,极大地提升了模块的可靠性。
目前常用锡片或锡膏作为芯片和DBC板间的连接剂,其工艺成熟简单,但焊锡的热导率较低且会随温度变化,对于高温工况的SiC器件适用性较差,焊锡层的可靠性问题易造成模块失效。BOETTGE使用烧结银连接(LTJT)和瞬态液相焊接(TLPS)技术,有效降低了焊料层的空洞率。
高温封装技术采用了铜线键合技术、LTJT及TLPS技术,有效提升了模块的电流容量,降低了焊料层的空洞率,从而有效提升模块在各类高温工况下的可靠性。
4新型封装结构和高温封装技术总结
通过分析以上几种低寄生电感的新型封装结构和高温封装技术,可以发现虽然SiC功率器件的高速开关特性实现了新型电力电子装备的高可控性和低开关损耗(即高转换效率),但是高开关速度的实现依赖于低电感布线等新技术。8种技术的技术特点及优点如表1所示。
由表1可知,芯片无应力封装、3D封装、DBC+PCB混合封装、柔性PCB+双面烧结混合封装和平面互连技术均可降低模块的封装寄生电感;其中柔性PCB+双面烧结混合封装技术降低寄生电感的幅度最大,达到91.3%;平面互联技术和反转贴片封装技术均可降低25%左右的导通电阻,双面散热技术可降低30%左右的热阻。
5 SiC 封装的挑战与展望
随着我国开始构建以新能源为主体的新型电力系统,需要电力电子装备在电力系统各个层面起到关键支撑作用,SiC 器件的应用将大大推动电网柔性半导体化进程,SiC 器件在新型电力系统中应用前景广阔。在可预见的未来,电力电子器件将向高频、高效、高功率密度方向快速发展。
在电力系统领域,随着对高电压、大电流 SiC 器件需求的不断增长,业界对于模块的封装寄生电感、导通电阻、开关损耗、热阻等参数也提出了更高的要求,因此在封装层面将需要导热系数和热膨胀系数优良的封装材料,寄生电感更低的新型封装结构,多功能集成封装模块内部抗干扰以及更好的散热方式等,这些要求对未来封装技术的发展指出了方向。传统硅基模块的封装技术在 SiC 模块中应用存在诸多问题,随着基于 SiC 等宽禁带半导体材料的模块在市场中占比的提升,未来新型的封装技术将重点聚焦于降低模块的寄生电感和提升模块的高温可靠性这两个方面。
碳化硅晶圆划片技术研究
高爱梅 黄卫国 韩 瑞
( 中国电子科技集团公司第四十五研究所)
摘 要
碳化硅 (SiC) 材料具有禁带宽度大、导热性好、载流子迁移率高等优点,是第三代半导体材料的代表之一。因其莫氏硬度大,致使划片难度增大,严重制约了碳化硅器件的规模化发展;通过分析碳化硅的材料特性和现有划片技术特点,结合工艺试验,提出了几种碳化硅晶圆的划片方法,给出工艺参数并分析各自的优缺点,获得了理想的加工工艺。
碳化硅是宽禁带半导体器件制造的核心材料,SiC 器件具有高频、大功率、耐高温、耐辐射、抗干扰、体积小、重量轻等诸多优势,是目前硅和砷化镓等半导体材料所无法比拟的,应用前景十分广阔,是核心器件发展需要的关键材料,由于其加工难度大,一直未能得到大规模推广应用。碳化硅材料的加工难度体现在:(1)硬度大,莫氏硬度分布在 9.2~9.6;(2)化学稳定性高,几乎不与任何强酸或强碱发生反应;(3) 加工设备尚不成熟。因此,围绕碳化硅晶圆划片工艺和设备展开研究,对推动我国碳化硅新型电子元器件的发展,促进第三代半导体产业发展有着积极的意义。
1 碳化硅材料特性
碳化硅是ⅠⅤ-ⅠⅤ族二元化合物半导体,具有很强的离子共价键,结合能量稳定,具有优越的力学、化学性能。材料带隙即禁带能量决定了器件很多性能,包括光谱响应、抗辐射、工作温度、击穿电压等,碳化硅禁带宽度大。如最常用的4H-SiC禁带能量是3.23 eV,因此,具有良好的紫外光谱响应特性,被用于制作紫外光电二极管。SiC临界击穿电场比常用半导体硅和砷化镓大很多,其制作的器件具有很好的耐高压特性。另外,击穿电场和热导率决定器件的最大功率传输能力,SiC热导率高达 5 W/(cm·K),比许多金属还要高,因此非常适合做高温、大功率器件和电路。碳化硅热稳定性很好,可以工作在 300~600 ℃。碳化硅硬度高,耐磨性好,常用来研磨或切割其它材料,这就意味着碳化硅衬底的划切非常棘手。
目前,用于制作电子器件的碳化硅晶圆主要有2种,N型导电晶圆厚度150~350 μm,电阻率0.010~0.028 Ω·cm 2 ,主要应用于发光二极管、电力电子行业的功率器件。高纯半绝缘晶圆厚度50~100 μm,电阻率1×10 8 Ω·cm 2 ,主要用于微波射频、氮化镓晶体管等领域。针对半导体行业应用的SiC晶圆划切,研究几种加工方法的特点及应用。
2碳化硅晶圆划片方法
2.1砂轮划片
砂轮划片机是通过空气静压电主轴驱动刀片高速旋转,实现对材料的强力磨削。所用的刀片刃口镀有金刚砂颗粒,金刚砂的莫氏硬度为10级,仅仅比硬度9.5级的SiC略高一点,反复地低速磨削不仅费时,而且费力,同时也会造成刀具频繁磨损。如:100mm(4英寸)SiC晶圆划切每片需要6~8h,且易造成崩边缺陷。因此,这种传统的低效加工方式已经逐渐被激光划片取代。
2.2激光全划
激光划片是利用高能激光束照射工件表面,使被照射区域局部熔化、气化,从而达到去除材料,实现划片的过程。激光划片是非接触式加工,无机械应力损伤,加工方式灵活,不存在刀具损耗和水污染,设备使用维护成本低。为避免激光划透晶圆时损伤支撑膜,采用耐高温烧蚀的UV膜。
目前,激光划片设备采用工业激光器,波长主要有1064nm、532nm、355nm三种,脉宽为纳秒、皮秒和飞秒级。理论上,激光波长越短、脉宽越短,加工热效应越小,有利于微细精密加工,但成本相对较高。355nm的紫外纳秒激光器因其技术成熟、成本低、加工热效应小,应用非常广泛。近几年1064nm的皮秒激光器技术发展迅速,应用到很多新领域,获得了很好的效果。图1、图2分别对2种激光器划切SiC晶圆的效果进行了对比
从图1、图2中可以看出,355 nm紫外激光加工热效应小,但未完全气化的熔渣在切割道内粘连堆积,使得切割断面不光滑,附着的熔渣在后续工艺环节容易脱落,影响器件性能。1064 nm的皮秒激光器采用较大的功率,划切效率高,材料去除充分,断面均匀一致,但加工热效应太大,芯片设计中需要预留更宽的划切道。355 nm纳秒和1064 nm皮秒激光器的参数及其2种激光器划切准100 mm、厚80 μm SiC晶圆的效果如表1所示。
2.3激光半划
激光半划适用于解理性较好的材料加工,激光划切至一定深度,然后采用裂片方式,沿切割道产生纵向延伸的应力使芯片分离。这种加工方式效率高,无需贴膜去膜工序,加工成本低。但碳化硅晶圆的解理性差,不易裂片,裂开的一面容易崩边,划过的部分仍然存在熔渣粘连现象,如图3所示。
2.4激光隐形划切
激光隐形划切是将激光聚焦在材料内部,形成改质层,然后通过裂片或扩膜的方式分离芯片。表面无粉尘污染,几乎无材料损耗,加工效率高。实现隐形划切的2个条件是材料对激光透明,足够的脉冲能量产生多光子吸收。碳化硅在室温下的带隙能量Eg约为3.2 eV,即为5.13×10 -19 J。1064 nm激光光子能量E=hc/λ=1.87×10 -19 J。可见1064 nm的激光光子能量小于碳化硅材料的吸收带隙,在光学上呈透明特性,满足隐形划切的条件。实际的透过率与材料表面特性、厚度、掺杂物的种类等因素有关,以厚度300 μm的碳化硅抛光晶圆为例,实测1064 nm激光透过率约为67%。选用脉冲宽度极短的皮秒激光,多光子吸收产生的能量不转换成热能,只在材料内部引起一定深度的改质层,改质层是材料内部裂纹区、熔融区或折射率变化区。然后通过后续的裂片工艺,晶粒将沿着改质层分离。
碳化硅材料解理性差,改质层的间隔不能太大。试验采用JHQ-611全自动划片机和350 μm厚的SiC晶圆,划切22层,划切速度500 mm/s,裂开后的断面比较光滑,崩边小,边缘整齐,如图4所示。
2.5水导激光划切
水导激光是将激光聚焦后导入微水柱中,水柱的直径根据喷嘴孔径而异,有100~30 μm多种规格。利用水柱与空气界面全反射的原理,激光被导入水柱后将沿着水柱行进方向传播。在水柱维持稳定的范围内都能进行加工,超长的有效工作距离特别适合厚材料的切割。传统激光切割时,能量的累积和传导是造成切割道两侧热损伤的主要原因,而水导激光因水柱的作用,将每个脉冲残留的热量迅速带走不会累积在工件上,因此切割道干净利落。基于这些优点,理论上水导激光切割碳化硅是不错的选择,但该技术难度大,相关的设备成熟度不高,作为易损件的喷嘴制作难度大,如果不能精确稳定地控制微细水柱,飞溅的水滴烧蚀芯片,影响成品率。因此,该工艺目前尚未应用到碳化硅晶圆生产环节中。
3结束语
本文分析了目前碳化硅晶圆划片的几种工艺方法,结合工艺试验和数据,比较各自的优劣和可行性。其中,激光隐形划片与裂片结合的加工方法,加工效率高、工艺效果满足生产需求,是碳化硅晶圆的理想加工方式。
点胶设备介绍
吴经同
(上海回天新材料有限公司,上海201616)
摘要:
本文介绍了点胶设备的功能、分类、构成、选型原则、工作原理与性能特点,并以2种典型的点胶方式介绍了点胶过程中常见问题和设备参数优化方法。
随着胶粘技术的发展及应用领域越来越广,胶粘剂的点胶方式正在向机械化、自动化和高精度化方向发展。作为胶粘剂研发和应用人员,需要对常用点胶设备的组成、功能有全面的认识和了解,能够针对胶粘剂的特性帮用户选择合适的点胶设备,解决设备在使用时出现的各种问题,优化工艺参数,使设备达到最佳的使用效果。本文将对点胶设备的组成、功能、常见问题的解决方法及工艺参数优化等作简要介绍。
1点胶设备的功能、分类、构成及选型原则
1.1点胶设备的功能
点胶设备是在胶粘剂应用中,为了减少胶粘剂的浪费,实现自动化点胶,提高施胶效率和精确度的有效控制机器。根据客户需求,采用不同的点胶方法,让胶粘剂在工业自动化下应用得更简单更科学,借助点胶设备可以实现不同应用功能下的点胶,如定量灌封、壳体密封、灌封保护、在线成型、表面涂覆和底部填充。
1.2点胶设备的分类
常见的点胶设备有手持式胶枪,半自动式气动点胶机,三轴桌面式机器平台,全自动立体点胶机器手臂等,如图1所示。
1.3点胶设备的构成
点胶设备由以下几个系统组成:(1)控制胶粘剂流速流量与出胶形状的点胶阀和点胶针头;(2)提供连续不断胶粘剂供给的供料系统;(3)控制胶粘剂出胶时间和位置的点胶控制器;(4)实现胶粘剂与产品形状和要求完美匹配的功能型点胶平台;(5)如果是双组分胶粘剂体系,点胶设备还需要加装一个双组分精确计量系统;(6)双组分胶粘剂混合系统。
1.3.1点胶阀类型和功能
点胶阀的种类很多,通常根据胶粘剂的黏度、单位时间内的出胶量、供胶压力和点胶类型选择相对应的点胶阀,常见的点胶阀及其功能见表1。
表1、点胶阀及其功能
1.3.2点胶针头的类型和功能
1.3.3供料系统
供料也是设备的一个关键组成部分,一个合适的供料系统,不仅可以为点胶机提供稳定的出胶环境,也可以让胶粘剂在使用时杜绝接触环境造成污染或是空气进入点胶管道,影响点胶效果。常见的供料系统见表3。
1.3.4控制器
控制器是用来联通机器平台与点胶阀的纽带,用来控制点胶阀开关,常见的控制器有喷雾阀控制器,气动活塞阀控制器,多阀控制器,蠕动点胶阀控制器等,见图2。
1.3.5点胶平台
为了让胶粘剂按预设的方式点胶,比如打点、划线、选择性注胶、涂覆,就需要借助点胶机的点胶平台。一般点胶的路径有平面式或立体式,点胶机分为半自动式或是全自动流水线2种方式,点胶机的点胶平台类型如表4所示。
1.3.6双组分胶粘剂混合系统
双组分胶粘剂混合系统包括双组分计量泵、压力桶/压盘泵、双组分胶阀、静态混料管、稳压器(见图3)。主要应用于灌封、地成型垫片、灌封填充、发泡成型、结构粘接、密封涂布。
双组分胶粘剂计量缸式柱塞泵和齿轮式体积计量泵的精准计量。计量缸式柱塞泵,按照计量缸的横截面比例,在2个缸体活塞相同的运动距离下,定量出胶,这种计量方式出胶比例误差小,计量准确,且胶黏剂中的填料对缸体的影响小,维修成本低(见图4)。
齿轮式体积计量泵,简称齿轮泵,通过齿轮的咬合,把等体积的胶粘剂液体吸入或排出,再通过齿轮的旋转速度不同,可以控制单位时间内的出胶量,进而控制A、B组分的出胶比例(见图5)。
1.4点胶设备的选型原则
设备选型时通常考虑以下5个方面的内容,如表5、表6所示。
2 非接触式点胶方式研究和接触式点胶常见问题的解决方法
2.1 非接触式点胶方式
非接触式点胶在电子行业如1inebar灯条上的应用非常广泛,其设备见图6,以非接触式点胶过程中胶水黏度,触变与设备参数的配合为例,研究影响非接触式点胶中的散点、胶型保持和喷射高度之间的互为影响关系。
Linebar行业的用胶点是PC透镜与PCB的粘接,是通过在PCB的指定位置,通过定量快速点胶,把PCB透镜的3个连接点安装上,再进行80〜90°C大约15min的回流炉固化,把PC透镜粘接到PCB灯条上。
该应用的点胶方式是快速定量点胶,点胶点的速度决定了生产效率。采用这种非接触式的喷射点胶,单个点点胶速度可以在5ms内完成。
目前点胶时常常遇到的问题是胶粘剂与设备的匹配问题,希望在点胶过程中胶点是一个馒头型,且在未装配透镜前,胶点的馒头型保持率好,胶点形状无变化,这就需要胶水在常温下的黏度高,触变性好,这样才能使胶点在形成后形状保持良好。在实际点胶过程中,喷射阀跟柱塞阀不同,在高速喷点的时候,如果黏度太高,胶粘剂就喷不出来,容易粘在出胶嘴,形成不了完整的点;黏度太低,胶点的形状保持性又不好,而且还容易产生散点,拖尾的现象,影响灯条点胶质量。所以,设备和胶粘剂的匹配度很关键。
2.2 胶粘剂黏度与喷嘴口径的匹配
喷射阀在用于低黏度流体的点胶时,如底填胶,一般使用0.2mm的喷嘴,但当使用上万黏度且带有触变性的胶粘剂时,就无法有效划线或打点,所以高黏度胶粘剂使用时,除了喷嘴温度设置外,喷嘴的口径选择也很关键。例如在诺信S-800平台,使用DJ-8000喷射阀,出胶口加热温度40°C,气压0.17MPa,以点胶600个点为研究对象,结果见表7。
从本次实验可看出,对于不同黏度的胶粘剂,在使用喷射阀时,也要选择合适口径的喷嘴,才能得到符合要求的胶点形状和高效快速的出胶效率。
以回天6660环氧树脂胶为对象,研究胶粘剂在不同黏度和触变下点胶后胶点形状的保持和高速点胶时散点拖尾出现的概率,来找到这种工艺的胶粘剂与设备最佳匹配方案。
测试设备:诺信S-800点胶平台配合诺信DJ-8000喷射阀,胶嘴直径0.8mm,出胶口加热温度40°C,点胶高度15cm,出胶速度5ms/周期,测试胶粘剂:回天6660,测试结果见表8〜11。
结论:在使用喷射阀点胶时,胶粘剂黏度增大时,胶点的形状保持好,散点出现的概率也会减少。
结论:当初始黏度保持相同的条件下,随着触变指数的变大,胶水的散点比例也会降低,并且散点改善明显。
结论:30°C和60°C出现散点的概率较大,所以选择合适的点胶温度,对散点的改善也很关键。
结论:散点出现的概率和喷射的高度也有很大的关系,随着喷射高度的降低,散点出现的概率也大大降低。
综上可知,在喷胶过程中,散点的形成不仅与设备的参数有密切关系,而且与胶粘剂本身的黏度、触变性也有很大的关系。对于设备来说,除了参数的调整和优化外,更需要所使用的胶粘剂有合适黏度和触变指数,才能获得良好的点胶效果。如在Linebar行业应用时,首先要保证胶粘剂形状,所以需要胶粘剂有较高的黏度和触变。高黏度胶使用喷射阀极难出胶,所以在喷嘴处对胶粘剂进行加热,降低胶粘剂喷射瞬间的黏度,同时也提高胶粘剂触变指数,使胶粘剂在剪切运动时黏度较小,2部分作用,最大程度降低喷射时黏度,顺利完成出胶;同时,在到达基板表面,胶水温度降低,黏度升高,触变越明显,这种增粘效果越好,促进了胶粘剂凝聚减少散点产生。
2.3 接触式点胶常见问题的解决方法
以密封胶在平面密封时打胶为例,总结点胶过程中遇到的问题。
1)胶条出现粗细不一致,胶线不饱满
原因分析:划线时,胶水是先到达点胶面,然后随着出胶量的增加,由下而上的填充成型,一般胶条剖面是呈半圆形;出现S型,主要是点胶嘴与基板高度过高,胶水没有到达底部,点胶头已经离开该位置,所以胶条被拉成粗细不一致,胶线不饱满。
解决方法:调整点胶高度,主要是降低点胶高度,直到胶线粗细一致为止。
2) 做平面密封时,打回形或圆形胶条,在开头和收尾处出现衔接不好的问题。
因分析:开始时,出胶较少或较多,造成出胶少或者多,达不到理想的量;收尾时,断胶困难,或关胶不及时,造成出胶量大,每次点胶,重现性差,不稳定。
解决办法:出胶时间和位置的控制,与胶阀的灵敏性有关,一般将普通的时间压力式出胶的出胶头加装气动控制阀,这样出胶时间和位置与胶粘剂中压力无关,只与控制阀有关,而控制阀的开关只与输入的信号有关,与胶粘剂压力无关,这样就可以实现流体的快速开关和一致重现性好的要求。
3)高黏度胶粘剂出胶困难,点胶速度慢
原因分析:高黏度流体点胶时,往往面临的是出胶困难,打胶速度慢的困境,例如黏度超百万的高导热硅脂,用一般的时间压力方式,就很难出胶。这主要是黏度高,阻力大,阻力来自2个方面,一是包装管内流体流动的阻力;二是输送管道和点胶针头的阻力,所以克服这些阻力,只能通过提高泵胶压力和减少出胶头的阻力来完成。
解决办法:一是供胶压力采用气缸推杆式,在相同的气压下可以提高供胶压力;二是改变出胶针头的形状,使出胶针头由针型点胶头改成锥形点胶头,由于锥形针头的内径是由粗变细的形状,出胶口处是最小的内径,而针型针头,内径大小不变,且内径与出胶口一致,所以锥形针头能有效降低出胶阻力。
来源:半导体封装工程师之家
- |
- +1 赞 0
- 收藏
- 评论 0
本文由三年不鸣转载自芯长征科技公众号,原文标题为:碳化硅器件封装进展综述及展望,本站所有转载文章系出于传递更多信息之目的,且明确注明来源,不希望被转载的媒体或个人可与我们联系,我们将立即进行删除处理。
相关研发服务和供应服务
相关推荐
3300V SiC MOSFET栅氧可靠性研究
通过对3300V SiC MOSFET栅氧可靠性的试验研究,发现不同芯片设计中,栅氧在MOSFET器件承受反偏电压时所承受的应力不同。该电应力随着反偏电压的增大及温度的升高而增大。针对这种现象,在高压SiC MOSFET器件可靠性评估中应额外考虑;此外,需要在设计及应用中对该隐患加以重视。
怎么选智能汽车域控制器芯片?
自动驾驶芯片是指可实现高级别自动驾驶的 SoC 芯片。CPU作为通用处理器,适用于处理数量适中的复杂运算。汽车中的控制类芯片、底盘域控制芯片、动力域控制芯片、车身域控制芯片和座舱域控制芯片的选型需要考虑到工作要求、性能要求、产业格局和行业壁垒等因素。
芯片设计中,DRAM类型的选择正在变复杂
芯片制造商开始将多种类型和风格的 DRAM 整合到同一个先进封装中,为日益分布式的内存但更加复杂的设计奠定了基础。尽管多年来预测 DRAM 将被其他类型的内存取代,但它仍然是几乎所有计算中的重要组成部分。它的足迹非但没有消失,反而在增加,选择的数量也在增加。
士模微电子亮相第十四届配电应用技术大会,助力新型电力系统发展
7月25日,为期两天的第14届配电技术应用大会在江苏南京如期举行,士模微电子携ADC、放大器、基准等多款产品亮相第14届配电技术应用大会,并发表关于“配网应用中核心ADC性能及可靠性评价”的演讲,展示了信号链芯片全覆盖的配网解决方案以及全面完善的质量管理体系,助力新型电力系统发展。此次展品中,高性能ADC产品CM2248、CM2249均为大陆流片并通过AQKK认证。
【IC】联芯通HPLC+HRF双模芯片VC7351通过国网计量中心芯片级互联互通检测,全力助推新型电力系统建设
联芯通提供智能电网和物联网通信整体解决方案,近日宣布其HPLC+HRF双模芯片VC7351已成功通过国网计量中心芯片级互联互通检测,并取得检测合格报告。该芯片支持国家电网双模通信标准,实现HPLC高速电力线载波通信和HRF高速微功率无线通信功能,有效解决采用单模通信技术时可能存在的通信“孤岛”问题,大幅度提升通信稳定性、可靠性和实时性。
赛思同许继电气签署同步时钟装置年度框架采购协议,赋能新能源大规模接入和新型电力系统建设
近日,赛思同许继电气股份有限公司签署同步时钟装置年度框架采购协议。聚焦“源、网、荷、储”四大领域,赛思时频重器携手许继电气超强赋能新能源大规模接入和新型电力系统建设,共振国家“双碳目标”。许继电气采购的赛思同步时钟装置TS3000系列产品,是经电力科学研究院权威检测认证,可提供纳秒级时间信号,可提供独立北斗授时同时满足所有电厂(站)授时需求的高精度时间同步装置。
混合碳化硅分立器件深入图腾柱无桥PFC应用,国产龙头厂牌分享选型及方案设计经验
现代尖端电力电子设备性能升级需要提升系统功率密度、使用更高的主开关频率,现有硅基IGBT配合硅基FRD性能已无法完全满足要求,为此,基本半导体推出的混合碳化硅分立器件将新型场截止IGBT技术和碳化硅肖特基二极管技术相结合,为硬开关拓扑打造了一个兼顾品质和性价比的完美方案。
Yole展望:化合物半导体行业前景先声夺人
Yole集团半导体衬底与材料技术与市场分析师Ali Jaffal博士总结道:“化合物半导体行业正处于向更大直径衬底过渡的关键时刻。在功率电子领域,产能的需求使SiC向8英寸过渡成为了当务之急;在光子领域,人工智能正在推动高数据率激光器的需求,这将加速向6英寸InP衬底的过渡。总之,在功率电子和光子化合物半导体强劲增长的推动下,化合物半导体衬底和外延片市场将不断发展,整个行业前景可期。
用于光伏/储能/电动汽车充电器的IGBT微沟槽分立器件
描述- 该资料宣布了一种新型650V 50A混合硅碳化硅(Si/SiC)封装产品,适用于光伏/电动汽车充电/能源存储应用。这些产品采用先进的沟槽设计技术,以满足电力转换系统中功率器件的高效需求。产品具有低Vce(sat)和快速开关特性,可完全替代市场上主流的其他同类产品。
型号- H SERIES,DGW50N65CTH2A,DGZ50N65CTS2A,DGWC50N65CTS2A,DGZC50N65CTS2A,DGW50N65CTS2A,DGWC50N65CTH2A,DGZ50N65CTH2A,DGZC50N65CTH2A,S SERIES
【产品】三相1200V/450A SiC MOSFET 智能功率模块,用于电动汽车电机驱动或电力逆变器
本文介绍了一种用于电动汽车电机驱动或电力逆变器的新型三相1200V SiC MOSFET 智能功率模块(IPM),含有栅极驱动器和三相全桥SiC MOSFET功率电路,可用于水冷功率系统,优化了功率模块的电气、机械和散热设计及其控制驱动。
国产高性能MCU厂商——先楫半导体与东方电子在新型电力系统数字化等领域展开合作,赋能中国电力行业高速发展
2022年10月25日——国产高性能MCU芯片厂商先楫半导体与东方电子集团签署战略合作协议。双方将依托各自优势,联合产业上下游,聚焦智慧能源,以自主可控为抓手,在新型电力系统数字化等领域展开合作,为高质量实现我国的“双碳”目标提供新的动力。
一文看懂汽车半导体
国内汽车半导体芯片的发展取得了显著进展。国内制造商在技术水平、自主创新、政策支持、合作交流和产业链等方面取得了积极成果。然而,仍需加大研发投入,提升技术水平和产品质量,加强与国外厂商的合作,进一步推动国内汽车半导体芯片产业的发展。
一文看懂晶圆级封装工艺
晶圆级封装是指晶圆切割前的工艺。晶圆级封装分为扇入型晶圆级芯片封装(Fan-In WLCSP)和扇出型晶圆级芯片封装(Fan-Out WLCSP),其特点是在整个封装过程中,晶圆始终保持完整。除此之外,重新分配层(RDL)封装、倒片(Flip Chip)封装及硅通孔(TSV)封装通常也被归类为晶圆级封装,尽管这些封装方法在晶圆切割前仅完成了部分工序。
万字长文聊聊“车规级”芯片
什么是 Automotive Grade(也就是我们常说的车规级)?就是始终如一的可靠性。
光刻机实现突破:芯片制造核心瓶颈的环节,28nm光刻机国产替代加速推进
光刻机作为半导体制造的关键装备,在技术演进和市场竞争中发挥着至关重要的作用。国产光刻机的崛起为我国半导体产业自主发展提供了新的机遇,同时,EDA技术的不断进步也为半导体设计和制造注入了强大的动力。随着技术的不断发展,我们有理由相信,在未来的半导体产业中,中国将继续取得更多的突破和进步。
电子商城
现货市场
服务
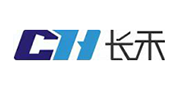
可根据用户的MOSFET管进行参数检测出具报告,静态参数最大电压:7500V、检测最大电流6000A;动态参数最大电压:3300V、检测最大电流:4500A。该测试标准满足GB、IEC及行业标准等,具备可靠性评估及老化实验能力。
实验室地址: 西安 提交需求>
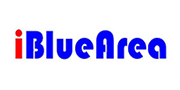
提供蓝牙BLE芯片协议、蓝牙模块、蓝牙成品测试认证服务;测试内容分Host主机层,Controller控制器层,Profile应用层测试。支持到场/视频直播测试,资深专家全程指导。
实验室地址: 深圳 提交需求>
登录 | 立即注册
提交评论