Coherent Laser FrameWork Makes a Mark in Siemen’s Digital Factory
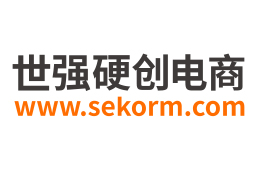
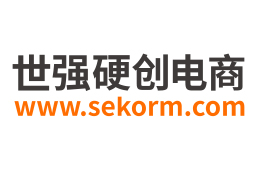
There is a growing need for manufacturers to place unique identifying marks on their products. Part of this is to meet government-specified compliance requirements. There’s also an increasing demand from both industrial users and consumers for detailed product traceability.
Governments and industry also want manufacturers to reduce their carbon footprint and to make products using more eco-friendly methods. However, these requirements for better traceability and documentation, together with greener production methods, can sometimes conflict. This is especially true when it comes to meeting compliance standards, which often generate a large amount of paper documentation.
Manufacturing leader Siemens has developed an effective way to meet both these needs with their “ID Link” initiative – an all-digital approach to product documentation. Precision Laser marking systems from COHERENT – which produce high precision marks and integrate seamlessly into the digital factory – are a key enabling technology in bringing the ID Link program into production.
THE MARKING CHALLENGE
Making the ID Link marks in a high-volume production environment presents significant technological challenges. Some of these relate to the mark itself. Specifically, the ID Link QR code contains a fair amount of data. If the product itself is physically small, then this mark must be made at very high resolution to remain readable.
Furthermore, it’s typical to write much more than just the ID Link during the marking operation. There are usually numerous other marks and symbols written at this time. Figure 1 shows a typical product from the Siemens Factory Automation group. It gets marked on two sides.
There are a couple of other wrinkles in producing the set of marks required on this particular device. One is that a portion of the face of the device is inset. That is, it’s at a lower level than the rest of the surface. So, the marking system must be able to refocus to deliver a high-resolution mark over the entire surface.
Also, several marks are placed next to LED indicators. This makes the absolute position of the mark important. So each numeral must appear next to the proper LED. Furthermore, Siemens wants good unit-to-unit consistency – the marks should always appear the same distance from the LED on every unit.
The difficulty in producing these marks is compounded because many Siemens industrial automation products are made in extremely high volume. Therefore, the takt time for a given process (like marking all these identifiers) must be short. Just a few seconds.
The other challenge in implementing ID Link in production is software related. In particular, the marking system must interface with other factory automation and Manufacturing Execution Systems (MES) to receive the information necessary to properly identify the part, and then get the specific information (serial number, etc.) for the mark itself. After marking, the laser system must transmit data about the finished part back to the production control software.
MARKING SYSTEM DEVELOPMENT
“We never considered using any non-laser marking technology for this application,” notes Tobias Mittnacht, ID Link Project Manager at Siemens. “We’re producing a high-value product in large quantities, and we want a legible mark that is cosmetically attractive and matches the quality and perceived value of our part. Plus, the mark must be indelible; these parts are handled quite a bit by users, and we don’t want the mark coming off or smudging.
“Additionally, we need to be able to produce these marks quickly, and rapidly change the mark pattern as different part variations come down the production line. Finally, to fully integrate marking into our digital factory, we need to have the marking system automatically generate each unique mark based on data coming from our PLM System. Laser marking is the only technology that delivers on all these requirements,” adds Herbert Biller.
Producing the actual mark in this case requires removing a thin layer of dark thermoplastic to reveal a lighter-colored plastic beneath it. An Nd: YVO4 laser operating in the infrared is an ideal source for this task. In some cases where the particular polymer doesn’t absorb well in the IR, a UV Nd: YVO4 laser is used instead.
The hardware solution presented by Coherent for this application was a PowerLine E25 laser marking engine. This integrates an Nd: YVO4 laser with an xy galvanometer scanner and F-theta scan lens, plus all the necessary control electronics. The actual production system uses two lasers to independently mark two sides of the device simultaneously. A fast-focusing module is used in the scanner that marks the surface having two different levels. This enables the scanner to refocus and make the sharpest possible mark no matter what the surface height.
A key element for achieving the required mark placement accuracy is the integrated, through-the-lens (TTL) vision system PartVision. It examines and verifies the part before marking and tells the scanner how to adjust for variations in position caused by material handling and part transport tolerances.
PartVision is necessary because it avoids any mismatch between the view of the vision system and that of the laser scanner. This same vision system is used for post-marking inspection.
Figure 1: Marks produced on the Siemens SIMATIC ET 200SP
interface module. Much of this same information is repeated on the side
of the device.
Figure 2: The Coherent PowerLine E25 integrates an Nd: YVO4
laser, high-performance scanning, and beam delivery optics, drive
electronics, and powerful control software to yield a fast, flexible,
and accurate marking platform.
INTEGRATING WITH THE DIGITAL FACTORY
“We chose to partner with Coherent because they are the only laser company that offers the degree of vertical integration that we require. In particular, this means providing the laser hardware and application assistance for refining the process recipes. And it includes having the capabilities and willingness to develop all the layers of software required to integrate the marker smoothly into our digital factory,” reports Bernhard Mayer, Head of New Machine & New Product Introduction.
“I think Coherent was able to achieve this software integration so quickly because of Laser FrameWork. It’s much more than just a user interface and environment for rapidly defining new process recipes. It truly is a framework that enables connectivity with other elements in the digital factory.”
“The other thing that Laser FrameWork offers us is seamless integration of the vision system. Mark placement accuracy is really important to us, plus very high-speed operation in our application. In our experience, it’s very difficult to achieve these when you add a vision system from a third-party vendor to a laser marker. It takes an embedded vision system to deliver the level of on-demand accuracy we require.”
Tobias Mittnacht points out that, “One example of Laser FrameWork flexibility, plus the willingness of Coherent to support our specific needs, showed up in implementing the surrounding frame for the ID Link. This frame must adapt dynamically to the QR code size. Coherent was the first laser manufacturer who delivered this capability within their software.”
Herbert Biller adds, “A final bonus of Laser FrameWork is that it’s backward compatible. We have a large installed base of Coherent marking systems. We’re able to upgrade these to our current standards with Laser FrameWork. This saves us a tremendous capital expense.”
Digital manufacturing is becoming increasingly popular because it enables companies to respond more quickly to changing demands, increases production efficiency, reduces labor content, and improves quality. Coherent Laser FrameWork enables Coherent laser machines to operate successfully in the digital environment. And support from Coherent in developing applications based on Laser FrameWork can rapidly get these solutions into production.
Figure 3: Vision and pattern recognition capabilities
included in the Laser FrameWork software, combined with a TTL vision system, ensure
mark placement accuracy.
THE ID LINK CONCEPT
The International Electrochemical Commission has formulated a standard (IEC 61406-1) for product identification that is quickly gaining global use. It specifies that each product unit must have a unique mark that provides a link (URL) to digital information about that product.
The Siemens ID Link was developed to meet this standard and provides an eco-friendly approach to meeting product labeling, documentation, and compliance requirements. An ID Link is a unique QR code that forms the “digital nameplate” of the product. It contains information including the part number, serial number, and even the MAC address for products used in the IOT (internet of things). The customer can easily identify the ID Link because it is always surrounded by a standardized square frame with a triangular corner on the lower right side.
Scanning this ID Link QR code takes the user to a web page that contains comprehensive product information. This can include datasheets, manuals, calibration protocols, compliance certifications, downloads, Siemens product contacts, and even information on the product’s carbon footprint.
Providing all this information digitally eliminates a virtual mountain of associated paperwork. Plus, it makes everything immediately accessible to the user. There’s never a need to search for a misplaced manual.
Currently, Siemens is working to implement ID Link on all the products manufactured by the company’s two largest divisions – Digital Industries and Smart Infrastructure. The initiative is in pilot production at a Siemens factory in Amberg, Germany; this facility belongs to the Factory Automation business unit within the Digital Industries division. The Factory Automation plant manufactures industrial automation products.
- |
- +1 赞 0
- 收藏
- 评论 0
本文由玄子转载自COHERENT News,原文标题为:LASER FRAMEWORK MAKES A MARK IN SIEMENS’ DIGITAL FACTORY,本站所有转载文章系出于传递更多信息之目的,且明确注明来源,不希望被转载的媒体或个人可与我们联系,我们将立即进行删除处理。
相关推荐
UV Lasers from Coherent Enable Detection of Minute Defects on Semiconductor Wafers
UV lasers from Coherent enable detection of minute defects on semiconductor wafers which is key to maximizing yields and lowering cost.
Ytterbium Fiber Lasers Enable Cutting-Edge Neuroscience
The latest generation of ytterbium-based lasers now provides full independent control of both the tunable beam and the fixed wavelength beam, before they leave the laser head, i.e., with guaranteed pulse width and TEM00 beam quality (M2 < 1.1).
Coherent LASER FRAMEWORK助力西门子在其数字工厂中生成标记
借助 Coherent 应用程序开发支持和 Coherent 出品的 Laser FrameWork 软件,西门子能够成功实施其 ID Link 制造计划。
Coherent Introduces New Laser Welding Head With Tactile Seam-Tracking Technology for Electric Vehicle Manufacturing
Coherent Corp., a leader in advanced laser processing solutions, today introduced HIGHtactile, a new laser welding head with tactile seam-tracking technology ideal for electric vehicle (EV) manufacturing applications.
Coherent Unveils Discovery LX Laser, Provides Ultrashort 100fs Pulses, Expanding the Chameleon Discovery Family
Coherent announces the launch of the Chameleon Discovery LX, the latest addition to the successful Chameleon Discovery product line. Designed for researchers in nonlinear microscopy and ultrafast spectroscopy, this advanced femtosecond laser delivers exceptional performance and versatility to meet evolving market needs.
金刚石J-3RF激励OEM工业CO2激光器
描述- 该资料介绍了Coherent公司生产的Diamond J-3系列射频激发的工业CO2激光器。该系列激光器提供超过250瓦的平均功率,具有独特的脉冲特性,峰值功率超过750瓦。激光器具有多种波长选项,脉冲重复频率高达200 kHz,适用于多种材料加工应用。
型号- DIAMOND J-3-10.6,DIAMOND J-3,DIAMOND J-3-9.4,DIAMOND J-3-10.2,DIAMOND J-3 SERIES
Coherent Introduced 2x1000mW Dual-Chip Pump Laser Module for Optical Amplification in Optical Networks
Coherent, a leader in pump laser technology for erbium-doped fiber amplifiers (EDFAs) deployed in optical networks, today announced the industry’s first dual-chip pump laser module with up to 1000mW of output power per fiber in a 10-pin butterfly package.
Coherent Introduces ARM FL20D Fiber Laser, Setting New Standards for High-Power Welding
Coherent today announced the launch of the ARM FL20D fiber laser. This new offering in the highly successful ARM laser family features a new higher power level of 20 kW and a unique dual ring beam configuration.
金刚石J-6射频激励OEM工业CO2激光器
描述- 该资料介绍了Coherent公司生产的Diamond J-6型号的CO2激光器。该激光器是一款全封闭、脉冲式CO2激光器,平均功率超过500瓦,具有紧凑的集成设计。其独特的板状放电设计使得J-6激光器能够提供优化的脉冲和准连续波性能,适用于高功率准连续波操作的应用,如柔性包装、折叠纸盒、打孔、标签切割、纺织品图案设计和雕刻等。
型号- DIAMOND J-6,DIAMOND J-6-10.6
Coherent Introduces Industry-first Pump Laser Diode with Record 65W Power
Coherent Corp, a leader in high-power semiconductor lasers, announced the introduction of its next-generation pump laser diode, with 65W of output power for fiber lasers in industrial and consumer applications.
COHERENT LASER FRAMEWORK可管理所有系统功能的统一软件平台,提高医疗器械制造效率
今天在医疗器械制造中保持竞争力的关键在于生产力。从运营中获得更多 – 更高的吞吐量、更少的停机时间、更高的质量和更少的错误。激光器提供了所有这些优势 – 现在,Laser FrameWork 使它们比以往任何时候都更易于使用、更易于集成且更可靠。这就是生产力。
金刚石J-5射频激励OEM工业CO2激光器
描述- COherent Diamond J-5系列脉冲CO2激光器,提供平均功率超过400瓦,具有独特的板状放电设计,可实现超过1千瓦的峰值功率。该系列激光器在10.6微米和9.4微米波长下可用,脉冲重复频率高达200千赫兹,具有快速上升和下降时间。J-5系列激光器适用于广泛的材料加工应用,包括转换、钻孔、切割、刻蚀、雕刻和标记。
型号- DIAMOND J-5,DIAMOND J-5-9.4,DIAMOND J-5-10.6NB,DIAMOND J-5-10.6,DIAMOND J-5 SERIES
瓦克在2023年度国际塑料加工专业展会展示免恒温固化处理型液体硅橡胶及供有机硅激光打标使用的颜料膏
瓦克化学股份有限公司在2023年度国际塑料加工专业展会Fakuma上展示加工后无需二次硫化的硅橡胶新产品。ELASTOSIL®LR 5003液体硅橡胶适用于食品及其它敏感应用领域,无需热后加工,便可满足相关法律对极限值的规定。瓦克化学集团同时展示的,还包括一种新型有机硅弹性体打标解决方案:ELASTOSIL® Laser Marking颜料膏能够确保激光精准地对此类有机硅进行永久性标记。
Coherent New High-power CO₂ Laser Modulator Unlocks Faster Processing Speeds
Specifically, the new Coherent CO₂ laser electro-optic switch enables the use of higher power lasers (up to 1 kW) to speed up many drilling, cutting, and engraving processes involving non-metals such as polymers, composites, organics, and ceramics.
电子商城
现货市场
服务
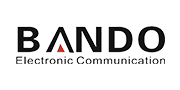
可定制高压耐热绝缘电缆的材质:导体-镀锡/镀镍软铜线,绝缘体-架桥难燃PE/氟素树脂PFA,工作电压:300-600V,工作温度:150-200℃,阻燃对应UL:VW-1、FT1、-F-mark规格。
最小起订量: 3000m 提交需求>
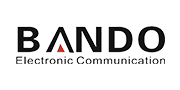
可定制高密度编组屏蔽电缆的材质、工作电压30-300V、工作温度80-90℃、芯对数和截面积、尺寸长度,阻燃对应UL:VW-1规格,电气用品安全法F-mark阻燃规格,对应UL·CSA·NEC·PSE等各种海外规格,符合欧盟RoHS。
最小起订量: 3000m 提交需求>
登录 | 立即注册
提交评论