Photon Automation and Coherent Teamwork Improves Precision Laser Welding
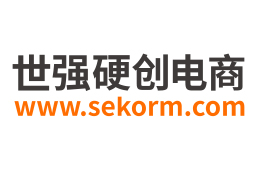
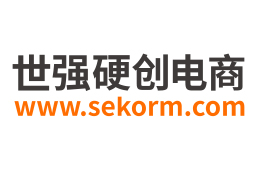
Tight coordination between the Photon Automation and COHERENT applications teams enabled rapid development of an advanced laser welding process.
Photon Automation, Inc. (Greenfield, Indiana, USA) has been designing and developing automated systems for manufacturing since 2000. The company’s ability to consistently deliver solutions that increase productivity and reduce costs has enabled them to build a highly successful business. Today they service customers in diverse areas including energy storage, medical devices, consumer products, communications, automotive manufacturing, and aerospace.
Photon Automation currently occupies 250,000 ft² of space, including applications development laboratories, engineering offices, a machine shop, and manufacturing space. In addition to designing and building custom automation systems, they also provide applications development services, prototype manufacturing and testing, and design for manufacturability (DFM) consulting. Photon Automation products range from semi-automated, stand-alone tools or fixtures to fully automated production lines.
In 2023 Photon Automation was asked to bid on a welding system for joining busbars to battery terminals for an energy storage application. Their requestor had already worked with another prototyping house on a laser welding system, but they weren’t entirely happy with the results.
In particular, the welding process the end user had was producing a significant amount of spatter. They knew that this spatter typically correlated with weld porosity and poor weld strength. Based on prior positive experiences with Photon Automation, they believed the company would be able to identify the source of the problem and provide the welding technology necessary to eliminate it. And they were confident that Photon Automation could accomplish this all in a timely fashion.
Identifying a Successful Process
Photon Automation began by reaching out to Coherent Labs in Plymouth, Michigan. They asked us to do some testing on the customer-supplied samples using our adjustable ring mode fiber laser (ARM FL). Their prior experience with this laser had shown them that its unique combination of back-reflection immunity, excellent beam quality, and advanced capability for closed-loop power control would enable it to successfully perform this type of difficult weld.
This testing confirmed the capability of the ARM FL, in particular, that it provided spatial and temporal control over how laser power is delivered to eliminate the spatter issue. It also showed that this specific process would require 8 kW of power because of the part thicknesses involved. “We weren’t surprised at the results from the ARM FL,” notes William Huffman, CEO, of Photon Automation. “It has proven itself to us in the past as very capable of tackling these kinds of very demanding welding processes.”
Coherent also performed pull tests of the welds to measure their mechanical strength. These confirmed that the ARM fiber laser process delivered the required joint quality. Plus, Photon Automation used its own CT scanner to obtain detailed views of the weld cross sections. This is necessary because a weld that looks cosmetically good from the surface may be still hiding defects underneath. Polished and etched cross-sections may or may not show porosity or cracks that could exist in front of or behind the sample, whereas CT scans show the entire weld in three dimensions.
The CT scans of the ARM laser welds confirmed what Photon Automation had hoped. Namely that weld porosity had been reduced, and that this correlated with a lower concentration of stress risers in the weld. Stress risers are features that cause a concentration of stress in a localized area of a weld joint. These stress concentrations can significantly increase the likelihood of failure, such as cracking or fatigue, under load or vibration.
Photon Automation presented the weld comparisons, including the CT scans, to their customer. While there were multiple factors involved in the customer’s decision-making, Photon Automation credits the demonstrated weld quality as the key determining factor in why they won the contract to produce the welding systems.
Coming up to Speed
While the initial application testing proved that the ARM fiber laser could deliver the required process, Photon Automation understood that there was still quite a bit of work involved in developing a production ready tool around it.
One of the central issues was creating a control system that could take full advantage of the inherent speed capability and other key features of the laser. In particular, the ability of the ARM fiber laser to very rapidly and independently change power in the center and ring beams offers distinct advantages over other lasers that lack this ability. Fully utilizing this capability promised to improve process quality and also deliver a throughput rate that would meet their customer’s needs.
But this challenge played straight into the core competency at Photon Automation. Specifically, this is the ability to combine laser sources, beam delivery systems, motion control, and part handling robotics with the level of precision and control needed to perform the most difficult welding tasks. These are welds that involve factors like high-value materials, high-performance joint requirements, or widely dissimilar materials. All of these conditions reduce the process window, necessitating this higher degree of control.
The out-of-the-box control system Photon Automation was presented with at the time had a latency in the 8 ms to 12 ms range. This delay between when the controller initiates a power change and when the laser responds to that change caused significant issues when attempting to weld conductors onto lithium-ion battery cells. This was because the scanner was capable of moving the beam on the work surface much faster than the power could be changed in the laser.
Faced with the latency limitations of the existing control hardware, the Photon software team needed to include dwell time within their code to compensate for these indeterminate delays. Photon Automation engineer Michael Dupont knew that a more elegant solution for this impediment would be to use a dedicated signal processor instead of ‘cheating’ the code with artificial delays to compensate for the laggy hardware.
Michael demonstrated his invention to the Photon management team with a wire-wrapped microprocessor-based control board that he put together. This was the start of Photon Automation’s WonderBoard™, a high-speed, dedicated control platform with the sole purpose of providing discrete, independent control of the laser center and ring power in conjunction with the spatial position of the laser on the workpiece via custom laser path planning software.
Working in close consultation with Coherent gave Photon Automation access to our in-depth knowledge of the exact workings of the ARM fiber laser. This enabled them to fully optimize the performance of their new controller. Using the WonderBoard™ with the Coherent ARM fiber laser reduced the latency in their overall system (controller, scanner, and laser) down to 2.5 µs – an improvement of nearly 5,000X! The combination of this responsive controller, beam delivery system, and part handling robotics from Photon Automation, plus the Coherent ARM fiber laser, formed the heart of the welding system they delivered.
“We knew before we started this project that the Coherent ARM fiber laser had unique capabilities and offered some big advantages for this kind of demanding welding application,” notes William Huffman, CEO, Photon Automation. “But equally important to the success of this project was the level of cooperation and coordination between our two applications teams. Our technical people are in continual contact and work together very closely. We get an immediate response when we have a question or need a test from the Coherent applications lab. And we’ll help Coherent out, too, because we have different equipment and can perform tests they don’t have direct access to, including the use of Photon’s CT scanning capability. This arrangement allows us to get the absolute best performance possible from the laser, and it gets us to that point very fast. That enables us to keep our customers happy and maintain a competitive edge.”
- |
- +1 赞 0
- 收藏
- 评论 0
本文由雪飘梦飞转载自COHERENT Official Website,原文标题为:PHOTON AUTOMATION: TEAMWORK IMPROVES PRECISION LASER WELDING,本站所有转载文章系出于传递更多信息之目的,且明确注明来源,不希望被转载的媒体或个人可与我们联系,我们将立即进行删除处理。
相关推荐
Caltech: Unlocking Quantum Mysteries
Dr. David Hsieh‘s research at Caltech utilizes the Coherent Astrella laser to study quantum materials, particularly strongly correlated electron systems like Mott insulators. His work has led to the discovery of Hubbard excitons, contributing significantly to quantum mechanics and the understanding of exotic quantum phenomena. The laser‘s precision and reliability have been crucial for these groundbreaking experiments.
UV Lasers from Coherent Enable Detection of Minute Defects on Semiconductor Wafers
UV lasers from Coherent enable detection of minute defects on semiconductor wafers which is key to maximizing yields and lowering cost.
Coherent LASER FRAMEWORK助力西门子在其数字工厂中生成标记
借助 Coherent 应用程序开发支持和 Coherent 出品的 Laser FrameWork 软件,西门子能够成功实施其 ID Link 制造计划。
电力线F 10/30 QS激光打标机,带绿色光纤激光器
描述- 该资料介绍了两款绿色光纤激光标记机——PowerLine F 10 QS 和 PowerLine F 30 QS。这两款设备适用于半导体IC和其他热敏感元件的浅刻标记,采用绿色波长和纳秒脉冲长度的光纤激光器与高质量扫描光学系统相结合。PowerLine F 30 QS 可作为双头激光标记机使用,以提高效率。软件支持复杂图案设计和变量数据(条形码、序列号)的使用。
型号- F 10 QS,F 30 QS D,F 30 QS
Coherent Announced Latest Generation Adjustable Ring Mode Fiber Laser ARM FL, Reducing the Volume and Footprint by 50%
Coherent announced the launch of its latest generation adjustable ring mode fiber laser ARM FL. This next generation platform, featuring a new advanced controller, offers all the functions of its predecessor while reducing the volume and footprint by 50%.
Coherent Introduces New Laser Welding Head With Tactile Seam-Tracking Technology for Electric Vehicle Manufacturing
Coherent Corp., a leader in advanced laser processing solutions, today introduced HIGHtactile, a new laser welding head with tactile seam-tracking technology ideal for electric vehicle (EV) manufacturing applications.
即插即用的OBIS LX/LS激光器CW固态激光器
描述- Coherent OBIS系列激光器提供高信噪比激光技术,适用于生命科学、环境监测和检测等多个领域。该系列产品基于光泵半导体激光(OPSL)技术和激光二极管解决方案,具有出色的可靠性和性能。OBIS家族覆盖从紫外到近红外波段的波长范围,具备即插即用灵活性,可快速集成并降低时间成本。
型号- OBIS FAMILY,OBIS 473LX,OBIS 413LX,OBIS 514LX,OBIS 685LX,OBIS 640LX,OBIS 660LX,OBIS 637LX,OBIS 375LX,OBIS LX,OBIS 505LS,OBIS 522LX,OBIS 980LX,OBIS,OBIS 808LX,OBIS 405LX,OBIS 561LS,OBIS LS,OBIS 730LX,OBIS 750LX,OBIS 488LS,OBIS 422LX,OBIS 505LX,OBIS 488LX,OBIS 445LX,OBIS 633LX,OBIS 690LX,OBIS 647LX,OBIS 785LX,OBIS 458LX,OBIS 514LS,OBIS 552LS,OBIS 594LS,OBIS 532LS
Coherent Unveils Discovery LX Laser, Provides Ultrashort 100fs Pulses, Expanding the Chameleon Discovery Family
Coherent announces the launch of the Chameleon Discovery LX, the latest addition to the successful Chameleon Discovery product line. Designed for researchers in nonlinear microscopy and ultrafast spectroscopy, this advanced femtosecond laser delivers exceptional performance and versatility to meet evolving market needs.
带光束管理的FL-ARM高功率可调环形模式(ARM)光纤激光器
描述- 该资料介绍了HighLight FL-ARM系列工业多千瓦光纤激光器,具备独特的ARM技术,提供两种独立可控的同轴光束。这些激光器适用于多种焊接任务,如锌涂层钢的无间隙焊接和铝焊接(无需填充材料),具有低飞溅和无热裂纹的特点。产品特点包括可调功率范围、高稳定性、先进的闭环功率控制和优化的编程工具。
型号- FL7500-ARM,FL4000-ARM,FL-ARM,FL8000-ARM,FL-ARM SERIES,FL2000-ARM,FL6000-ARM,FL10000-ARM
Coherent Introduced 2x1000mW Dual-Chip Pump Laser Module for Optical Amplification in Optical Networks
Coherent, a leader in pump laser technology for erbium-doped fiber amplifiers (EDFAs) deployed in optical networks, today announced the industry’s first dual-chip pump laser module with up to 1000mW of output power per fiber in a 10-pin butterfly package.
Coherent Introduces ARM FL20D Fiber Laser, Setting New Standards for High-Power Welding
Coherent today announced the launch of the ARM FL20D fiber laser. This new offering in the highly successful ARM laser family features a new higher power level of 20 kW and a unique dual ring beam configuration.
Coherent Introduces New HIGHmotion 2D Laser Processing Head Optimized for Deep Copper Welds Over Wide Working Areas in EV Applications
Coherent, a leader in advanced laser processing solutions, today introduced its new HIGHmotion 2D laser processing head that is rated for 8 kW beam delivery and which has been optimized for deep copper welds over wide working areas in electric vehicle (EV) manufacturing applications.
Coherent Introduces Industry-first Pump Laser Diode with Record 65W Power
Coherent Corp, a leader in high-power semiconductor lasers, announced the introduction of its next-generation pump laser diode, with 65W of output power for fiber lasers in industrial and consumer applications.
眼镜制造商在激光焊接成功案例中看到了更好的结果
描述- 奥地利高端眼镜制造商Silhouette International通过激光焊接技术解决了生产无螺丝、无铰链钛合金眼镜框架的制造难题。采用Coherent的SmartWeld技术,实现了更精确的热分布控制,提高了焊接质量和效率。Coherent MPS Rotary自动化系统进一步降低了工具和制造成本,提高了生产效率。
电子商城
现货市场
服务
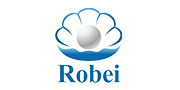
世强深圳实验室提供Robei EDA软件免费使用服务,与VCS、NC-Verilog、Modelsim等EDA工具无缝衔接,将IC设计高度抽象化,并精简到三个基本元素:模块、引脚、连接线,自动生成代码。点击预约,支持到场/视频直播使用,资深专家全程指导。
实验室地址: 深圳 提交需求>
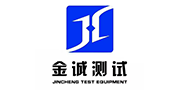
可定制无线位移传感器量程范围10~600mm,采用了无线传输方式,可远程自动实时检(监)测位移量值,准确度级别(级):0.2、0.5;内置模块:无线传输模块、供电模块;传输距离L(m):可视距离1000 (Zigbee、 LORA)。
最小起订量: 1pcs 提交需求>
登录 | 立即注册
提交评论