eVTOL Battery vs EV Battery: What’s the Difference?
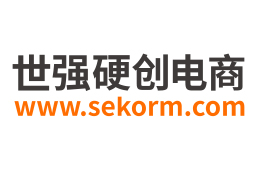
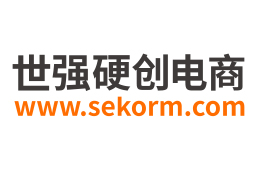
The surge in demand for urban transport alternatives has paved the way for this timely deal. As cities grapple with increasing congestion and pollution, the appeal of manned and unmanned eVTOL aircraft, operating below an altitude of 1,000 meters, is growing rapidly. These innovative vehicles promise to revolutionize urban mobility by offering efficient and eco-friendly transportation solutions. They achieve this by bypassing traditional traffic bottlenecks and reducing travel times significantly.
eVTOL is suitable for various applications, but the most popular one is urban transportation. Aerial taxis will offer faster, greener and more efficient transfers from city locations, such as financial quarters, to airports. eVTOLs could replace the helicopter services currently used for this purpose. eVTOL will offer an environmentally friendly and more economical way of providing short-hop flights. The lower costs and 24/7 operation could make it accessible to more people. The eVTOL Battery market is expected to reach US$50 billion by 2030, showcasing the immense potential for electric vertical take-off and landing (eVTOL) aircraft.
One of the key challenges is justifying the business case for mass-market appeal of these modes of transportation. This is because there is an intricate trade-off between commercial demands and technical aspects, such as safety, range, turnaround times, and battery life.
eVTOL Battery Requirements
At the core of eVTOL technology is electric propulsion, which relies on electric motors powered by batteries or other electric power sources. This contrasts with traditional aircraft that use internal combustion engines. Electric motors offer several advantages, including lower noise levels, reduced emissions, and greater efficiency. The electric powertrain of an eVTOL typically consists of a battery pack, electric motors, and power electronics that manage energy distribution. Battery reserve and performance will be central to eVTOL services, and will also provide manufacturers with a way to differentiate their models in a competitive market.
Battery technology is critical to the performance and viability of eVTOL aircraft. Advances in energy density, charging speed, and battery lifespan will enhance the range, payload capacity, and operational efficiency of eVTOLs. Research and development in solid-state batteries, fast-charging systems, and energy management will play a crucial role in the future of eVTOL technology.
For instance, with eVTOL systems, the stages of flight need to be considered, as the battery cannot be so heavy as to hinder takeoff yet needs enough power to support vertical takeoff and landing as well as (horizontal) cruising. In addition, an eVTOL battery needs to have a long cycle life and rapid charging capabilities so that it can be quickly recharged in the time between the aircraft landing and taking off again. Creating a safe battery that meets these demands requires evaluating the power–energy tradeoff, designing an optimal battery management system, and reducing the risk of battery degradation.
eVTOL Battery vs EV Battery: What's the Difference?
Electric vertical takeoff and landing (eVTOL) aircraft have attracted considerable interest as a disruptive technology to transform future transportation systems. Their unique operating profiles and requirements present grand challenges to batteries. Batteries used in transport technology need to be safe and durable and have high performance and quick charging time. Although electric batteries that meet these needs already exist on the market due to the rise in electric vehicles (EVs), there are notable differences in the performance needs for EV and eVTOL batteries.
In fact, eVTOL batteries have more stringent requirements than EV batteries in all aspects. The high cruise power leads to a larger average discharge rate for eVTOL batteries. Thus, the specific energy of eVTOL batteries should be rated at a higher C-rate than EV batteries. In addition, eVTOLs require high power for takeoff and landing, which typically lasts 30–120 s. Hence, the peak power of eVTOL batteries should be evaluated for a longer timescale than EV batteries (typically 10 s). Furthermore, charging a sufficient amount of energy in 5–10 min is essential for maximizing eVTOL revenues. The high fast-charging frequency and utilization rates make eVTOL batteries operate up to ∼1,600 h and ∼1,600 EFCs per year, posing critical challenges to battery life. Finally, eVTOL batteries have more stringent requirements on battery safety. Not only should they prohibit any fire or explosion, but they should also continue functioning even after a safety incident occurs until a safe landing. The below figure shows the typical differences between an EV battery and an EVTOL battery requirements.
Fig.1
Recharging speed and the distance the aircraft can travel before recharging will be key differentiators. These requirements highlight the role of the BMS function in boosting battery performance and extending its longevity.
The BMS for eVTOL Batteries is more Crucial than for EV Batteries
eVTOL aircraft are powered by large Li-ion batteries. Therefore, an effective battery management system (BMS) is essential. Data relating to current, voltage, temperature and other parameters must be continuously available to ensure optimal performance and safety of the passengers. The BMS continuously monitors critical performance parameters such as voltage, current, temperature, and state of charge (SOC) to keep a battery within safe operational limits, protecting it from conditions like overcharging, over discharging, and overheating. It also balances the cells within a battery pack to ensure uniform performance and extend the overall battery life. This information is communicated to users and operators in real time, keeping them well informed about the status and health of the battery systems.
Monitoring a battery’s temperature is also critical for optimizing its performance, evaluating and preventing degradation, and ensuring safety. In a battery pack, if one cell overheats, the other cells in that pack and in connecting packs will follow suit, leading to battery failure and potential safety issues, such as fire. Looking at heat generation among cell packs can also guide decision-making regarding the setup of how the batteries will be housed in the eVTOL system. If the batteries are interconnected, there is an increased risk of all batteries malfunctioning while the system is in the air.
As batteries operate, various degradation processes occur, such as mechanical degradation, the loss of active material, and electrolyte depletion. These processes lead to several unwanted effects that cause capacity loss in batteries. They diminish the battery’s performance, reducing its ability to deliver power (power fade) and store energy (capacity fade) over time. Early detection of battery degradation helps mitigate risks like in-flight failures or power loss and assists operators in planning battery usage and maintenance. Tracking degradation metrics such as impedance, capacity retention, and voltage profiles during cycles via the BMS provides insight into the extent of degradation over time and ensures the safe, reliable, and efficient use of batteries in various systems.
In an electric road vehicle, managing risks is more straightforward. The EV can automatically stop and alert the occupants if there is a risk of thermal runaway within the battery. For eVTOLs, it is not as simple. When a fault occurs, the aircraft could be thousands of meters up in the air. Likewise, if a cell malfunctions and goes offline, the effect might be severe. In a ground vehicle, it will mean a loss of traction. But for an eVTOL, a power failure could result in a sudden drop in altitude. If a battery fault that should have been detected leads to an accident, the aircraft manufacturer or operator could damage their reputation beyond repair.That’s why BMS monitoring of the cells needs increased scrutiny to identify and mitigate potential problems as quickly as possible.
Conclusion
In conclusion, while both eVTOL and EV batteries share similarities in their reliance on lithium-ion technology and the need for safety, durability, and performance, the operational demands of eVTOLs push the boundaries of battery technology further. eVTOL batteries must meet more stringent requirements, including higher discharge rates, rapid charging capabilities, and exceptional safety standards to ensure reliable performance in flight. As a global leading lipo battery manufacturer, Grepow provides semi-solid state batteies with an energy density of up to 350Wh/kg, supporting 5C fast charging, designed to fulfill the high-performance and long-endurance needs of eVTOLs.
- |
- +1 赞 0
- 收藏
- 评论 0
本文由三年不鸣转载自Grepow Official Website,原文标题为:eVTOL Battery vs EV Battery: What’s the Difference?,本站所有转载文章系出于传递更多信息之目的,且明确注明来源,不希望被转载的媒体或个人可与我们联系,我们将立即进行删除处理。
相关研发服务和供应服务
相关推荐
AAM vs UAM: What’s the Difference?
In recent years, the landscape of transportation has been undergoing a transformative shift, particularly in the realm of air mobility. Concepts like Advanced Air Mobility (AAM) and Urban Air Mobility (UAM) are becoming increasingly common parlance, but what exactly do these terms mean, and how do they differ?
What Is An eVTOL And How To Choose Batteries For It?
eVTOL aircraft are at the forefront of modern aviation, offering a revolutionary approach to urban air mobility and transportation. These aircraft, powered by electric motors, promise quieter operations, reduced emissions, and the ability to take off and land vertically, eliminating the need for traditional runways. Central to the operation of eVTOLs are their batteries, which play a critical role in determining their performance, range, and overall feasibility. Here, we explore the key aspects of eVTOL batteries and how to choose the right ones for these innovative aircraft.
Next-Generation eVTOL Battery Technology
The United Nations projects that 68% of the world‘s population will live in urban areas by 2050, up from 55% in 2018. Urban air mobility (UAM)—an ecosystem unlocking the airspace for on-demand passenger and cargo transportation by flying vehicles—has the potential to disrupt urban mobility systems. Electric vertical takeoff and landing (eVTOL) aircraft, combining helicopters’ convenience of local takeoff and landing, airplanes’ efficient aerodynamic flight, and electric powertrains‘ low noise and environmental impact, have emerged as the most promising candidate for UAM.
The BOYD Specialty Vehicle Battery Liquid Cold Plate Increases Thermal Performance While Decreasing the Weight of the Battery Pack by over 40%
When creating a new series of batteries for electric vehicles (EVs), a leading battery producer approached Boyd to design new liquid cold plates for the battery packs. The new battery packs would be featured in large electric specialty vehicles (such as fire and refuse vehicles) which require extensive amounts of power, leading to strict thermal and weight management requirements.
EV Battery Pack Water Detection Sensor from Amphenol Sensors
With the sharp growth of electric vehicles, many OEMs are using a water cooling system for the EV battery system. When water escapes the system and leaks into the battery pack, dangerous conditions are created. Amphenol Advanced Sensors‘ Water Detection Sensor monitors for water leakage by constantly checking resistance values. If a leak is detected in the EV battery pack, this sensor technology provides immediate notification.
Grepow Battery was interviewed by Global Sky Media about eVTOL Power
Grepow‘s products are mainly high-rate batteries. We will continue to develop high rate and high energy density power batteries with an energy density between 300 to 350Wh/kg while meeting a 5C to 10C fast charging and long cycle life of more than 1000 times.
How EV Cooling Batteries Products and Solutions Protect Against Collision and Thermal Runaway
This artical introduces how Aavid help protect electric vehicle batteries against collision impact and li-ion thermal runaway.
Grepow‘s NMC 532 Fast Charge Battery Increases Charging Speed By 60%
Grepow‘s NMC 532 Fast Charge Battery increases charging speed by 60%, which is very beneficial for applications such as agricultural spraying drones and mapping UAV (eVTOL) that have limited working hours.
Melexis Launches the MLX91230 Current Sensors Which Brings 0.5% Accuracy in a Compact Design
Melexis launched the MLX91230, the first product of its third generation of current sensors. This digital solution brings 0.5% accuracy at an affordable price in a compact design. The MLX91230 is perfect for EV battery management and power distribution systems.
Low Altitude Economy Benchmarking Enterprise | Grepow Gained Two Major Awards
On January 7th, the ‘2024 National UAV and Unmanned Systems Industry Spring Festival Gathering and the Ninth UAV Hundred People Summit‘ concluded successfully at Shenzhen‘s Window of the World Caesar‘s Palace. Nearly a thousand industry experts and UAV entrepreneurs from across the country gathered to discuss new strategies for low-altitude eco+nomic growth and explore emerging trends in UAV development.
格瑞普电池选型表
格瑞普锂电池,磷酸铁锂电池,高压锂电池,镍氢电池,低温锂电池,快充电池,三元锂电池选型表。倍率(C):1~50C,容量(mAh):48~40000mAh,电压:1.2V~4.35V
产品型号
|
品类
|
倍率Rate(C)
|
Thickness(mm)
|
Width(mm)
|
Length(mm)
|
容量(mAh、mA)
|
Voltage(V)
|
CP6431122-R1A
|
三元锂电池
|
1C
|
6.4mm
|
31mm
|
122mm
|
3000mAh
|
3.7V
|
选型表 - 格瑞普 立即选型
【技术】格瑞普解析刀片电池的特点和优势
关于刀片电池相信各位一定有所耳闻,那么什么是刀片电池?它有什么特点和优势呢?本文格瑞普将为您进行介绍。
2024无人机竞速联赛柯桥站,格瑞普R-LINE 5.0系列TATTU电池大放异彩,成为众多飞手信赖的选择
格瑞普研发生产的多款TATTU电池大放异彩,尤其是R-LINE 5.0系列的1550mAh、1480mAh及1400mAh型号,成为众多飞手信赖的选择。资格赛中,Minjae、王淼等一众顶尖飞手凭借卓越技术和装备优势,纷纷展现出非凡实力。
电子商城
服务
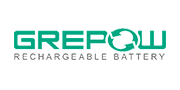
可自由定制电池形状,锂离子聚合物/磷酸铁锂成分,放电倍率Max. 50C (持续放电倍率) / 150C (脉冲放电倍率),充电倍率:Max. 5,厚度可达0.5mm。
最小起订量: 5000 提交需求>
登录 | 立即注册
提交评论