Smiths Interconnect is Transforming New Product Development with “CAD-to-FAB“

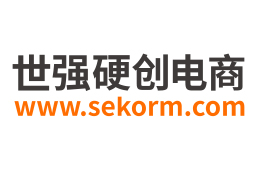

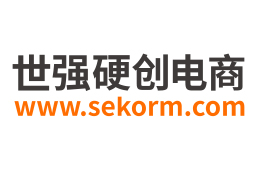
When Henry Ford reimagined the manufacturing process with interchangeable parts and a ‘continuous flow’ through specialist operators, he cut motor car production from 12 hours to 93 minutes. Replicated by manufacturers globally, this new production paradigm not only made cars affordable for the masses but also drove huge social and industrial change.
A century on, by channelling Ford’s pioneering approach to processes as well as products, engineers are continuing to find solutions for today’s pressing challenges.
One of these is ‘CAD-to-FAB’ - CAD stands for ‘computer-aided design’ and FAB for ‘digitised fabrication.’ This process can streamline and clean up the entire production line, from concept to customer-ready unit.
Old ways
The production of satellite communications components provides a useful modern illustration of the step-change CAD-to-FAB represents. Like the motor car, these items were until recently, highly customized and used sparingly for only the largest and most expensive projects. However, with the growth of low orbit satellites and other infrastructure to deliver ‘anywhere/anytime’ communications, they’ve gained a ‘mass production’ imperative – in terms of volume, cost, and pace of delivery.
Not only is this impossible to achieve with traditional component development processes, but unjustifiable given their associated environmental impact.
Take Smiths Interconnect’s original route for prototyping one such component: an isolator, which is used in satellite and radar systems to ‘quarantine’ signals from electrical and environmental interference.
Post-design production began with 2x2-inch, unmarked ceramic, wafer-thin bases – known as wafers - similar to what’s used in your phone chip. After a quality check in Dundee, Scotland they shipped to Dallas, Texas for perforation with the tiny holes that will later ‘ground’ the electrical signals moving through them – something that’s essential for the isolator to do its job, but a time-consuming, manual task.
Next, the wafers were shipped to our site in San Jose in Costa Rica where we applied the conductive ‘thread’ through which the signals flow (typically gold or silver for their superior conductive quality).
But, because we, like all other manufacturers, lacked technology precise enough to ‘draw’ the required pattern onto the wafer, we coated all of it - using the slow, wasteful process of blasting a gold or silver ingot with a high-voltage charge until it shed sufficient tiny particles to cover both sides – before the excess material was finally etched off with acid.
Between coating and etching, the wafers were diced into individual 13x13mm isolators, ready for final assembly in Dundee. This involved the fiddly process of manually adding a magnetic circuit to each isolator. Because any imprecision undermines performance, each item had to undergo an additional manual inspection before being performance-tested in our Space Test Lab.
With new products requiring an average of 2.1 design iterations before finalisation, in total this process could see them travel some 36,000 air miles over a lengthy 26 weeks - not something we could or wanted to scale up.
“FAB” idea
Instead, we’ve developed a revolutionary ‘CAD-to-FAB’ process which has been successfully trialed on a customer order for isolators for a radar system.
It began in much the same way with Dundee and Dallas doing what they had always done; but then the Costa Rica team devised a new, speedier, and cleaner way to apply the conductive material: using a high-end screen stencil to uniformly coat it. Although it still coats the whole surface, it takes just one hour per round instead of several days and wastes far less material.
The Dundee team then used patent-pending digital patterning to remove excess material – a far faster and cleaner technique than acid-etching. And final assembly is performed by COBOTs (collaborative robots) – which are far quicker and more precise than humans. Due to the tight controls embedded throughout this digitized process, the customer only required final testing of 0.1% of samples, saving further time.
The impressive outcome of the trial not only attracted a major new contract but also match-funding from the UK Space Agency that’s now enabling the establishment of a £3.8m single-site CAD-to-FAB facility in Dundee. This final improvement means that all steps in the new process will now be performed in Scotland – removing the need to send to other international locations and saving some 25,000 air miles, 8 months, and 46% of the cost of the average new product development cycle.
Grant Robertson, an engineer at Smiths Interconnect, explains: ‘This ground-breaking facility allows us to eliminate all mid-production shipping, waste and the use of acid. ‘Plus, by making design and production cheaper and more repeatable, it enables us to handle more - and larger orders with the same resource, and target higher risk/reward opportunities.’
With a patent pending for the proven CAD-to-FAB process, the team is already working to fully automate other stages of assembly and inspection. It’s this kind of drive that will help reduce our industry’s impact on the planet while scaling up innovation that improves lives. We’re pretty sure Henry Ford would approve.
How the CAD 2 FAB process works.
- |
- +1 赞 0
- 收藏
- 评论 0
本文由Lluvia转载自Smiths Interconnect Official Website,原文标题为:Transforming new product development with "CAD-to-FAB",本站所有转载文章系出于传递更多信息之目的,且明确注明来源,不希望被转载的媒体或个人可与我们联系,我们将立即进行删除处理。
相关推荐
The Anatomy of a Microstrip Isolator and Circulator: Understanding the Basics of Microwave Microstrip Isolator and Circulator Technologies
Smiths Interconnect has produced almost 700,000 microstrip isolators and circulators over the past 2 decades from 300 portfolio products. The innovation continues and on average 12 new designs being added to the portfolio each year. Today automation is used to produce a large proportion of the devices supplied with robot assembly working had in hand with human operators to bring unheard of device consistency and quality.
Smiths Interconnect Has Invested in A Comprehensive Range of Environmental Tests at Dundee Facility to Replicate Deep Space Environment
Smiths Interconnect, a global supplier of cutting-edge connectivity solutions, has invested in a comprehensive range of environmental tests at their Dundee facility. This offers an important capability to customers not prepared to negotiate on fundamental reliability and insist on demonstrable compliance.
X-band RF Isolator and Circulator
The X-band belongs to the microwave frequency range. There are two versions of X-band: one refers to the radio wave band with a frequency of 8-12GHz, and the other refers to the frequency range of X-band with a frequency of 7-11.2GHz. This artical introduces some X-band RF isolators and circulators.
The Main Application of RF Circulator
In this article UIY will introduce two common applications of circulators: duplexer and RF isolators.
Smiths Interconnect Offered Isolators to Support NASA’s Europa Clipper Mission to Explore Jupiter’s Moon
Smiths Interconnect is proud to support NASA and the Johns Hopkins Applied Physics Laboratory in providing key components for use in the forthcoming Europa Clipper mission to explore one of Jupiter’s moons.
Smiths Interconnect Has a Very Large Portfolio of Existing Coaxial Isolators and Circulators for Space or Defence Applications
As it is impractical to solder the piece parts externally and pass the assembly into the cavity, Smiths Interconnect uses a contactless induction soldering and inspect the resultant solder joints using a Smiths Interconnect in-house 3D x-ray machine, whose 160keV beam makes short work of up to 5mm of steel.
SWaP challenges in the defence industry: How Smiths Interconnect rises to the challenge
The defence industry has exceptionally high connectivity demands, especially when it comes to size, weight and power (SWaP). Smiths Interconnect is an industry-leading provider of cutting-edge connectivity solutions to the defence sector for applications such as guidance systems, data links, manpack radios, radar systems (ground, air and shipboard), antenna systems and drones.
商业航空航天连接解决方案
描述- Smiths Interconnect 是商业航空航天领域高可靠性连接产品和服务的主要供应商。公司提供高性能连接器解决方案、天线系统、射频组件和电缆组装,服务于飞行控制与导航系统、发动机系统、电源分配、卫星通信连接等多种航空应用。其技术品牌包括 EMC、Hypertac、IDI 等,专注于为高科技、高质量解决方案提供卓越性能,以满足高度安全和耐用性需求。此外,Smiths Interconnect 还提供广泛的认证标准和技术支持服务,以适应全球市场。
L、S和X波段高功率环行器和隔离器
型号- IA10001200P3KS,CB800012000P300S,CA31003500P3KS,IB800012000P300S,CA10001200P3KS,IA31003500P3KS
K波段无源元件空间合格的同轴和WR51隔离器、循环器和ISO适配器、波导负载和微带隔离器
描述- Smiths Interconnect提供一系列K波段无源组件,专为卫星通信有效载荷在GEO/MEO和LEO轨道上使用而设计。这些组件包括隔离器、环行器、终端、转换器和混合器等,覆盖从S波段到Ka波段的频率范围。产品经过内部测试和认证,确保在极端环境下稳定可靠。特点包括宽带、温度稳定、低插入损耗和高功率处理能力。
型号- 19TE110,I190220/A,I233236/A,I190220/B,19HD353,I177220/H,I255270/A,C173202/C,19TE111,I173220/A,19TM107,19TM106,I173220/C,I235240/A,19TE109,19CD328,19HD359,19HD358,I178202/J,I178202/H
国防连接解决方案
描述- Smiths Interconnect 提供一系列高可靠性连接解决方案,服务于军事和国防、医疗、半导体测试和工业市场。其产品包括集成微波组件、方向寻找器、卫星通信、数据链路、天线、光收发器和连接器解决方案等。公司技术品牌(如EMC、Hypertac、IDI、Lorch等)以其高性能和高品质解决方案而闻名,适用于安全关键应用和环境苛刻条件。产品线涵盖了高可靠性电气连接器、坚固嵌入式收发器、天线系统解决方案以及广泛的创新射频和微波解决方案。此外,Smiths Interconnect 还提供定制设计和全球支持服务。
Introduction to Common Frequency Band of Satellite Communication (C / Ku / KA Band)
UIY Inc. specializes in RF and microwave passive components, integrating R &D, production, sales and service. In this paper,UIY will introduce Common frequency band of satellite communication (C / Ku / KA band).
From the Clouds of Everest to the Surface of Other Planets, Smiths Kits and Components Are Widely Used
Smiths kit is reckoned to be on half of the geostationary satellites orbiting the Earth at present, allowing us to drive by sat-nav, get reasonably accurate weather forecasts, receive 400 television channels, trade financial instruments in milliseconds and shoot first when opponents on the other side of the world converge on your position in Call of Duty.
Smiths Interconnect’s Isolator is Connecting with (Potential) Life on Jupiter’s Moons
It was a galactic effort. No surprise, then, at the site’s pride in knowing JUICE’s first transmission was successfully made and received. Nor that the team saved JUICE’s July 2031 date of arrival at Jupiter, after which Smiths Interconnect’s isolator will be helping to relay data that is highly relevant to Earth’s immediate future.
New X-band passive components for Space and Defence
Smiths Interconnect has launched its broad range of microstrip isolators, circulators and coaxial components in X-band.
电子商城
品牌:数明半导体
品类:High Speed Six Channel Digital Isolator
价格:¥3.4118
现货: 1,520
现货市场
登录 | 立即注册
提交评论