The Liquid Cooling Plate Passed the Air Tightness Test, So Why does Leakage Still Occur?
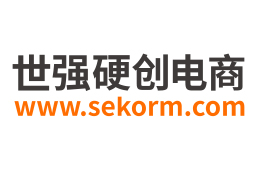
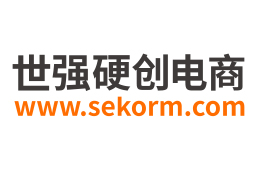
The air tightness of the battery pack is a key factor in ensuring the quality and safety of the battery pack. It is related to the safety, reliability and service life of the battery pack. The air tightness test of the battery pack should be carried out not only during the production process, but also during battery maintenance and inspection.
1. Battery Pack Airtightness Requirements
In actual production, the air tightness of the battery pack must meet the following requirements:
Sealing performance, the battery pack shell, interface and connectors must have good sealing performance to prevent dust, water vapor and other external impurities from entering the battery pack, which can be achieved through welding, sealants, waterproof materials, etc.
Waterproof performance, to prevent moisture from entering the battery, causing short circuits, corrosion and other problems. According to the national standard GB38031-2020 "Safety Requirements for Power Batteries for Electric Vehicles", the sealing performance of batteries and their components should meet the IP67 standard. Most new energy vehicles have higher sealing performance requirements for batteries and their components, and must meet the IP68 standard, that is, the battery pack can prevent water from entering within the specified water depth and submersion time.
Traditional air tightness testing methods include pressure method and immersion method (water test). The immersion method is to immerse the liquid cooling plate in water and observe whether bubbles are generated to judge the sealing.
Liquid Cooling Plate Water Channel Air Tightness Test Tank
Although the IP68 standard is more stringent, in actual applications, the pressure drop method is often used as the main detection method to meet the IP68 requirements by setting appropriate airtightness detection standards. The pressure drop method determines the airtightness of the battery pack by measuring the pressure change inside the battery pack. When performing airtightness testing, multiple parameters need to be paid attention to, such as inflation pressure, inflation time, pressure stabilization time and leakage rate.
2. Analysis of Liquid Cooling Plate Leakage Problem
With the continuous upgrading of market demand for power battery vehicles, battery energy storage systerms, etc., higher energy density and power density battery packs are widely used. Because of the thermal characteristics of batteries, to ensure the stable operation of core equipment such as batteries and improve energy utilization efficiency, liquid cooling technology is one of the mainstream technical routes for energy storage thermal management, and the air tightness test of the liquid cooling system has become a key link.
Liquid cooling plate leakage is a serious problem: the leakage will hinder the normal flow of the coolant, affect the heat dissipation effect of the liquid cooling plate, and reduce the performance of the equipment; the leakage may also cause aging and damage of system components, reducing the reliability of the system; the leakage may also corrode electronic components and circuits, increasing the risk of equipment failure and fire.
Why does the leakage problem still occur after rigorous air tightness testing during the production and manufacturing process of the liquid cooling plate?
Liquid Cooling System Airtightness Test Process
Liquid seepage may be caused by a variety of factors:
Tiny cracks and defects. Landscape air tightness testing may detect large leakage channels, but tiny cracks and defects may still exist. These tiny cracks may expand under liquid pressure or high temperature environment, causing liquid seepage.
Coolant surface tension and wettability differences: When the surface tension of the coolant is low, it is easier to penetrate through tiny gaps. If the surface tension design of the liquid cold plate is unreasonable or the coolant is not properly selected, the liquid seepage problem may be aggravated.
Wettability differences: Different coolants have different wettability on solid surfaces. If the material surface roughness of the liquid cold plate is high or there are microstructural defects, the coolant may penetrate more easily.
Installation or process problems: If the installation process of the liquid cold plate is not fine enough, or there are defects in the welding, connection and other processes, it may also lead to poor sealing and increase the possibility of liquid seepage.
Environmental conditions: Changes in temperature, especially in high-pressure environments, may affect the permeability of the coolant. Although these environmental factors may not be considered during air tightness testing, in actual operation, temperature fluctuations may cause seal failure.
Material aging or fatigue: If the material of the liquid cold plate is used for too long, it may age or fatigue, causing its sealing performance to deteriorate, thereby increasing the risk of liquid leakage.
3. Preventive Measures for Liquid Cooling Plate Leakage
Improve the design of liquid cooling plate: By optimizing the structure and design of the liquid cooling plate, reduce small cracks and defects, and improve its sealing performance. For example, when welding the module installation beam on the flow channel surface, take anti-leakage measures to avoid coolant leakage.
Improve the manufacturing process level: In the production process of the liquid cooling plate, high-quality welding processes and materials are used to ensure that the coolant is not easy to penetrate. At the same time, during the assembly process, strictly follow the operating procedures to avoid looseness or incorrect installation.
Optimize the combination of detection methods to ensure detection efficiency while improving detection accuracy and reducing missed detection rate. The immersion method and pressure drop method are used for air tightness detection, which is simple to operate, economical, and efficient, and is suitable for large-scale routine detection needs. However, the detection accuracy of the two methods is low. The detection accuracy of the pressure drop method is generally a leakage rate of 1×10-4Pa·m³/s, and the accuracy of the detection results is easily interfered by factors such as temperature, humidity, cleanliness, and pressure. Use detection equipment with higher detection accuracy and better effect to increase the detection accuracy to 1×10-6Pa·m³/s, thereby improving the detection effect.
In addition to the preventive measures for the liquid cooling plate itself, it is also necessary to adopt appropriate response strategies in multiple aspects such as coolant selection, seal selection and equipment working environment.
- |
- +1 赞 0
- 收藏
- 评论 0
本文由玄子转载自Walmate Official Website,原文标题为:The liquid cooling plate passed the air tightness test, so why does leakage still occur?,本站所有转载文章系出于传递更多信息之目的,且明确注明来源,不希望被转载的媒体或个人可与我们联系,我们将立即进行删除处理。
相关推荐
How to effectively prevent or reduce the impact of thermal deformation of battery tray welding?
Battery trays, also known as battery boxes or PACK boxes, are increasingly valued as a very important component in the development of new energy vehicles. The design of battery trays needs to balance the relationship between factors such as weight, safety, cost, and material performance. Aluminum alloys are widely used in automotive lightweight engineering because of their low density and high specific strength, which can ensure rigidity while ensuring vehicle body performance.
The BOYD Specialty Vehicle Battery Liquid Cold Plate Increases Thermal Performance While Decreasing the Weight of the Battery Pack by over 40%
When creating a new series of batteries for electric vehicles (EVs), a leading battery producer approached Boyd to design new liquid cold plates for the battery packs. The new battery packs would be featured in large electric specialty vehicles (such as fire and refuse vehicles) which require extensive amounts of power, leading to strict thermal and weight management requirements.
Risks of Channel Contamination and Cleaning Control Techniques in the Manufacturing Process of Liquid-Cooled Plates
As the power density and heat generation of various electronic and power products continue to rise, heat dissipation faces increasingly severe challenges. Liquid cooling solutions are gradually becoming the mainstream option due to their efficient heat dissipation, low energy consumption, low noise, and high reliability.
Simulation of Cooling Performance of Energy Storage Battery Packs and Optimization of Liquid Cooling
Energy storage systems, due to their important role in balancing power grid processes and improving the utilization of new energy, have become the leading force driving global energy development and transformation. Electrochemical energy storage technology is mature, with a short construction period. Power and energy can be flexibly configured according to different application needs, and the charging and discharging response speed is fast, which can be applied in various occasions.
Thermal Conductivity of Aluminum Alloy: Principles, Factors, and Applications in High-efficiency Heat Transfer Equipment
Aluminum alloy is the most widely used non-ferrous metal structural material in industry, especially in scenarios where the thermal conductivity of materials is of great concern, and in situations where efficient heat conduction is required, such as electronic equipment heat dissipation, electric vehicle three-power heat dissipation, and battery energy storage systems. In the fields of heat dissipation and aerospace, it is usually used to manufacture efficient heat transfer equipment such as radiators, heat conduction plates, and electronic components.
RRC2057 Battery Pack Instruction Manual (RRC2057 电池 使用说明书)
描述- 本说明书为RRC2057电池包的使用指南,包含操作说明和安全注意事项。强调电池的安全使用,如避免高温、火源、短路和机械冲击。详细说明了电池的存储和操作温度,以及充电和放电的条件。提供电池的技术规格,包括电压、容量、尺寸和重量。此外,还包含电池的回收和环保信息,以及符合性声明和符号解释。
型号- RRC2057
RRC2020Battery Pack Instruction Manual(使用说明书)
描述- 这份资料是一份关于RRC2020电池组的操作手册,提供了电池的使用说明、安全注意事项、技术规格和回收信息。手册涵盖了电池的安装、操作、存储和回收等方面的内容,并提供了不同语言的版本,包括德语、英语、中文等。手册强调了电池的安全使用,如避免短路、机械冲击和不当存储,并提供了电池的技术参数,如电压、容量和尺寸。此外,手册还包含了电池的回收指南和符合性声明。
型号- RRC2020
Discussion on the Development of Battery Tray for New Energy Vehicles
The three major focuses of current new energy vehicle development - safety, lightweighting, and reliability - are closely related to the battery pack, and the battery housing is the load-bearing component of the battery system, which has a significant impact on the collision, energy consumption, and other aspects of the battery pack and even the entire vehicle.
Can Walmate provide CMM report?
Walmate does not provide design services, so you will have to have a CAD file ready to use our service. You are responsible for submitting 2D and 3D CAD drawings, and we can then provide a Design for Manufacturing (DFM) review upon receiving your order.
How does Walmate ensure the quality of my parts?
Walmate takes a proactive approach to customer’s quality concerns from the initial communication, providing cost-effective and rationalized advice from designs, materials, production processes, manufacturability, etc. Once your order is confirmed, we will perform a full Design for Manufacturing (DFM) review to point out any issues that our engineers feel may affect the quality of your parts. We have the ability to share inspection data with you in real-time so we can work together to address any quality issues you may have during production. All incoming materials will meet your design specifications. Final inspection reports before shipment.
Do Walmate have any quality certifications?
Walmate is a ISO 9001 & IATF 16949 & ISO 14001 Certified Factory.
RRC2020 Battery Pack Instruction Manual (RRC2020 Battery Pack 使用说明书)
描述- 这份资料是一份名为“RRC2020 Battery Pack”的电池组的使用说明书。内容包括安全性指导、操作温度范围、存储温度建议、充电注意事项、技术规格、回收信息和合规性声明。说明书提供了多语言版本,包括德语、英语、保加利亚语、捷克语、中文(简体和繁体)、丹麦语、爱沙尼亚语、希腊语、西班牙语、法语、印地语、克罗地亚语、意大利语、日语、韩语、拉脱维亚语、立陶宛语、匈牙利语、荷兰语、挪威语、葡萄牙语、波兰语、罗马尼亚语、俄语、斯洛伐克语、斯洛文尼亚语、芬兰语、瑞典语、泰语等。此外,还包含了电池的关键成分和安全符号的解释。
型号- RRC2020
登录 | 立即注册
提交评论