Thermal Design Challenges and Heatsinks Manufacturing
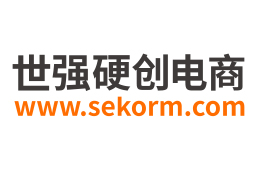
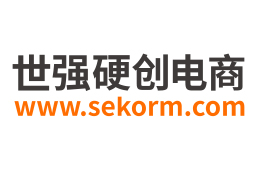
The trend towards miniaturization of electronic devices is increasing, while the demand for more functions and higher performance further drives the reduction of external dimensions at various packaging levels, resulting in a rapid increase in power density.
The miniaturization of equipment originally stems from cost reduction considerations. Cooling solutions directly increase the weight, volume, and cost of the product without any functional benefits, but they provide product reliability.
Controlling component temperature within a specified range is a common standard for determining the acceptable level of a design, and effective heat dissipation is crucial for the stable operation and long-term reliability of electronic products.
On the one hand, the result of device miniaturization is a decreasing design margin and a lower tolerance for over design. On the other hand, the overall trend of miniaturization has given rise to increasingly messy and complex geometric models, deepening the close integration of mechanical and electronic components in products. As a result, the flow space is greatly compressed, limiting the range of convective heat dissipation and making the structure of the core material of thermal design - the radiator - more complex.
Heat sink is the most commonly used heat dissipation strengthening component in electronic device thermal design. Its strengthening principle is to increase the heat exchange area. When designing, it is generally necessary to consider the heat flux density of the heat source, the temperature requirements of the heating components, the internal space size of the product, the installation and appearance design of the heat sink, and other requirements.
The performance of a heasink is influenced by many factors such as material, geometric dimensions, bottom flatness, thermal resistance, surface treatment, installation and fastening methods, and working environment temperature and humidity.
Heatsink material
The materials used for heatsinks mainly include aluminum, aluminum alloy, copper, iron, etc. Aluminum is the most abundant metal element stored in nature, with light weight, strong corrosion resistance, and high thermal conductivity, making it very suitable as a raw material for radiators. Adding some metals to aluminum to form aluminum alloys can significantly improve the hardness of the material. Graphite has the conductivity and thermal conductivity of metallic materials, as well as the plasticity similar to organic plastics, and is further applied in fields such as electronics, communication, and lighting.
2. Heatsink manufacturing process
The processing technology of radiators mainly includes CNC, aluminum extrusion, shovel teeth, slotting teeth, etc.
Aluminum extrusion: The aluminum extrusion heat sink heats the aluminum ingot to around 460 ℃, and under high pressure, allows semi-solid aluminum to flow through an extrusion mold with grooves, extruding the initial shape of the heat sink, and then cutting and further processing. The aluminum extrusion process cannot accurately ensure the flatness and other dimensional requirements of the radiator, so further processing is usually required in the later stage.
Shovel teeth: Shovel teeth are used to cut and straighten long strip shaped metal sheets (usually aluminum or copper alloys) at a certain angle using a shovel tooth machine, and repeat cutting to form a consistently arranged fin structure. Compared to extrusion technology, the advantage of shovel teeth is that they can process heat sinks with higher fin density and higher tooth height ratio.
Splitting: The processing of slotting heat sink involves inserting the teeth into the heat sink substrate, and connecting the teeth to the substrate through methods such as adhesive welding, brazing, or extrusion; The connection between the teeth and the base of the toothed radiator is very important. If not handled properly, it may form a certain contact thermal resistance, which affects the heat dissipation performance of the toothed radiator.
3. Surface treatment of heatsinks
Aluminum alloys are prone to oxidation in the air (forming an alumina film), but this natural oxide layer is not dense, has weak corrosion resistance, and is prone to contamination; Based on the requirements of aesthetics, corrosion resistance, and improved heat dissipation performance, metal radiators need to undergo surface treatment. Common surface treatment processes include anodizing, sandblasting, chemical nickel plating, and baking paint.
Anodization: The principle of anodizing is essentially water electrolysis, which involves placing aluminum or aluminum alloy as the anode in a dielectric solution and using electrolysis to form an aluminum oxide film on its surface. This process is called anodizing treatment of aluminum or aluminum alloy; After anodizing, the surface emissivity of the radiator will increase, and the heat dissipation ability of the thermal radiation will be enhanced; Anodizing can maintain or change the color of aluminum & aluminum alloys, and black anodizing is commonly used for heat sinks.
Sandblasting: Sandblasting refers to the process of using compressed air as the power and utilizing the impact of high-speed sand flow to clean and roughen the surface of a radiator; By impacting and cutting the surface, this process can not only remove all dirt such as rust on the surface of the radiator, but also exhibit a uniform and consistent metallic luster on the product surface.
Electroless nickel plating: Chemical nickel plating is a process of depositing nickel alloys from aqueous solutions onto the surface of objects; Its characteristics include high surface hardness, good wear resistance, uniform and beautiful coating, and strong corrosion resistance; Due to the inability of copper and aluminum to be directly soldered, both require chemical nickel plating before using processes such as soldering.
Baking paint: Baking paint is a high-performance special coating called Teflon added to the surface of a heat sink at high temperatures (280℃~400℃), which has the characteristics of non adhesion, heat resistance, moisture resistance, wear resistance, corrosion resistance, etc.
Compared to traditional spray painting techniques, baking paint has advantages in both aesthetics and thermal conductivity. However, heat pipe assembly heat sinks are prone to expansion and deformation due to high temperatures, so low-temperature baking paint is particularly needed during baking.
As the power to be processed continues to increase, heat sinks begin to be combined with heat pipes, fins and other devices to form higher performance heat dissipation modules, and water-cooled heat sinks with higher heat dissipation efficiency have emerged.
- |
- +1 赞 0
- 收藏
- 评论 0
本文由玄子转载自Walmate Official Website,原文标题为:Thermal design challenges and heatsinks manufacturing,本站所有转载文章系出于传递更多信息之目的,且明确注明来源,不希望被转载的媒体或个人可与我们联系,我们将立即进行删除处理。
相关推荐
Understanding the Crucial Role of Heatsinks in Electronics: More Than Just Cooling
In the world of electronics, heatsinks play a pivotal role in ensuring the efficient functioning and longevity of various devices. Often overlooked despite their critical importance, heatsinks are integral components designed to manage and dissipate heat generated by electronic components such as CPUs, GPUs, and power transistors.
How Electronic Device Manufacturers Can Deliver Cost-Efficiency For Consumers In Today’s High-Cost World
Liquid-based conformal coats protect only certain components, however, do not protect the full board inside the device. This can mean the end for devices that are susceptible to water ingress such as those with multiple moving parts or are open in design.
Littelfuse(力特)IXYS功率半导体选型指南
目录- Introduction of Littelfuse Index Symbols and Terms/Nomenclature New Pressfit Pin packages ISOPLUS™ family IGBT Discretes IGBT Modules Power MOSFETs Diodes Thyristors Rectifier Bridges Protection Devices Gate Drivers/Power Relays Diode & Thyristor(IXYS Chippenham) Power Semiconductor Chips/Direct Copper Bonded Ceramic Substrates Application Notes Highlights Outline Drawings
型号- R1280NC25M,MCD 26-16IO1B,N2055HE420,IXTT 30N50L2,R1280NC25K,R1280NC25L,MCD 56-18IO8B,IXBOD 2-52R,R1280NC25J,IXTQ 52N30P,MCK 200-18IO1,IXYR 100N120C3,LSIC2SD120C05,MDC600-22IO1W,IXYH 16N250CV1HV,LSIC2SD120C08,M0863LC360,IXTP 100N15X4,VBO 125-08NO7,DPG 15I200PA,F1600NC080,IXTH 1N450HV,T0600TB45A,LSIC2SD065E40CCA,DSEP 2X91-03A,IXBOD 2-51R,IXTX 4N300P3HV,IXTA 36N30P,VBO 72-18NO7,M4305TJ240,IXFR 64N60P,N6405EA240,IXYR 50N120C3D1,MCD580-28IO7,VUO 25-14NO8,0440 007.WRA,IXFY 36N20X3,VBO 25-12NO2,IXTT 120N15P,M1010NC400,IXBH 6N170,MCC 56-14IO1,VBE 26-06NO7,MCD160-30IO3,SXB4869G,IXTJ 3N150,DHG 10I1200PM,IXTH 120P065T,VTO 39-08HO7,IXFN 32N80P,IXTL 2N450,DMA 30P1600HR,IXBOD 2-54R,MDK950-18N1W,CS 20-25MOT1,IXBOD 2-55R,IXTK 140N20P,IXTR 48P20P,DH 20-18A,W2115MC560,IXTP 05N100P,IXFT 18N90P,QJ8030LH4TP,N4340TJ180,DMA 30P1600HB,W3841VC340,MKH 17RP650DCGLB 11,,SXB4649HEXT,IXBOD 2-17RD,DSEP 40-03AS,IXFH 42N50P2,Q8025K6TP,IXFH 22N50P,DPG 30C200HB,DSI 30-12AS,MCMA 240UI1600ED,IXBOD 2-53R,M0367WC220,VUM 25-05E,CPC1786J,IXYT 80N90C3,T0840NC17E,CLA 100E1200HB,N3533ZD180,R0717LC16H,IXTR 140P10T,R0717LC16G,IXFT 60N50P3,VUM 33-06PH,IXFA 22N65X2,VUO 84-16NO7,MIXA 60W1200TED,MDD275-30N3,IXA 70I1200NA,IXYH 80N90C3,IXTQ 86N25T,IXFN 80N60P3,MDMA 65P1600TG,IXTL 2N470,IXTT 88N30P,XAA170,MCR500-30IO7,N6405EA280,DSA 30I100PA,IXGX 55N120A3H1,E0770HF65F,IXFR 40N90P,W7045MC030,IXTQ 44N50P,XK2000SA114M,IX4351NE 130,MDNA 660U2200PTEH,MIXG 180W1200TEH,LOC210,IXFK 120N25P,LOC211,IXGH 20N120A3,DSB 15IM30UC,IXTQ 26N50P,IXTP 450P2,IXFH 86N30T,IXFK 120N65X2,N2086NC060,IXTP 60N20T,MDD 142-12N1,IXXH 30N60B3D1,XSK4400DA116M076,CPC1788J,IXFB 40N110P,N2055HE450,IXBOD 2-56R,DHG 10I1200PA,M4305TJ280,DSA 60C60HB,IXFK 240N25X3,MCD720-18IO7,F1300NC45P,R0717LC14H,W121CEC180,W4205TE520,R0717LC14G,XW180GC34B,MMIX 1G75N250,XW180GC34A,IXBOD 1-30R,IXTY 1R4N100P,MDO 500-18N1,XSK3400DA076038,VBO 25-16AO2,VBO 50-16NO7,K1947ZC400,IXFQ 26N50P3,DSEP 2X91-06A,MEO 450-12DA,S0500YC25Y,IXYQ 30N65B3D1,W3842MC240,S6004DS2RP,G4000EF250,CLA 100E1200KB,IXTT 1N450HV,VUB 116-16NOXT,H0700KC140,VW 2X60-12IO1,MCMA 265P1600KA,DPG 10I200PA,IXFT 46N30T,IXYP 10N65C3D1,IXTH 440N055T2,N3533ZD140,DPG 10I200PM,Q8015LTP,DSA 70C200HB,DPG 30I300HA,DSA 50C100QB,IXTH 30N50L2,R3047TC28M,R3047TC28N,MCC 44-14IO8B,R3047TC28K,MCNA 180PD2200YB,MCD 255-16IO1,N2172ZD450,MCO 500-16IO1,DCG 20C1200HR,MCD 162-18IO1,VVZB-16IOXT,DSSK 40-006B,IXGH 10N170A,VUO 62-14NO7,M0710LC600,Ø IXTP 130N15X4,N4472HK180,IXBOD 1-32RD,DHH 55-36N1F,DSSK 18-0025BS,MCD 56-18IO1B,IXFK 220N20X3,Ø IXG 70IF1200NA,F0900VF520,IXBOD 2-35RD,IXTA 90N075T2,R2475ZD28R,VUB 120-16NOX,IXYP 20N120C4,R2475ZD28N,M0367WC280,IXYP 20N120C3,M1609NC260,R2475ZD28M,IXXH 40N65B4,MDD 26-14N1B,VUO 98-16NO7,MDD 310-18N1,MCD 26-16IO8B,MITA 300RF1700PTED,H0700KC14Y,MDC500-22IO1,VBO 52-08NO7,XAA117,DSEP 2X61-12B,DSEP 2X61-12A,IXFX 180N15P,S8055RTP,VUO 68-08NO7,MCNA 120PD2200TB-NI,MIXA 41W1200ED,IXTH 06N220P3HV,IXTP 10P50P,MCD500-18IO1,MMO 140-12IO7,IXYP 20N120B4,MCC500-22IO1,IXFH 50N85X,W3842MC280,DSSK 40-008B,DSSK 60-02A,IXFR 102N30P,N4472HK160,IXFH 12N120P,H0700KC17Y,MCC320-36IO2,M1494NK250,XSL300C2WS,DSEP 2X25-12C,IXFH 100N25P,IXTK 200N10L2,DSEP 12-12B,MMIX 1B20N300C,DSEP 12-12A,IXTH 50N25T,IXFN 140N30P,H0700KC17D,W3842MC28A,DSEI 60-06A,MCD 225-12IO1,LSIC2SD065D06A,M0451YC120,DSEI 2X161-12P,DHG 50X650NA,MCMA 35PD1200TB,MDC550-12IO1,DSI 2X55-12A,IXTY 8N65X2,MCC 255-16IO1,IXYP 20N120A4,IXTH 460P2,LCA220,MDD 56-18N1B,MDC580-28IO7,W9830TJ150MBR,R1280NC21J,CLA 100E1200TZ,IXTP 230N04T4,R1280NC21M,VBE 17-06NO7,R1280NC21K,R1280NC21L,M1609NC200,IXGX 120N60A3,MMO 175-16IO7,IXGK 82N120A3,DSSK 48-0025B,CS 19-08HO1S,DSEC 30-12A,MCD501-16IO2,MIXG 240W1200PTEH,LSIC2SD120E30CC,SJ6012DRP,VUO 105-18NO7,R1280NC22J,MCD 72-18IO1B,VUO 160-18NO7,IX4310T,R1280NC22K,R1280NC22L,R1280NC22M,F0900VC450,MEO 500-06DA,SXB2167FB,IXTQ 60N10T,IXFN 30N120P,VUO 30-08NO3,M0334RJ200,DSA 60C60PB,MDD 255-16N1,IXFH 18N65X2,MCC 225-12IO1,R2620ZC22L,MDA 810-18N2,R2620ZC22K,IXBH 10N170,R2620ZC22J,MDMA 140P1200TG,MDA950-18N1W,NANOASMDC016F-2,IXFN 40N110P,IXFX 250N10P,MCD320-30IO2,IXTY 10P15T,IXBOD 2-50R,DPG 30I300PA,IXFN 50N120SK,CPC3902,N2172ZD420,IXTT 16N20D2,MDD 710-26N2,W3841VC300,N4340TJ180MBR,IXTP 12N65X2,N3175HE160,SV6020R2TP,DSEI 60-02A,DPG 60C400QB,CPC3909,W2115MC520,DSEC 60-06B,DSEC 60-06A,MCMA 450UH1600TEH,DSSK 30-018A,IXYP 10N65C3,IXBH 22N300HV,IXTA 62N15P,CNE 60E2200TZ,DSI 2X55-16A,IXFR 180N15P,F1500NC200,LSIC2SD120C10,IXFP 220N06T3,MCD600-22IO1W,IXTA 36P15P,MIXG 360PF1200PSTED,F1500NC250,IXFH 80N65X2-4,MDD 175-28N1,IXBT 32N300HV,DSA 35-12A,IXTX 60N50L2,M0710LC560,R5145FA42V,IXTH 30N50P,R5145FA42W,DHG 100X650NA,IXGT 10N170A,IXFA 10N80P,MMIX 1T132N50P3,FMM 22-06PF,DMA 30P1200HB,DSA 75-16B,W5130MK280,IXTH 2R4N120P,LSIC1MO120T0080,IXTX 80N30L2,IXYN 75N65C3D1,MDD630-36N2,DSEI 2X161-06P,W5838ZD220,DSEI 60-12A,IXYH 40N65C3H1,W5282ZC240,IXTR 210P10T,MDMA 425P1600PTSF,IXXK 300N60C3,P0848YC06B,P0848YC06C,DHG 60C600HB,DPG 30P300PJ,LSIC1MO120E0040,S0700KC14Y,IXFK 220N15P,MCC 26-16IO1B,IXGK 55N120A3H1,DSA 1
How to Design A Rectangular Fin Heatsink
In applications where volumetric power density and heat flux density requirements are not high, rectangular fin heatsinks are favored by engineers due to their simple structure, reasonable manufacturing cost, and good heat dissipation performance.
Can Walmate provide CMM report?
Walmate does not provide design services, so you will have to have a CAD file ready to use our service. You are responsible for submitting 2D and 3D CAD drawings, and we can then provide a Design for Manufacturing (DFM) review upon receiving your order.
Kinghelm Board-to-board Connector KH-WB105-F30E-04L: Setting a New Benchmark for Electronic Device Connections
In modern electronic devices, the performance of connectors directly affects the reliability and data transfer efficiency of the equipment. As a high-performance board-to-board connector, the Kinghelm KH-WB105-F30E-04L stands out with its unique design and excellent electrical performance, making it an ideal connection solution in fields such as communications, automotive electronics, and industrial automation.
How does Walmate ensure the quality of my parts?
Walmate takes a proactive approach to customer’s quality concerns from the initial communication, providing cost-effective and rationalized advice from designs, materials, production processes, manufacturability, etc. Once your order is confirmed, we will perform a full Design for Manufacturing (DFM) review to point out any issues that our engineers feel may affect the quality of your parts. We have the ability to share inspection data with you in real-time so we can work together to address any quality issues you may have during production. All incoming materials will meet your design specifications. Final inspection reports before shipment.
Do Walmate have any quality certifications?
Walmate is a ISO 9001 & IATF 16949 & ISO 14001 Certified Factory.
2149730-1 SFP+1x4固定架、散热器和光导管材料声明
描述- 本资料为TE Connectivity公司关于其产品SFP+ 1x4 Cage, Heatsinks and Lightpipes的合规性声明。内容包括产品符合欧盟RoHS指令、中国RoHS指令和REACH法规的要求,详细列出了产品中各材料的成分、含量及合规性信息。
型号- 2149730-1
Can Walmate make design drawings for me?
Walmate does not provide design services, so you will have to have a CAD file ready to use our service. You are responsible for submitting 2D and 3D CAD drawings, and we can then provide a Design for Manufacturing (DFM) review upon receiving your order.
Do Walmate offer OQC reports? Like material cert and FAQ?
Walmate offers OQC reports upon request.If required, we can produce additional documentation on material certs, inspection reports, certificates of conformance, etc. We just ask that this information is requested upfront on the order as it becomes very difficult to get something like a material cert afterward!
What types of manufacturing processes can Walmate offer?
CNC Machining, Aluminum Extrusion,Skived Fin Process, and Welding, which include Friction Stir Welding(FSW), Cold Metal Transfer( CMT), Brazing.
登录 | 立即注册
提交评论