Simulation of Cooling Performance of Energy Storage Battery Packs and Optimization of Liquid Cooling
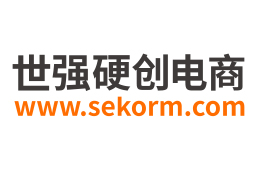
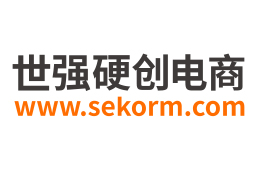
1-Introduction
Energy storage systems, due to their important role in balancing power grid processes and improving the utilization of new energy, have become the leading force driving global energy development and transformation. Electrochemical energy storage technology is mature, with a short construction period. Power and energy can be flexibly configured according to different application needs, and the charging and discharging response speed is fast, which can be applied on various occasions.
During the charging and discharging process of energy storage systems, heat is generated. Poor heat dissipation can cause the battery temperature to be too high or the battery temperature difference to be large. In mild cases, it can lead to a decrease in battery life, and in severe cases, it can cause safety issues such as thermal runaway.
This article is based on a practical project and establishes a thermal fluid simulation model according to the actual size of the battery pack. It analyzes in detail the distribution of pressure, velocity, and temperature in the entire heat dissipation system, obtains the thermal load of the system, and provides structural optimization suggestions for the design of the liquid cooling plate flow channel of the battery pack.
2-Project Overview
2.1 Environmental Information
2.2Specification information of heat source devices:
2.3 Thermal Conductive Silicone
3-Heat Dissipation Model
A battery pack that uses liquid cooling for heat dissipation, consisting of 72 280AH cells and a liquid cooling plate. The size of the liquid cooling plate is 1570mm in length, 960mm in width, and 42mm in height, with 24 internal flow channels. The heat dissipation model of the battery pack is shown in the following figure:
4-Simulation Results Under The Condition of Inlet Water of 8L/min
The temperature distribution of the battery cells is 18.38-28.77 ℃, with the temperature distribution range of the highest temperature cell being 21.46-26.37 ℃ and the temperature distribution range of the lowest temperature cell being 18.76-26.37 ℃. As shown in Figure (a):
Temperature distribution of liquid cooled plate: 18.00-21.99℃, as shown in Figure (b):
The flow resistance is about 17KPa, the pressure profile of the liquid cooling plate is shown in Figure (c), and the velocity profile of the liquid cooling plate is shown in Figure(d):
5-Conclusion
In this plan, the overall temperature ranges from 18.38 to 28.77 ℃, with a temperature difference of 2.4 ℃ between the highest and lowest battery cells. The overall temperature of the liquid cooled plate ranges from 18.00 to 21.99 ℃, the uniformity of temperature still needs to be optimized, multiple high-temperature areas have appeared.
Comparing the pressure and velocity profile of the liquid cooling plate, the high-temperature area of the liquid cooling plate is mainly distributed in areas with lower pressure and velocity. Based on the layout of the battery cells, it can be seen that the width margin of the liquid cooling plate is relatively large. It is recommended to block the two outermost flow channels of the liquid cooling plate, or appropriately reduce the width of the liquid cooling plate to achieve better heat dissipation effect.
- |
- +1 赞 0
- 收藏
- 评论 0
本文由梨花落风转载自Walmate Official Website,原文标题为:Simulation of cooling performance of energy storage battery packs and optimization of liquid cooling...,本站所有转载文章系出于传递更多信息之目的,且明确注明来源,不希望被转载的媒体或个人可与我们联系,我们将立即进行删除处理。
相关推荐
Thermal Conductivity of Aluminum Alloy: Principles, Factors, and Applications in High-efficiency Heat Transfer Equipment
Aluminum alloy is the most widely used non-ferrous metal structural material in industry, especially in scenarios where the thermal conductivity of materials is of great concern, and in situations where efficient heat conduction is required, such as electronic equipment heat dissipation, electric vehicle three-power heat dissipation, and battery energy storage systems. In the fields of heat dissipation and aerospace, it is usually used to manufacture efficient heat transfer equipment such as radiators, heat conduction plates, and electronic components.
What is a Lithium-ion Battery Cell, Battery Module, and Battery Pack?
In the fast-paced world of technology and electric vehicles, lithium-ion batteries have become the backbone of energy storage solutions. Whether it‘s powering your smartphone, laptop, or electric car, these high-energy-density batteries have revolutionized the way we store and utilize electrical energy. In this article, we will delve into the components that make up a lithium-ion battery system, exploring the intricacies of battery cells, battery modules, and battery packs.
The BOYD Specialty Vehicle Battery Liquid Cold Plate Increases Thermal Performance While Decreasing the Weight of the Battery Pack by over 40%
When creating a new series of batteries for electric vehicles (EVs), a leading battery producer approached Boyd to design new liquid cold plates for the battery packs. The new battery packs would be featured in large electric specialty vehicles (such as fire and refuse vehicles) which require extensive amounts of power, leading to strict thermal and weight management requirements.
The Liquid Cooling Plate Passed the Air Tightness Test, So Why does Leakage Still Occur?
Why does the leakage problem still occur after rigorous air tightness testing during the production and manufacturing process of the liquid cooling plate? This article analyzes the causes of liquid cooling plate leakage and brings up corresponding preventive measures.
How to effectively prevent or reduce the impact of thermal deformation of battery tray welding?
Battery trays, also known as battery boxes or PACK boxes, are increasingly valued as a very important component in the development of new energy vehicles. The design of battery trays needs to balance the relationship between factors such as weight, safety, cost, and material performance. Aluminum alloys are widely used in automotive lightweight engineering because of their low density and high specific strength, which can ensure rigidity while ensuring vehicle body performance.
Risks of Channel Contamination and Cleaning Control Techniques in the Manufacturing Process of Liquid-Cooled Plates
As the power density and heat generation of various electronic and power products continue to rise, heat dissipation faces increasingly severe challenges. Liquid cooling solutions are gradually becoming the mainstream option due to their efficient heat dissipation, low energy consumption, low noise, and high reliability.
RRC2057 Battery Pack Instruction Manual (RRC2057 电池 使用说明书)
描述- 本说明书为RRC2057电池包的使用指南,包含操作说明和安全注意事项。强调电池的安全使用,如避免高温、火源、短路和机械冲击。详细说明了电池的存储和操作温度,以及充电和放电的条件。提供电池的技术规格,包括电压、容量、尺寸和重量。此外,还包含电池的回收和环保信息,以及符合性声明和符号解释。
型号- RRC2057
RRC2020Battery Pack Instruction Manual(使用说明书)
描述- 这份资料是一份关于RRC2020电池组的操作手册,提供了电池的使用说明、安全注意事项、技术规格和回收信息。手册涵盖了电池的安装、操作、存储和回收等方面的内容,并提供了不同语言的版本,包括德语、英语、中文等。手册强调了电池的安全使用,如避免短路、机械冲击和不当存储,并提供了电池的技术参数,如电压、容量和尺寸。此外,手册还包含了电池的回收指南和符合性声明。
型号- RRC2020
Discussion on the Development of Battery Tray for New Energy Vehicles
The three major focuses of current new energy vehicle development - safety, lightweighting, and reliability - are closely related to the battery pack, and the battery housing is the load-bearing component of the battery system, which has a significant impact on the collision, energy consumption, and other aspects of the battery pack and even the entire vehicle.
Can Walmate provide CMM report?
Walmate does not provide design services, so you will have to have a CAD file ready to use our service. You are responsible for submitting 2D and 3D CAD drawings, and we can then provide a Design for Manufacturing (DFM) review upon receiving your order.
How does Walmate ensure the quality of my parts?
Walmate takes a proactive approach to customer’s quality concerns from the initial communication, providing cost-effective and rationalized advice from designs, materials, production processes, manufacturability, etc. Once your order is confirmed, we will perform a full Design for Manufacturing (DFM) review to point out any issues that our engineers feel may affect the quality of your parts. We have the ability to share inspection data with you in real-time so we can work together to address any quality issues you may have during production. All incoming materials will meet your design specifications. Final inspection reports before shipment.
Do Walmate have any quality certifications?
Walmate is a ISO 9001 & IATF 16949 & ISO 14001 Certified Factory.
登录 | 立即注册
提交评论