A Overview of Cooling Systems for Hydrogen Fuel Cell Vehicles
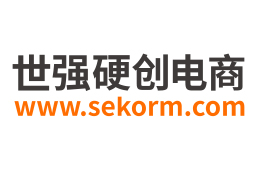
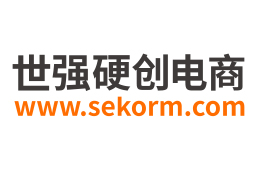
Abstract: Hydrogen fuel cells, also known as proton exchange membrane fuel cells (PEMFCs), are widely used in electric vehicle charging stations, automobiles, and other power generation facilities due to their advantages of high efficiency, zero emissions, and zero pollution. Hydrogen fuel cell vehicles emit 3-5 times more heat during operation than traditional fuel vehicles. This article briefly describes the current technology related to hydrogen fuel cell heat dissipation.
1-Working Principle of Hydrogen Fuel Cells
Hydrogen fuel cells release a large amount of heat during operation, among which electrochemical reaction heat accounts for about 55%, irreversible electrochemical reaction heat accounts for about 35%, Joule heat accounts for about 10%, condensation heat and various heat losses account for about 5%. The heat generated by hydrogen fuel cells is approximately equal to the electrical energy they generate. If not dissipated in a timely manner, the temperature inside the battery will significantly increase, thereby affecting its service life.
2-Hydrogen Fuel Cell Heat Dissipations
Compared to fuel powered vehicles, hydrogen fuel cell vehicles have a higher heat generation and a more complex system. At the same time, due to the limitation of the working temperature of hydrogen fuel cells, the temperature difference between hydrogen fuel cells and the outside world is smaller, making it more difficult for the heat dissipation system to dissipate heat. The working temperature of hydrogen fuel cells has a significant impact on fluid flow resistance, catalyst activity, stack efficiency, and stability, thus requiring an efficient heat dissipation system.
Liquid cooling technology is currently the mainstream technology in the application of hydrogen fuel cells in vehicles. It aims to reduce water pump power consumption by reducing system pressure drop, eliminate excess heat in hydrogen fuel cells with the lowest power consumption, and optimize the distribution of circulating working fluid flow channels to reduce internal temperature differences and improve the uniformity of battery temperature distribution.
90% of the heat generated in hydrogen fuel cells is eliminated by the heat dissipation system through thermal conduction and convection, while 10% of the heat is dispersed to the external environment through radiation heat dissipation. Traditional heat dissipation methods include air cooling, liquid cooling, and phase change heat dissipation.
3-Heat Transfer of PEMFC System
3.1 Stack Heat Transfer
After heat is generated inside the PEMFC, it will be transferred between the various components inside the PEMFC and the external environment. The heat transfer inside the fuel cell stack mainly depends on the thermal resistance of each component and the contact thermal resistance between different components. As the gas diffusion layer is the "bridge" connecting the main heat generation component (membrane electrode) and the main heat dissipation component (bipolar plate), its thermal resistance and the size of the contact thermal resistance with other components have a significant impact on the heat transfer performance inside the PEMFC. In addition, the contact thermal resistance between different components can have a significant impact on the internal heat transfer of the fuel cell stack.
3.2 Cooling Liquid Heat Transfer
The cooling methods of fuel cells include air cooling, liquid cooling, and phase change cooling.
The factors that affect coolant heat transfer include the PEMFC stack end, the coolant itself, and the radiator end. The coolant comes into direct contact with the bipolar plate at the end of the PEMFC stack, so the coolant flow channel structure has a significant impact on its heat transfer. In addition, the properties of the coolant itself can also affect the related heat transfer process. Considering the insufficient available space, choosing a coolant with a larger heat capacity can reduce the size of the radiator and improve the thermal management performance of PEMFC. Therefore, the demand for new high-efficiency coolants is becoming increasingly evident.
- |
- +1 赞 0
- 收藏
- 评论 0
本文由莫子若转载自Walmate Official Website,原文标题为:A Overview of Cooling Systems for Hydrogen Fuel Cell Vehicles,本站所有转载文章系出于传递更多信息之目的,且明确注明来源,不希望被转载的媒体或个人可与我们联系,我们将立即进行删除处理。
相关推荐
Key Points in Designing Aluminum Profiles Used in New Energy Vehicles and Energy Storage Battery Packs
The battery pack is a key component of new energy vehicles, energy storage cabinets and containers. It is an energy source through the shell envelope, providing power for electric vehicles and providing consumption capacity for energy storage cabinets and containers. In combination with actual engineering needs, this article summarizes the key points of profile design for battery packs by analyzing the requirements of mechanical strength, safety, thermal management and lightweight of battery packs.
Application of Friction Stir Welding Technology in Battery Tray Manufacturing
At present, the lightweight effect of the aluminum alloy battery tray and plastic top cover scheme is significant and has been adopted by many car manufacturers. The battery tray adopts a scheme of aluminum extrusion profile+friction stir welding+MIG welding, which has low comprehensive application cost, meets the performance requirements, and can achieve the integration of the circulating water channel of water-cooled batteries.
Bidirectional DC DC Converter: A Comprehensive Overview
A bidirectional DC DC converter is a power electronic device that can convert DC power from one voltage level to another in both directions. It has the capability to transfer power bidirectionally between two DC sources, such as batteries, capacitors, or fuel cells, with different voltage levels. This converter is widely used in various applications, such as electric vehicles, renewable energy systems, and energy storage systems, due to its high efficiency, compact size, and low cost.
电池热管理和汽车轻量化制造商迈泰热传授权世强硬创代理
迈泰热传(Walmate)的热管理和轻量化设计和产品,已成功应用在电机、电控、电池和储能等模块上,成为国内诸多汽车主机厂和电池Pack厂和商业储能的首选供应商。
MODEL 63200A SERIES PROGRAMMABLE DC ELECTRONIC LOAD
型号- 63212A-600-840,63205A-600-350,63202A-1200-80,63215A-1200-600,63200A,63203A-150-300,63204A-600-280,63206A-600-420,63206A-150-600,63215A-600-1050,63220A-600-1400,MODEL 63200A SERIES,63202A-150-200,63218A-150-1800,63205A-150-500,63206A-1200-240,63208A-150-800,63204A-1200-160,63215A-150-1500,63210A-1200-400,63212A-1200-480,63210A-150-1000,63200A SERIES,63208A-600-560,MODEL 63200A,63212A-150-1200,63224A-150-2000,63202A-600-140,63218A-1200-720,63210A-600-700,63220A-1200-800,63203A-600-210,63203A-1200-120,63208A-1200-320,63224A-600-1680,63218A-600-1260,63220A-150-2000,63206A-60-1000,MODEL 63206A-60-1000,63205A-1200-200,63204A-150-400,63224A-1200-960
IVT-S high precision current measurement system
型号- 5601230200,5601230400,IVT-S-500-U0-I-CAN1-12/24,IVT-S-1K-U3-I-CAN2-12/24,5600200220,IVT-S-300-U3-I-CAN1-12/24,5601240101,IVT-S-2K5-U3-I-CAN2-12/24,IVT-S-300-U0-I-CAN2-12/24,IVT-S-1K-U0-I-CAN2-12/24,IVT-S-100-U0-I-CAN1-12/24,IVT-S,IVT-S-100-U3-I-CAN1-12/24,IVT-S-1K-U3-I-CAN1-12/24,5601250200,5601250400,IVT-S-500-U3-I-CAN2-12/24,IVT-S-1K-U0-I-CAN1-12/24,IVT-S-300-U3-I-CAN2-12/24,IVT-S-2K5-U0-I-CAN2-12/24,IVT-S-500-U0-I-CAN2-12/24,5600200420,IVT-S-300-U0-I-CAN1-12/24,IVT-S-2K5-U0-I-CAN1-12/24,IVT-S-100-U0-I-CAN2-12/24,IVT-S-100-U3-I-CAN2-12/24,IVT-S-500-U3-I-CAN1-12/24,IVT-S-2K5-U3-I-CAN1-12/24
IVT 3 COMPACT CURRENT SENSING ISAscale® compact high precision current measurement device
型号- IVT 3 SERIES,IVT 3 BASE,IVT 3,IVT 3 PRO
A Guide on Aluminium Extrusion
In recent times, there has been an increased demand for Aluminium Extrusion in product manufacturing and design. This led to an increase in the demand for a professional and reliable Aluminium Extrusion manufacturer.In the course of this article, we will talk about Aluminium Extrusion in detail. Aluminium Extrusion is a process that manufacturers use to create components and parts having certain cross-sectional profiles. To enhance both the properties and appearance of the aluminum, the manufacturer uses different mechanical and surface enhancement processes.
Silicones From Wevo Support The Battery Market to Meet ATEX Requirements, Offering Excellent Thermal Mitigation Properties
WEVO-CHEMIE GmbH has developed several silicone-based products especially for use in the battery systems produced by SAFT Groupe S.A., meeting ATEX requirements and moreover offering UL94 V-0 approval as well as excellent thermal mitigation properties.
液冷板气密性检测合格,为何仍会出现渗液问题?
在液冷板生产制造过程中经过严密气密性测试,针对液冷板出现的渗液问题,本文分析了该问题产生的原因,并提出了相关的预防措施。
Discussion on the Development of Battery Tray for New Energy Vehicles
The three major focuses of current new energy vehicle development - safety, lightweighting, and reliability - are closely related to the battery pack, and the battery housing is the load-bearing component of the battery system, which has a significant impact on the collision, energy consumption, and other aspects of the battery pack and even the entire vehicle.
热设计挑战与散热器加工制造
散热器是电子设备热设计中最常用的散热强化部件,其强化原理是增加换热面积,设计时一般要考虑发热源的热流密度、发热元器件温度要求、产品内部空间尺寸、散热器安装及外观设计等要求。
TCS Series Current Sensing Resistors
型号- TCS SERIES,TCS8518,TCS,TCS8420,TCS14,TCS 8118HR0001F,TCS5216,TCS6018,TCS8118
How to effectively prevent or reduce the impact of thermal deformation of battery tray welding?
Battery trays, also known as battery boxes or PACK boxes, are increasingly valued as a very important component in the development of new energy vehicles. The design of battery trays needs to balance the relationship between factors such as weight, safety, cost, and material performance. Aluminum alloys are widely used in automotive lightweight engineering because of their low density and high specific strength, which can ensure rigidity while ensuring vehicle body performance.
登录 | 立即注册
提交评论