How to effectively prevent or reduce the impact of thermal deformation of battery tray welding?
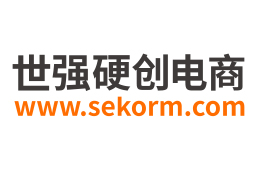
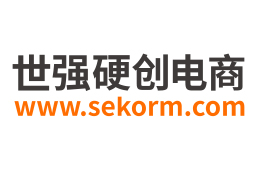
Battery trays, also known as battery boxes or PACK boxes, are increasingly valued as a very important component in the development of new energy vehicles. The design of Battery trays needs to balance the relationship between factors such as weight, safety, cost, and material performance. Aluminum alloys are widely used in automotive lightweight engineering because of their low density and high specific strength, which can ensure rigidity while ensuring vehicle body performance.
1-Battery tray welding location and method selection
Aluminum battery trays are made of extruded aluminum profiles, and the various components are combined into a whole by welding to form a complete frame structure. Similar structures are also widely used in energy storage pack boxes.
The welding parts of the battery tray usually include the bottom plate splicing, the connection between the bottom plate and the side, the connection between the side frame, the horizontal and vertical beams, the welding of liquid cooling system components, and the welding of accessories such as brackets and hanging ears. When selecting welding methods, different welding methods will be selected according to different material and structural requirements, see the table below:
2-Analysis of the influence of welding thermal deformation
Welding is a local heating processing method. Since the heat source is concentrated at the weld, the temperature distribution on the weld is uneven, which eventually leads to welding deformation and welding stress inside the welded structure. Welding thermal deformation is the phenomenon that the shape and size of the welded parts change due to uneven heat input and heat output during the welding process. Combined with actual engineering project experience, the parts that are prone to welding thermal deformation and the influencing factors are summarized:
a. Long straight welding area
In actual production, the bottom plate of the battery tray is generally made of 2 to 4 aluminum alloy profiles spliced together by stir friction welding. The welds are long, and there are also long welds between the bottom plate and the side plate, and between the bottom plate and the spacing beam. Long welds are prone to local overheating in the welding area due to concentrated heat input, resulting in thermal deformation.
Battery tray frame welding
b. Multi-component joints
It is caused by local high temperature heating and subsequent cooling during the welding process at the multi-component weld. During the welding process, the weldment is subjected to uneven heat input, resulting in a significant temperature difference between the weld area and the surrounding parent material, which causes thermal expansion and contraction effects, causing deformation of the welded parts. The electrical installation end of the energy storage pack box is usually equipped with a water nozzle, a wiring harness bracket, a beam, etc., and the welds are dense and very easy to deform.
In the weld-intensive area, the front side of the pallet is warped and deformed
c.Cold plate channel side wall
In the battery tray with integrated design of liquid cooling plate, parts with smaller structural rigidity, such as thin plates and pipe structures, cannot resist thermal deformation well during welding and are prone to deformation. For example, the side wall of the liquid cooling plate flow channel is very thin, generally only about 2mm. When welding beams, wiring harness brackets and other parts on the module mounting surface, it is easy to cause cracks and deformation wrinkles on the side wall of the flow channel, affecting the overall performance.
Thermal crack defects on the liquid cooling channel wall caused by beam welding
3-Welding thermal deformation control method
a. Segment welding, double-sided welding
For parts with relatively low strength requirements, segmented welding is adopted, and the welding process is broken down into multiple small sections. The welds are arranged symmetrically, and the welds are arranged symmetrically near the neutral axis in the construction section, so that the deformations caused by the welds may offset each other. At the same time, the length and number of welds are minimized, and excessive concentration or crossing of welds is avoided, which can reduce the welding temperature gradient and thus reduce welding deformation. For parts with high strength requirements such as the bottom plate, bottom plate and side frame, double-sided welding is adopted to increase strength while reducing bending deformation caused by large parts and long welds.
b.Optimizing welding sequence
Control welding deformation, use joints with lower rigidity, avoid two-way and three-way intersecting welds, and avoid high stress areas. Optimize the welding sequence, weld the weaker rigidity areas first, and the better rigidity areas last, such as welding the fillet welds first, then the short welds, and finally the long welds; weld the transverse welds first, then the longitudinal welds. A reasonable welding sequence can effectively control welding deformation, thereby controlling the weld dimensions.
c.Welding parameter adjustment
Control welding parameters and processes, and reasonably set welding speed, number of welding layers and thickness of each weld. For thicker welds, use multi-layer and multi-channel welding methods, and the thickness of each weld layer should not exceed 4mm. Multi-layer welding can reduce structural microstructure and improve joint performance. Accurately control welding parameters and reasonably select parameters such as welding current, voltage, electrode model and welding speed to ensure consistent shape and size of the molten pool, thereby avoiding errors caused by improper parameter selection.
d.Welding skills improvement
Improve the welder's operating skills (use mechanical processing for large components or nodes with strict requirements) to ensure consistency and standardization of actions during welding and reduce dimensional problems caused by human factors.
- |
- +1 赞 0
- 收藏
- 评论 0
本文由出山转载自Walmate Official Website,原文标题为:How to effectively prevent or reduce the impact of thermal deformation of battery tray welding?,本站所有转载文章系出于传递更多信息之目的,且明确注明来源,不希望被转载的媒体或个人可与我们联系,我们将立即进行删除处理。
相关推荐
液冷板气密性检测合格,为何仍会出现渗液问题?
在液冷板生产制造过程中经过严密气密性测试,针对液冷板出现的渗液问题,本文分析了该问题产生的原因,并提出了相关的预防措施。
A Guide on Aluminium Extrusion
In recent times, there has been an increased demand for Aluminium Extrusion in product manufacturing and design. This led to an increase in the demand for a professional and reliable Aluminium Extrusion manufacturer.In the course of this article, we will talk about Aluminium Extrusion in detail. Aluminium Extrusion is a process that manufacturers use to create components and parts having certain cross-sectional profiles. To enhance both the properties and appearance of the aluminum, the manufacturer uses different mechanical and surface enhancement processes.
热设计中,工程师可以优化哪些设计元素实现有效降本
在散热器设计中,采用有效的降本方式能够提高整体系统的可靠性和效率,同时可以减少不必要的成本。本文介绍了工程师可以优化哪些设计元素实现有效降本。
日本电产集团综合产品目录(Nidec Group Products Catalog)
描述- 日本电产集团发布第10版产品目录,涵盖从精密小型马达到超大型电机的全系列产品。产品应用于信息技术、办公自动化、汽车、机器人、家电、物流、农业等多个领域。公司致力于成为全球领先的驱动技术企业,并积极应对汽车电动化、机器人应用扩展等五大技术创新浪潮。
型号- PM4系列,H300,D SERIES,NRFEIS-5060,DFS,GATS-2000 SERIES,TPI SERIES,GATS-7800 SERIES,R-6100,TVX,GATS-6300,GATS-8600,SX-20,RWI SERIES,ZI20A,GATS-7500系列,LSR-3230,BP100,RSH,GATS-7700 SERIES,K-MC1000,P2H系列,E300,GATS-2000系列,GATS-6300系列,NVM-6060GCP,VL-H系列,GATS-7500,MH3NCV,VL SERIES,GATS-7800系列,SS-SV,DEWE3-A4,TPI,TVX SERIES,RGA20,NRTES-1000 SERIES,FCPL,ΜV1,RSH系列,ZG SERIES,ID300,FMD,TPI系列,GATS-8600系列,S-CART,GATS-6300 SERIES,KS,CM,R-580,SS-SV SERIES,ANEX SERIES,LD SERIES,VP600GC,GE15FR PLUS,MD2,ANEX系列,NRTES-1000,P2H SERIES,FFB,VL系列,LS,RSH SERIES,RVL,VL-H SERIES,RVP,F600,SS-SV系列,S-FLAG,GATS-7500 SERIES,REC-92FT,DEWE3-PA8,ECO-KA,KCV1000-5AX,S-CART-V1000-LFT,RVL SERIES,RVP SERIES,R-700 SERIES,P2H,ZE16C,CPLS,S-CART-V500,HM500S,VM53RⅡ,GATS-7700,ANEX,NRTES-1000系列,HM-X6100,RWI,TVX系列,KA SERIES,S-CART-MINI,GATS-2000,PM4,VL-H,GATS-7700系列,CBZ,GH,GATS-8600 SERIES,R-700,R-5920系列,NRFEIS-3570,DFS SERIES,MVR-HX,MAF130EⅡ,BL-V20,ECO-KA SERIES,SERIES S-FLAG,RWI系列,HE,GATS-7800,R-5920
An overview of Power battery heat dissipation
This paper mainly introduces Walmate‘s introduction to Power battery heat dissipation. At present, Battery trays and energy storage liquid pack boxes from Walmate are available used in energy vehicle manufacturers and energy storage products manufacturers.
电池热管理和汽车轻量化制造商迈泰热传授权世强硬创代理
迈泰热传(Walmate)的热管理和轻量化设计和产品,已成功应用在电机、电控、电池和储能等模块上,成为国内诸多汽车主机厂和电池Pack厂和商业储能的首选供应商。
RH SMD Power Inductor: Superior Performance, Leading the New Trend in Inductor Technology
In today‘s fast-developing technological era, the performance of electronic devices is continuously improving, and the requirements for electronic components are increasingly stringent. The Xiangru RH73 SMD power inductor stands out in the electronic components market due to its high precision, large saturation current, miniaturized design, excellent temperature stability, and reliable quality.
Glpoly XK-D20双组份非硅酮导热结构胶
描述- GLPOLY XK-D20系列是一种新型橡胶改性环氧树脂专利材料,属于双组分非硅热导结构粘合剂。该系列产品具有优异的热传导性、电绝缘性、超强粘接强度和密封性能,适用于电子和机械系统的各种轻质超结构的热管理、电气绝缘、密封和粘接。
型号- XK-D20 SERIES,XK-D20,XK-D20H,XK-D20M,XK-D20L
Rhyton Thermal Conductive Materials and Insulation Materials: Thermal Management Secrets of New Energy Vehicle
Thermal management is an important link in the design of automobile charging piles, which directly affects the stability and service life of it. This article introduces how the thermal potting adhesive, thermal insulator and thermal grease from Rhyton protect the charging gun and charging pile of new energy vehicles.
SNP830气压测量传感器规格书
描述- 本资料为SNP830气压测量传感器的数据手册。该传感器适用于新能源汽车电池包压力监测应用,集成了8位MCU、24位ADC、温度传感器、空气压力传感器和供电电压监控单元。它可实时测量电池包的压力变化,并在压力超出正常范围时提供报警信号。
型号- SNP830,SNP830BNCLE
THPF‐EQ类型
描述- 该资料介绍了3L电子公司生产的THPF-EQ系列电感器的技术规格和应用。这些电感器适用于笔记本电脑、电脑、开关和服务器、基站、DC/DC转换器、新能源汽车和5G等领域。资料提供了详细的电气规格、尺寸图、推荐回流焊接条件、包装规格以及注意事项。
型号- THPF0631EQ-R18M,THPF0531EQ-3R3M,THPF0531EQ-R60M,THPF0521EQ-R82M,THPF0505EQ-100M,THPF0521EQ,THPF0431EQ-4R7M,THPF1508EQ-7R2M,THPF0531EQ-R56M,THPF1010EQ-8R2M,THPF0605EQ-4R3M,0731EQ,THPF0431EQ-1R0M,THPF1010EQ-6R8M,THPF0531EQ-R16M,THPF0631EQ-1R2M,THPF0707EQ-SERIES,0505EQ,THPF0505EQ-SERIES,THPF1510EQ-8R2M,THPF0707EQ-6R8M,THPF0431EQ-3R3M,THPF0631EQ-R33M,THPF0605EQ-2R2M,THPF1508EQ-2R2M,THPF0605EQ-1R5M,THPF1010EQ-1R0M,THPF1510EQ-6R8M,THPF0521EQ-R15M,THPF0531EQ-R33M,THPF1010EQ-4R7M,THPF0606EQ-100M,THPF0521EQ-1R0M,THPF0531EQ-1R2M,THPF0707EQ-4R7M,THPF1510EQ-4R7M,THPF1010EQ-150M,THPF0521EQ-1R5M,1508EQ,THPF1010EQ-3R3M,THPF0731EQ,THPF0631EQ-1R0M,THPF0631EQ-SERIES,THPF0421EQ-1R8M,THPF0631EQ-R68M,THPF0631EQ-R56M,THPF0605EQ-6R8M,THPF0521EQ-R80M,THPF1510EQ,THPF0631EQ-1R8M,THPF0421EQ-1R0M,0431EQ,THPF0606EQ-220M,0521EQ,THPF0631EQ-4R7M,THPF0421EQ-R56M,THPF0431EQ-6R8M,THPF0531EQ-SERIES,THPF0505EQ-5R6M,THPF1508EQ-2R0M,THPF1508EQ-SERIES,0631EQ,THPF0731EQ-1R5M,THPF1508EQ-4R2M,THPF0531EQ,THPF0731EQ-2R2M,THPF0606EQ-5R6M,THPF0531EQ-R47M,THPF0605EQ-R82M,THPF0605EQ-8R2M,THPF0505EQ,THPF0631EQ-3R3M,THPF‐EQ,THPF1010EQ-SERIES,THPF1010EQ-5R6M,THPF0421EQ-R60M,THPF0421EQ-R72M,0707EQ,THPF0606EQ-150M,THPF1510EQ-150M,THPF0606EQ,THPF0531EQ-2R2M,THPF0431EQ-R75M,THPF0531EQ-1R5M,THPF1510EQ-5R6M,THPF0731EQ-4R7M,THPF0605EQ-1R0M,THPF0531EQ-R80M,THPF1508EQ,THPF0505EQ-8R2M,THPF1010EQ-100M,THPF0605EQ-1R8M,THPF‐EQ TYPE,0605EQ,THPF0421EQ-1R2M,THPF0631EQ-4R5M,THPF0605EQ-4R7M,THPF0431EQ-SERIES,THPF0731EQ-1R0M,THPF1010EQ,THPF1510EQ-220M,THPF0731EQ-SERIES,THPF0421EQ,THPF0707EQ-3R3M,THPF0421EQ-R22M,THPF0731EQ-6R8M,THPF0606EQ-SERIES,THPF0731EQ-8R2M,THPF0606EQ-4R7M,1510EQ,THPF1508EQ-6R2M,THPF0421EQ-SERIES,THPF0521EQ-R47M,THPF0606EQ-8R2M,THPF1510EQ-SERIES,THPF0431EQ-2R2M,THPF0605EQ-3R3M,THPF1510EQ-100M,THPF1510EQ-330M,THPF0605EQ-SERIES,THPF0421EQ-R10M,THPF0521EQ-SERIES,0606EQ,THPF0605EQ,THPF0421EQ-R47M,THPF0731EQ-5R6M,THPF0605EQ-1R2M,THPF0531EQ-R82M,THPF1508EQ-3R0M,THPF0731EQ-2R7M,THPF0606EQ-6R8M,THPF1010EQ-2R2M,THPF0521EQ-R16M,THPF0605EQ-5R6M,THPF0707EQ,THPF0521EQ-R68M,THPF0521EQ-R56M,THPF0631EQ,THPF0421EQ-R36M,0531EQ,THPF0531EQ-1R8M,THPF0521EQ-1R2M,THPF0531EQ-4R7M,THPF0731EQ-3R3M,THPF0421EQ-1R5M,THPF0421EQ-2R2M,THPF1508EQ-4R7M,THPF1508EQ-8R2M,1010EQ,THPF1508EQ-5R3M,0421EQ,THPF0631EQ-1R5M,THPF0521EQ-R33M,THPF0531EQ-R15M,THPF0505EQ-6R8M,THPF0631EQ-2R2M,THPF0421EQ-R40M,THPF0531EQ-1R0M,THPF0431EQ
Application of Interface Materials in New Energy Vehicles
As the new energy vehicle market explodes in growth, there is also a large demand for various high-performance interface materials. This article introduces the applications of interface materials in new energy vehicles, and recommends solutions of thermal conductive materials, absorbing materials, adhesive materials etc. from Rhyton.
BASiC Semiconductor Launched Pcore™6 – Automotive 3-Phase Full-bridge SiC MOSFET Module for New Energy Vehicles
The automotive 3-phase Full-bridge SiC MOSFET Module Pcore™6 is designed and launched by BASiC Semiconductor based on the high-performance and high-efficiency requirements of power modules for core traction drivers from automobile manufacturers.
登录 | 立即注册
提交评论