What are the Drone Smart Battery Protocols?
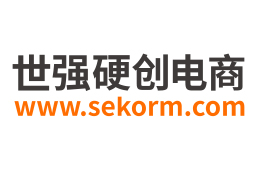
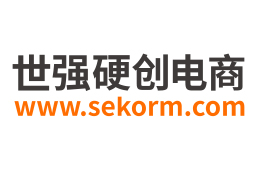
In the rapidly advancing world of drone technology, the importance of
efficient battery management cannot be overstated. As drones become more
powerful and diverse in their applications, the need for smart battery systems
to monitor and optimize performance is crucial. Smart drone batteries, equipped
with advanced communication protocols, play a pivotal role in ensuring safety,
reliability, and extended flight times. This article delves into the various
protocols used in drone smart batteries, examining how they work, their specific
use cases, and how they interact with other drone systems to enhance overall
functionality.
What is a Drone Smart Battery?
A smart drone battery is a type of battery designed with built-in intelligence (via a Battery Management System, or BMS) that allows it to provide detailed real-time information about its status, health, and performance. This includes data on voltage, current, temperature, state of charge (SoC), state of health (SoH), and cycle life. Smart batteries can also support safety features like overcurrent protection, overcharge/overdischarge protection, and temperature regulation to prevent damage to the battery or drone.
In contrast, an ordinary non-smart battery simply provides power without offering any additional data or safety management features. These batteries typically rely on external devices (like an external charger or monitor) to track their charge level, and they lack the built-in sensors and communication interfaces found in smart batteries.
Common Smart Drone Battery Protocols
The smart drone battery protocols are designed to monitor and manage the health, status, and performance of drone batteries in real-time. These protocols allow the BMS to communicate essential information such as voltage, current, temperature, SoC, and SoH to the drone’s flight controller, ensuring safe and efficient operation. The choice of protocol depends on the specific application, performance requirements, and the drone’s design.
1. I2C (Inter-Integrated Circuit)
●Description: A serial communication protocol often used for low-speed, short-distance communication between devices on the same circuit board or inside a system.
●Usage: Commonly used for battery monitoring, particularly in consumer drones and smaller drones. It allows the Battery Management System (BMS) to communicate data to the flight controller.
●Advantages:
1. Simple and cost-effective
2. Low power consumption
3. Allows multiple devices to share the same communication bus
●Disadvantages:
1. Short communication range (limited to devices on the same circuit board or close to each other)
2. Slower data transfer rate compared to other protocols
2. CAN Bus (Controller Area Network)
●Description: A robust and high-speed communication protocol designed for distributed systems, allowing different devices (such as motors, sensors, and battery management systems) to communicate efficiently with each other.
●Usage: Used for more advanced drones, particularly in industrial, commercial, and high-performance applications where fast and reliable communication is needed. It is especially suitable for heavy-lifting drones or drones requiring multiple systems to communicate.
●Advantages:
1. High-speed communication with low latency
2. Supports long-distance communication
3. Highly reliable in noisy environments
4. Can handle multiple devices on the same bus without performance degradation
●Disadvantages:
1. Requires more complex wiring and hardware than I2C
2. Higher cost in terms of implementation and components
3. SMBus (System Management Bus)
●Description: A subset of I2C designed for power management in computers and embedded systems. It is often used for battery monitoring and communication with devices like chargers, sensors, and the BMS.
●Usage: Typically used in smaller drones or applications that do not require the high-speed performance of CAN Bus. It is commonly found in consumer-grade drones.
●Advantages:
1. Relatively simple to implement
2. Uses the same principles as I2C, so it can be compatible with I2C-based systems
●Disadvantages:
1. Slower than CAN Bus
2. Short-range communication
4. UART (Universal Asynchronous Receiver-Transmitter)
●Description: A serial communication protocol that allows asynchronous data exchange between devices.
●Usage: Often used for battery monitoring and communication with flight controllers. Some consumer drones use UART for basic battery status communication.
●Advantages:
1. Simple to implement and use
2. Low cost
3. Can operate at higher speeds compared to I2C and SMBus
●Disadvantages:
1. Less reliable for multi-device communication than I2C and CAN Bus
2. Communication range is typically limited
5. Bluetooth Low Energy (BLE)
●Description: A wireless communication protocol designed for short-range, low-power data transfer.
●Usage: Often used for monitoring battery status and communicating with mobile apps or ground control stations. BLE can be used for real-time battery monitoring via smartphones or tablets, providing data on battery health and status.
●Advantages:
1. Wireless communication provides flexibility and convenience
2. Low power consumption, ideal for battery-powered devices
●Disadvantages:
1. Short communication range (typically 10–100 meters)
2. Limited data bandwidth, so it’s not suitable for high-speed, large-data applications
6. Modbus
●Description: A serial communication protocol used for industrial control systems. It’s commonly used for integrating devices like sensors and battery management systems.
●Usage: Industrial drones or fleets of drones might use Modbus to communicate battery data across different devices or networked systems.
●Advantages:
1. Robust and widely used in industrial applications
2. Supports multiple devices and long communication ranges
●Disadvantages:
1. More complex to implement than simpler protocols like I2C or UART
2. Slower data transfer rates than CAN Bus
7. Wi-Fi
●Description: Wi-Fi is used for high-speed, long-range wireless communication between drones and ground control stations, and can also be used for monitoring battery status in some advanced systems.
●Usage: High-end consumer drones or commercial drones may use Wi-Fi to transmit battery data, along with telemetry and video feeds.
●Advantages:
1. High-speed data transfer (can handle video feeds and telemetry data alongside battery monitoring)
2. Long-range communication (can work over several hundred meters to kilometers, depending on the setup)
●Disadvantages:
1. Consumes more power than BLE or other low-power wireless protocols
2. Can be subject to interference in crowded Wi-Fi environments
What are the Differences Between Using Different Protocols?
1. Speed and Latency
●CAN Bus is the fastest and most reliable for real-time communication with minimal latency, which is critical for drones requiring fast data exchange between the battery and flight controller, especially during high-performance flights.
●I2C and SMBus are slower but are sufficient for consumer drones where high-speed communication is not as critical.
●UART offers higher speeds than I2C but is not as commonly used for battery management in drones.
●BLE and Wi-Fi are suitable for lower-speed, less critical applications, such as monitoring battery status through a mobile device.
2. Range and Reliability
●CAN Bus supports longer distances (several meters) and is highly reliable in noisy environments, which makes it ideal for large drones and commercial applications.
●I2C is limited to short-range communication (typically on the same circuit board or within a device), and is thus more suited for smaller drones.
●BLE offers limited range (around 100 meters), making it suitable for local monitoring but not for flight-critical communication.
●Wi-Fi has the potential for long-range communication but may suffer from interference in crowded wireless environments.
3. Power Consumption
●BLE is specifically designed for low-power applications, making it ideal for battery-powered systems where minimal power drain is critical.
●I2C, SMBus, and UART are also low-power protocols, but they may not be as efficient as BLE in terms of energy use.
●CAN Bus and Wi-Fi consume more power due to their higher speed and longer range.
4. Complexity and Cost
●I2C and UART are relatively simple to implement and low-cost, making them suitable for consumer drones and basic battery management systems.
●CAN Bus is more complex and requires additional hardware, but it is necessary for high-performance and industrial-grade drones where robustness and speed are required.
●Wi-Fi and BLE offer convenience and flexibility but require wireless modules that add to the cost and power consumption.
5. Data Transfer Capacity
●CAN Bus supports high throughput and is capable of transmitting more data in real-time without much delay, making it ideal for data-heavy applications like industrial drones or drones used for heavy-lifting.
●Wi-Fi also supports high data transfer, especially for video streaming, telemetry, and battery data.
●I2C and SMBus offer lower data rates, which may limit their use in more complex applications.
Which Protocol Should I Choose?
The choice of protocol for smart drone batteries depends on the drone's application, performance requirements, and cost considerations:
●For consumer drones, I2C, SMBus, or UART may be sufficient for basic battery management and monitoring.
●For industrial, commercial, or heavy-lifting drones, CAN Bus is often preferred due to its high speed, robustness, and longer communication range.
●Wi-Fi and BLE offer flexibility for wireless communication but are generally used for more non-critical tasks like battery status updates via mobile devices.
The protocol choice also impacts power consumption, data transfer speed, and reliability, so the trade-offs must be considered when designing a drone system.
What are the Differences between Battery Protocol and Drone Protocol?
The communication protocols used by drone smart batteries and drones themselves are often related but serve different functions within the drone system. While there is some overlap, the protocols used by drones and their batteries are designed to address distinct aspects of the drone's operation, from battery monitoring to full drone control and telemetry. Here’s a breakdown of the differences between the protocols used for smart batteries and those used by the drone as a whole:
1. Purpose of the Protocols
●Drone Smart Batteries:
The communication protocols used by smart batteries focus on monitoring the battery's health, status, and performance. These protocols provide data about the battery's voltage, current, temperature, state of charge (SoC), state of health (SoH), cycle count, and other critical metrics that help ensure safe and efficient operation. The battery's communication system often communicates with the Battery Management System (BMS), which manages charging, discharging, and protection.
●Drones:
The communication protocols used by drones encompass a wider range of systems including the flight controller, navigation, remote control communication, telemetry, and payload systems (e.g., cameras, sensors). These protocols ensure real-time control of the drone, as well as the exchange of flight data between the drone and the operator, or between the drone and its onboard systems.
Protocols for drones include flight control, telemetry, remote communication (e.g., video feeds), and sometimes system diagnostics.
2. Common Protocols for Smart Batteries vs. Drones
●Battery Protocols:
These protocols are primarily used for monitoring battery-specific parameters. Examples include:
I2C (Inter-Integrated Circuit), CAN Bus (Controller Area Network), SMBus (System Management Bus), UART (Universal Asynchronous Receiver-Transmitter) and Bluetooth Low Energy (BLE).
●Drone Protocols:
These protocols manage the drone’s overall control and telemetry, ensuring communication between the drone and its controller, or its onboard and external systems. Common drone communication protocols include:
◆MAVLink (Micro Air Vehicle Link) – A protocol for drone flight control and telemetry (used in open-source autopilot systems like ArduPilot and PX4).
◆Wi-Fi – Used for video transmission, telemetry, and sometimes control commands.
◆Radio Frequency (RF) protocols – Including Wi-Fi, 2.4 GHz/5.8 GHz, and proprietary RF systems used by commercial drones for control and telemetry (e.g., DJI Lightbridge).
◆Bluetooth – Often used for local, short-range control and data transfer (e.g., for mobile app interaction).
◆Ethernet – In some advanced drones, used for fast, wired communication, especially in industrial or high-performance drones.
◆GPS/GLONASS – Navigation and position data protocols for real-time location tracking.
3. Differences in Data Types
●Battery Communication:
Data exchanged via battery protocols focuses heavily on voltage, current, temperature, and other metrics that influence battery health and usage.
The protocols used by batteries may transmit data such as charge level, discharge rate, temperature limits, state of charge (SoC), and state of health (SoH).
●Drone Communication:
Drones use a variety of protocols for different kinds of telemetry, control commands, navigation, and payload management.
This includes protocols for flight data (e.g., altitude, velocity, orientation), remote control signals, GPS data, video feed, and mission planning.
4. Data Transmission Range and Speed
●Battery Protocols:
Many battery protocols (e.g., I2C, SMBus, CAN Bus) are designed for short-range communication between components inside the drone or with a ground station.
CAN Bus, for example, allows fast, reliable communication between the battery and the flight controller but doesn’t need long-range communication.
BLE is also used for short-range, low-power communication, typically between the battery and a mobile device for status updates.
●Drone Protocols:
Drone communication protocols (e.g., MAVLink, Wi-Fi, RF communication) often need to cover longer distances and support higher data transfer rates, particularly for remote control and telemetry, as well as video transmission.
Wi-Fi and RF protocols are used for longer-range communication between the drone and its operator or control system.
5. Interaction with Other Drone Systems
●Battery Protocols:
Battery communication primarily interfaces with the Battery Management System (BMS) to monitor and control the battery’s health.
The BMS typically communicates directly with the flight controller to prevent battery over-discharge, ensure proper charging, and report battery status to the operator.
●Drone Protocols:
Drones have a more complex communication system where multiple protocols interact:
Flight controller protocols handle communication with the motors, GPS, and gyros to ensure stable flight.
Telecommunication protocols (e.g., Wi-Fi, RF) ensure data transfer between the drone and the operator's remote control, or enable payload control (e.g., camera, sensor systems).
Navigation protocols like GPS ensure the drone knows its position and can follow waypoints or be remotely controlled.
6. Complexity of Communication
●Battery Protocols:
Battery communication protocols are often simpler because the battery's role is more limited to power management, rather than full-system control.
●Drone Protocols:
Drone communication protocols are generally more complex, as they manage a variety of subsystems, from flight control to telemetry and payload control.
Do Smart Battery and Drone Protocols Need to Be the Same?
No, they do not need to use the same protocol, but they must be compatible. They have different roles and are designed to handle different types of data. The battery protocol is focused on the health and power management of the battery, while the drone protocol is focused on control and telemetry for the entire drone. The drone's flight controller and battery management system (BMS) can use different protocols as long as the flight controller can read and interpret the data from the battery and use it to manage flight and power efficiently. The protocols need to be interoperable or there should be a way for the systems to communicate via conversion mechanisms.
What are the Compatibility Issues Between Battery Protocol and Drone Protocol?
Compatibility between these protocols is essential for smooth operation. Here's how compatibility works and how potential issues might arise:
1.Protocol Mismatch:
If the battery uses a protocol that the drone's flight controller does not support, there could be issues with data exchange. For instance, if the drone expects I2C communication but the battery only supports CAN Bus, then the data from the battery would not be accessible to the flight controller, and the battery’s status might be unavailable.
However, most modern drone flight controllers are designed to support multiple communication protocols. If the battery uses a protocol like CAN Bus and the drone is designed to support it, there won't be compatibility issues. In some cases, the drone might also be compatible with several protocols, meaning it can accept I2C for the battery while using MAVLink or Wi-Fi for drone telemetry.
2. Different Protocols for Different Functions:
Drone systems are often designed to support different protocols for different subsystems. For example:
●Battery data might be transmitted via I2C or CAN Bus, since these are designed for power and health monitoring.
●Flight control and telemetry might use MAVLink, Wi-Fi, or RF, depending on the distance and data rates needed for communication.
This separation of concerns ensures that each protocol serves the right purpose: battery protocols focus on safe power management, and drone protocols focus on flight control and overall system management.
3. Communication Gateways or Converters
If there is a mismatch between the battery and drone protocols, one option is to use a communication gateway or protocol converter. This device can translate between different protocols (e.g., converting CAN Bus data to I2C or UART), allowing the battery to communicate with the flight controller even if they use different communication protocols.
4. Overlapping Protocols (e.g., CAN Bus)
Some high-end drone systems use CAN Bus for both the battery and flight control. In such cases, the flight controller and BMS are on the same bus, and the data from the battery is directly integrated into the drone's control system. This approach reduces the potential for compatibility issues.
MAVLink, used for telemetry, could also be part of the same network, sending both battery status and flight data over a unified communication system.
5. Wireless Communication (e.g., BLE, Wi-Fi)
For drones that use Bluetooth Low Energy (BLE) or Wi-Fi to communicate with the battery, wireless communication can be more flexible. The drone app or ground control system can pull battery data via BLE or Wi-Fi and integrate it with flight control information, as long as both systems support the same wireless standards.
Conclusion
Choosing the right smart battery protocol is critical to maximizing a drone's performance and longevity. Understanding the differences between battery protocols and drone communication systems allows manufacturers and operators to make informed decisions tailored to their needs. With the continued evolution of drone technology, the integration of advanced protocols will play a key role in shaping the future of aerial robotics, offering improved safety, efficiency, and capabilities across a wide range of industries. As a global leader in UAV battery production and R&D, Grepow provides cutting-edge smart drone batteries with CAN protocol support. Whether you're flying industrial drones, commercial aircraft, or heavy-lift vehicles, our batteries deliver the reliable performance you need.
- |
- +1 赞 0
- 收藏
- 评论 0
本文由wenxia转载自Grepow official website,原文标题为:What are the Drone Smart Battery Protocols?,本站所有转载文章系出于传递更多信息之目的,且明确注明来源,不希望被转载的媒体或个人可与我们联系,我们将立即进行删除处理。
相关研发服务和供应服务
相关推荐
Grepow 14S LiPo Battery Solutions are Designed to Deliver Exceptional Performance and Durability
In the realm of high-performance drones, power is paramount. Ensuring your aircraft is equipped with the right battery is not just a matter of flight time, but also of safety and reliability. Grepow, a leader in the drone battery industry, offers a range of cutting-edge solutions, including their 14s LiPo batteries, designed to deliver exceptional performance and durability for professional applications.
格瑞普负40度还能正常工作的磷酸铁锂电池,尺寸灵活,可进行专业化定制
深圳市格瑞普电池有限公司研发出了负40度还能正常工作的磷酸铁锂电池,一举打破了市场上的空缺,值得一提的是这负40度跟市场上大部分低温电池(可定制)产品不一样,格瑞普低温电池是实打实的低温。
【元件】格瑞普钢壳异形电池全新上市,为未来智能产品创新提供助力
格瑞普带着全球领先的钢壳异形电池产品和服务再次来到大众的视野!随着科技的进步,智能可穿戴设备愈发增多,且对产品空间的需求更加严格;因此,深圳市格瑞普特推出全新的,钢壳异形电池,为新时代的AI产品增加助力!
电安科技(DA TECHNOLOGY)陶瓷贴片保险丝选型指南
目录- Ceramic Chip Fuse Product overview CC201 Ceramic Chip Fuse CC202 Ceramic Chip Fuse CC203 Ceramic Chip Fuse CC204 Ceramic Chip Fuse CC211 Ceramic Chip Fuse CC212 Ceramic Chip Fuse CC213 Ceramic Chip Fuse CC221 Ceramic Chip Fuse
型号- CC212A008,CC212A007,CC212A006,CC221A01.5,CC212A001,CC213A03.5,CC213A.500,CC212A005,CC212A004,CC212A003,CC212A002,CC212A03.5,CC203A.250,CC203A.375,CC201A02.5,CC204A006,CC204A005,CC202A015A,CC204A008,CC204A007,CC221A.315,CC201A.250,CC203A02.5,CC213A.750,CC202A003,CC202A004,CC202A01.5,CC202A001,CC202A002,CC202A007,CC202A008,CC202A005,CC201A.375,CC202A006,CC221A02.5,CC203A.750,CC202A1.25,CC204A020,CC202A.630,CC202A015,CC202A.750,CC202A012,CC202A010,CC203A1.25,CC204A04.5,CC201A01.5,CC204A025,CC212A02.5,CC221,CC211A01.5,CC221A.375,CC203A.500,CC203A03.5,CC202A025,CC202A02.5,CC221A.250,CC204A012,CC202A020,CC204A010,CC204A015,CC203A001,CC203A002,CC203A003,CC211A.375,CC221A03.5,CC203A008,CC213A01.5,CC203A004,CC221A.500,CC203A005,CC203A006,CC203A007,CC221A002,CC213A005,CC221A003,CC221A001,CC201A04.5,CC202A030,CC221A004,CC204,CC203,CC211A.250,CC202,CC201,CC212A01.5,CC213A002,CC213A001,CC213A004,CC213A003,CC201A007,CC201A008,CC201A001,CC201A002,CC201A003,CC211A02.5,CC201A004,CC201A005,CC221A.750,CC204A030,CC202A03.5,CC202A012A,CC213,CC212,CC211,CC203A020,CC211A.750,CC201A010,CC213A02.5,CC201A012,CC201A015,CC221A.200,CC201A03.5,CC201A.500,CC203A012,CC211A.500,CC203A010,CC201A020,CC203A015,CC211A03.5,CC201A025,CC203A01.5,CC213A.375,CC213A.250,CC211A008,CC211A007,CC201A030,CC211A004,CC211A003,CC211A006,CC211A005,CC201A.750,CC202A04.5,CC211A002,CC211A001
2022 Commercial UAV EXPO | Grepow shows it‘s key products: Tattu Smart Battery, Smart Drone Battery, and TA3000 Charger
At the Commercial UAV EXPO 2022, Grepow will introduce you to the key products: Tattu Smart Battery, Smart Drone Battery, and TA3000 Charger.
Drone Mapping vs. Drone Surveying: What’s the Difference?
This article mainly tells Grepow about the difference between drone mapping and drone surveying and introduces the working principle of the two types of drones.
What is the Impact of Long Coldness on Agriculture Spraying UAVs Batteries and How to Deal with it
Agricultural drones are not only used for spraying and applying medicine, but also for spreading fertilizer, seeds, and feeds to meet the diversified needs of farmers and improve production efficiency.
Tips for maintenance and emergency disposal of agriculture drone battery
In this article, Grepow talks about how the agriculture drone battery is daily maintained, and how to dispose of it when there is an emergency.
NMC Battery vs. LCO Battery: What’s the Difference?
When it comes to lithium-ion batteries, two of the most commonly discussed chemistries are NMC (Nickel Manganese Cobalt) and LCO (Lithium Cobalt Oxide). Both are widely used in a variety of applications, from electric vehicles to consumer electronics, but they differ significantly in terms of chemical composition, energy density, cycle life, and cost. Understanding the key differences between NMC and LCO batteries is essential for choosing the right battery for specific applications, whether you‘re powering a smartphone or an electric vehicle.
Grepow Won the 2021 Specialized Innovative Enterprise Award
On January 9, 2022, Grepow won the 2021 Specialized Innovative Enterprise Award in the 7th UAV 100 People Conference and 2022 China Industry Spring Festival Gathering.
Tattu Pro High-capacity Drone Smart Battery ——The Newest Advance in UAV Power
Tattu Pro is available as a 22000mAh capacity solution in both 12S and 14S formats, giving a power output of 976.8Wh and 1139.6Wh respectively. Both versions are rated at 25C and support 3C fast charging for rapid turnaround, with a 600+ charge/discharge cycle lifespan.
3D Mapping Drone Helps Create The Popular Game Black Myth: Wukong
The use of drone 3D mapping in the creation of Black Myth: Wukong exemplifies the transformative impact of modern technology on the gaming industry. By combining advanced photogrammetry and 3D modeling techniques, developers can now bring rich, detailed environments to life with unprecedented accuracy and efficiency. This not only enhances the visual quality and immersion of games but also significantly reduces the time and cost associated with traditional modeling methods.
Grepow was delightly present to witness AI Drone from the UZH VS Human Challenge as one of the partners
The Human vs AI Drone Race, organised by the University of Zurich Robotics and Perception Group, took place this past weekend at Swiss Drone Days, and as one of the partners, Tattu (Grepow Battery) was delighted to be there to witness this historic moment!
The Grepow Tattu NMC 811 Battery – New Power For UAVs
The Tattu NMC 811 battery from Grepow, the innovation that can power our world. Delivering all this in a compact, long working time UAV battery delivers new opportunities for UAV pilots.
What Is A 12S Lipo Battery?
A 12s LiPo battery is a high-voltage, rechargeable power source commonly used in various applications, particularly in drones, electric vehicles, and RC models. The “12s“ designation indicates that the battery consists of 12 cells connected in series. Each cell in a LiPo battery typically has a nominal voltage of 3.7 volts. Therefore, a 12s configuration means the total nominal voltage of the battery is 12 times 3.7 volts, providing substantial power output suitable for high-demand applications.
电子商城
服务
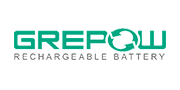
可自由定制电池形状,锂离子聚合物/磷酸铁锂成分,放电倍率Max. 50C (持续放电倍率) / 150C (脉冲放电倍率),充电倍率:Max. 5,厚度可达0.5mm。
最小起订量: 5000 提交需求>
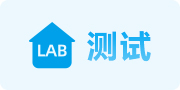
使用FloTHERM和Smart CFD软件,提供前期热仿真模拟、结构设计调整建议、中期样品测试和后期生产供应的一站式服务,热仿真技术团队专业指导。
实验室地址: 深圳 提交需求>
登录 | 立即注册
提交评论