Key Points in Designing Aluminum Profiles Used in New Energy Vehicles and Energy Storage Battery Packs
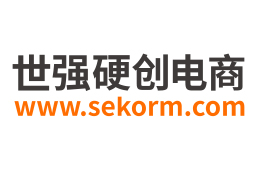
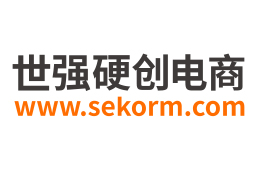
The battery pack is a key component of new energy vehicles, energy storage cabinets and containers. It is an energy source through the shell envelope, providing power for electric vehicles and providing consumption capacity for energy storage cabinets and containers. In combination with actual engineering needs, this article summarizes the key points of profile design for battery packs by analyzing the requirements of mechanical strength, safety, thermal management and lightweight of battery packs.
1-Battery pack housing design requirements
a.Mechanical strength, vibration resistance and impact resistance. After the test, there should be no mechanical damage, deformation or loosening of the fastening, and the locking mechanism should not be damaged.
b.Sealing: The sealing of the battery pack directly affects the working safety of the battery system. It is usually required to reach IP67 protection level to ensure that the battery pack is sealed and waterproof.
c.The design of the battery pack shell needs to take thermal management performance into consideration and ensure that the battery operates within an appropriate range through appropriate thermal management design.
d.For installation and fixation, the shell should have space for nameplate and safety signs, and reserve sufficient space and fixed foundation for the installation of acquisition lines, various sensor elements, etc.
e. All connectors, terminals, and electrical contacts of non-polar basic insulation should meet the corresponding protection level requirements when combined.
f.Lightweighting: Lightweighting of the shell is of great significance to improving the energy density of the battery pack. Aluminum alloy is light in weight and high in quality, making it the most feasible choice at present. The lightweighting level can be improved through appropriate extreme design in combination with actual applications.
g.Durability: The design life of the battery pack shell shall not be less than the service life of the overall product. No obvious plastic deformation should occur during the use cycle. The protection level and insulation performance should not be reduced. The structure should be easy to maintain, including the layout of nameplates and safety signs, and protection of connectors.
Figure 1 Typical aluminum alloy welded battery pack shell
2-Typical aluminum alloy battery pack shell solution
Commonly used aluminum alloy materials for battery pack shells include 6061-T6, 6005A-T6 and 6063-T6, etc. These materials have different yield strengths and tensile strengths to meet different structural requirements. The strength of these materials is: 6061-T6>6005A-T6>6063-T6.
At present, the battery pack shell forming solutions include aluminum profile welding, aluminum alloy casting, cast aluminum plus profile aluminum, stamped aluminum plate welding, etc. The aluminum profile welding solution has become the mainstream choice due to its flexibility and processing convenience. As shown in Figure 1, the shell is mainly composed of an aluminum alloy profile frame and an aluminum alloy profile bottom plate, which are welded using 6 series aluminum alloy extruded profiles. The aluminum alloy casting solution is regarded as the future development direction due to its simplified process and cost reduction potential.
3- Profile section design
a. Section size and complexity: The section size of the profile is measured by the circumscribed circle. The larger the circumscribed circle, the greater the extrusion pressure required. The section of the profile is usually composed of multiple cavities to improve the structural rigidity and strength. Usually, the frame, middle partition, bottom plate, beam, etc. adopt different section designs to adapt to different structural and functional requirements.
Figure 2 Typical aluminum alloy profile section
b. Aluminum profile wall thickness: The minimum wall thickness of a specific aluminum profile is related to the profile circumscribed circle radius, shape and alloy composition. For example, when the wall thickness of 6063 aluminum alloy is 1mm, the wall thickness of 6061 aluminum alloy should be about 1.5mm. The extrusion difficulty of the same section is: 6061-T6>6005A-T6>6063-T6. In the design of battery pack profiles, the frame profile is usually made of 6061-T6 aluminum alloy material, and its typical section is composed of multiple cavities, and the thinnest wall thickness is about 2mm; the bottom plate profile is also composed of multiple cavities, and the material is generally 6061-T6, 6065A-T6, and the thinnest wall thickness is also about 2mm; in addition, in the design of the bottom plate load-bearing tray and bottom plate liquid cooling integration, the bottom plate generally adopts a double-sided structure, the bottom plate thickness is generally 10mm, and the wall thickness and the inner wall of the cavity are about 2mm.
c. Tolerance of profile cross-sectional dimensions: The tolerance of cross-sectional dimensions should be determined based on the processing allowance of the aluminum profile, the conditions of use, the difficulty of profile extrusion, and the shape of the profile. For some aluminum profiles that are difficult to extrude, the shape can be changed or the process allowance and dimensional tolerance can be increased to reduce the difficulty of extrusion and extrude aluminum profile products that are close to the requirements, and then they can be reshaped or processed to meet the use requirements.
In addition, when designing the profile section, it is necessary to consider the specific requirements of different welding processes for joints, grooves, wall thickness, etc.
- |
- +1 赞 0
- 收藏
- 评论 0
本文由雪飘梦飞转载自Walmate Official Website,原文标题为:Key points in designing aluminum profiles used in new energy vehicles and energy storage battery pac...,本站所有转载文章系出于传递更多信息之目的,且明确注明来源,不希望被转载的媒体或个人可与我们联系,我们将立即进行删除处理。
相关推荐
FAKRA Connectors: Powering the Future of Automotive Technology
FAKRA connectors have become essential components for radio frequency signal connections in the automotive industry. As the trend of connected vehicles and the Internet of Everything gains momentum, FAKRA connectors are seeing a surge in demand. A major factor driving this growth is the rapid adoption of ADAS, which continues to expand as vehicles become more intelligent.
Application of Interface Materials in New Energy Vehicles
As the new energy vehicle market explodes in growth, there is also a large demand for various high-performance interface materials. This article introduces the applications of interface materials in new energy vehicles, and recommends solutions of thermal conductive materials, absorbing materials, adhesive materials etc. from Rhyton.
热设计挑战与散热器加工制造
散热器是电子设备热设计中最常用的散热强化部件,其强化原理是增加换热面积,设计时一般要考虑发热源的热流密度、发热元器件温度要求、产品内部空间尺寸、散热器安装及外观设计等要求。
Glpoly XK-D20双组份非硅酮导热结构胶
GLPOLY XK-D20系列是一种新型橡胶改性环氧树脂专利材料,属于双组分非硅热导结构粘合剂。该系列产品具有优异的热传导性、电绝缘性、超强粘接强度和密封性能,适用于电子和机械系统的各种轻质超结构的热管理、电气绝缘、密封和粘接。
金菱通达 - TWO-COMPONENT NON-SILICONE THERMAL CONDUCTIVE STRUCTURAL ADHESIVE,双组分非硅酮导热结构胶,XK-D20 SERIES,XK-D20,XK-D20H,XK-D20M,XK-D20L,机车车辆,NEW ENERGY VEHICLES,航空航天,新能源汽车,ROLLING STOCK,AEROSPACE
电池热管理和汽车轻量化制造商迈泰热传授权世强硬创代理
迈泰热传(Walmate)的热管理和轻量化设计和产品,已成功应用在电机、电控、电池和储能等模块上,成为国内诸多汽车主机厂和电池Pack厂和商业储能的首选供应商。
Xiangru Molded Inductor XRTC252012S with High Efficiency and Energy Saving, Opening a New Era of Efficient Circuits
Molded inductors, as core members of the circuit world, are injecting powerful energy into numerous electronic products with cutting-edge technology and excellent performance, leading the industry to new heights. Xiangru‘s XRTC252012S molded inductor stands out with its unique integrated molding process.
液冷板气密性检测合格,为何仍会出现渗液问题?
在液冷板生产制造过程中经过严密气密性测试,针对液冷板出现的渗液问题,本文分析了该问题产生的原因,并提出了相关的预防措施。
BASiC Semiconductor Launched Pcore™6 – Automotive 3-Phase Full-bridge SiC MOSFET Module for New Energy Vehicles
The automotive 3-phase Full-bridge SiC MOSFET Module Pcore™6 is designed and launched by BASiC Semiconductor based on the high-performance and high-efficiency requirements of power modules for core traction drivers from automobile manufacturers.
液冷板制造过程中的流道污染风险及清洁控制技术
液冷板是一种高效的散热组件,如果液冷板的流道不干净,会影响到冷却液的流动均匀性,过大颗粒的异物还会造成冷却液受到阻塞或流动不畅,进而影响电子设备的散热效率和整体性能。针对冷板内部流道的清洗是消除流道污染、提升流道洁净度的必要措施。
Rhyton High-Performance Silicone-Free Thermal Pads Escort for Electronic Equipment
HiPad4000SF is a silicone-free thermal pad material based on thermoplastic resin, whose thermal conductivity can reach 4W/m·K, and long-term use temperature can reach 125℃. It will not release or volatilize siloxane components during the working process.
SNP830气压测量传感器规格书
本资料为SNP830气压测量传感器的数据手册。该传感器适用于新能源汽车电池包压力监测应用,集成了8位MCU、24位ADC、温度传感器、空气压力传感器和供电电压监控单元。它可实时测量电池包的压力变化,并在压力超出正常范围时提供报警信号。
琻捷 - AIR PRESSURE MONITORING SENSOR,AIR PRESSURE MEASUREMENT SENSOR,气压测量传感器,气压监测传感器,SNP830,SNP830BNCLE,NEW ENERGY VEHICLE BATTERY PACK PRESSURE MONITORING,新能源汽车电池组压力监测,BATTERY PACK PRESSURE MONITORING,NEW ENERGY VEHICLES,新能源汽车,电池组压力监测
SUPU‘s Energy Storage Connector Products Shape Zero-carbon Future
SUPU, as a total solution provider of electrical connectivity, specializes in providing customers with safe and reliable energy storage connector products and solutions that are used in various energy storage system environments. With superior technology and full production capacity, SUPU‘s products are widely used by major energy storage customers.
AKJ82C06AS 60V常开(1-Form-A)光学MOSFET继电器临时数据表
本资料为AKJ82C06AS型60V常开(1-Form-A)光MOSFET继电器的数据手册。资料详细介绍了该继电器的特性、电气特性、典型特性、封装尺寸以及订购信息,适用于电信、测量设备、工业自动化、控制设备和新能源汽车等领域。
方舟微 - 常开(1-FORM-A)光学MOSFET继电器,NORMALLY OPEN (1-FORM-A) OPTICAL MOSFET RELAY,AKJ82C06AS,MEASUREMENT EQUIPMENT,INDUSTRIAL AUTOMATION,工业自动化,CONTROL EQUIPMENT,NEW ENERGY VEHICLES,新能源汽车,无线通讯,控制设备,TELECOMMUNICATIONS,测量设备
登录 | 立即注册
提交评论