Key Points in Designing Aluminum Profiles Used in New Energy Vehicles and Energy Storage Battery Packs
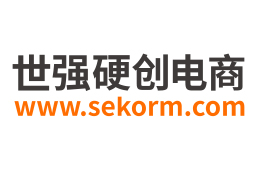
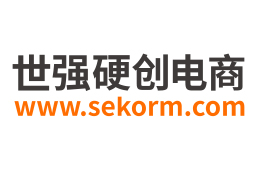
The battery pack is a key component of new energy vehicles, energy storage cabinets and containers. It is an energy source through the shell envelope, providing power for electric vehicles and providing consumption capacity for energy storage cabinets and containers. In combination with actual engineering needs, this article summarizes the key points of profile design for battery packs by analyzing the requirements of mechanical strength, safety, thermal management and lightweight of battery packs.
1-Battery pack housing design requirements
a.Mechanical strength, vibration resistance and impact resistance. After the test, there should be no mechanical damage, deformation or loosening of the fastening, and the locking mechanism should not be damaged.
b.Sealing: The sealing of the battery pack directly affects the working safety of the battery system. It is usually required to reach IP67 protection level to ensure that the battery pack is sealed and waterproof.
c.The design of the battery pack shell needs to take thermal management performance into consideration and ensure that the battery operates within an appropriate range through appropriate thermal management design.
d.For installation and fixation, the shell should have space for nameplate and safety signs, and reserve sufficient space and fixed foundation for the installation of acquisition lines, various sensor elements, etc.
e. All connectors, terminals, and electrical contacts of non-polar basic insulation should meet the corresponding protection level requirements when combined.
f.Lightweighting: Lightweighting of the shell is of great significance to improving the energy density of the battery pack. Aluminum alloy is light in weight and high in quality, making it the most feasible choice at present. The lightweighting level can be improved through appropriate extreme design in combination with actual applications.
g.Durability: The design life of the battery pack shell shall not be less than the service life of the overall product. No obvious plastic deformation should occur during the use cycle. The protection level and insulation performance should not be reduced. The structure should be easy to maintain, including the layout of nameplates and safety signs, and protection of connectors.
Figure 1 Typical aluminum alloy welded battery pack shell
2-Typical aluminum alloy battery pack shell solution
Commonly used aluminum alloy materials for battery pack shells include 6061-T6, 6005A-T6 and 6063-T6, etc. These materials have different yield strengths and tensile strengths to meet different structural requirements. The strength of these materials is: 6061-T6>6005A-T6>6063-T6.
At present, the battery pack shell forming solutions include aluminum profile welding, aluminum alloy casting, cast aluminum plus profile aluminum, stamped aluminum plate welding, etc. The aluminum profile welding solution has become the mainstream choice due to its flexibility and processing convenience. As shown in Figure 1, the shell is mainly composed of an aluminum alloy profile frame and an aluminum alloy profile bottom plate, which are welded using 6 series aluminum alloy extruded profiles. The aluminum alloy casting solution is regarded as the future development direction due to its simplified process and cost reduction potential.
3- Profile section design
a. Section size and complexity: The section size of the profile is measured by the circumscribed circle. The larger the circumscribed circle, the greater the extrusion pressure required. The section of the profile is usually composed of multiple cavities to improve the structural rigidity and strength. Usually, the frame, middle partition, bottom plate, beam, etc. adopt different section designs to adapt to different structural and functional requirements.
Figure 2 Typical aluminum alloy profile section
b. Aluminum profile wall thickness: The minimum wall thickness of a specific aluminum profile is related to the profile circumscribed circle radius, shape and alloy composition. For example, when the wall thickness of 6063 aluminum alloy is 1mm, the wall thickness of 6061 aluminum alloy should be about 1.5mm. The extrusion difficulty of the same section is: 6061-T6>6005A-T6>6063-T6. In the design of battery pack profiles, the frame profile is usually made of 6061-T6 aluminum alloy material, and its typical section is composed of multiple cavities, and the thinnest wall thickness is about 2mm; the bottom plate profile is also composed of multiple cavities, and the material is generally 6061-T6, 6065A-T6, and the thinnest wall thickness is also about 2mm; in addition, in the design of the bottom plate load-bearing tray and bottom plate liquid cooling integration, the bottom plate generally adopts a double-sided structure, the bottom plate thickness is generally 10mm, and the wall thickness and the inner wall of the cavity are about 2mm.
c. Tolerance of profile cross-sectional dimensions: The tolerance of cross-sectional dimensions should be determined based on the processing allowance of the aluminum profile, the conditions of use, the difficulty of profile extrusion, and the shape of the profile. For some aluminum profiles that are difficult to extrude, the shape can be changed or the process allowance and dimensional tolerance can be increased to reduce the difficulty of extrusion and extrude aluminum profile products that are close to the requirements, and then they can be reshaped or processed to meet the use requirements.
In addition, when designing the profile section, it is necessary to consider the specific requirements of different welding processes for joints, grooves, wall thickness, etc.
- |
- +1 赞 0
- 收藏
- 评论 0
本文由雪飘梦飞转载自Walmate Official Website,原文标题为:Key points in designing aluminum profiles used in new energy vehicles and energy storage battery pac...,本站所有转载文章系出于传递更多信息之目的,且明确注明来源,不希望被转载的媒体或个人可与我们联系,我们将立即进行删除处理。
相关推荐
Application of Friction Stir Welding Technology in Battery Tray Manufacturing
At present, the lightweight effect of the aluminum alloy battery tray and plastic top cover scheme is significant and has been adopted by many car manufacturers. The battery tray adopts a scheme of aluminum extrusion profile+friction stir welding+MIG welding, which has low comprehensive application cost, meets the performance requirements, and can achieve the integration of the circulating water channel of water-cooled batteries.
热设计挑战与散热器加工制造
散热器是电子设备热设计中最常用的散热强化部件,其强化原理是增加换热面积,设计时一般要考虑发热源的热流密度、发热元器件温度要求、产品内部空间尺寸、散热器安装及外观设计等要求。
The Application of IGBT in the Electronic Control System of New Energy Vehicles and Its Heat Dissipation Technology
The main heating device in the electronic control system of new energy vehicles is the inverter, which converts the direct current of the battery into alternating current that can drive the motor. During this process, the IBGT in the inverter will generate a large amount of heat. To solve the heat dissipation problem of these devices, this article will introduce the working principle of inverters and advanced liquid cooling heat dissipation technology.
电池热管理和汽车轻量化制造商迈泰热传授权世强硬创代理
迈泰热传(Walmate)的热管理和轻量化设计和产品,已成功应用在电机、电控、电池和储能等模块上,成为国内诸多汽车主机厂和电池Pack厂和商业储能的首选供应商。
GLPOLY XK-D20 Two-component Non-silicone Thermal Conductive Structural Adhesive
型号- XK-D20 SERIES,XK-D20,XK-D20H,XK-D20M,XK-D20L
BASiC Semiconductor Launched Pcore™6 – Automotive 3-Phase Full-bridge SiC MOSFET Module for New Energy Vehicles
The automotive 3-phase Full-bridge SiC MOSFET Module Pcore™6 is designed and launched by BASiC Semiconductor based on the high-performance and high-efficiency requirements of power modules for core traction drivers from automobile manufacturers.
A Guide on Aluminium Extrusion
In recent times, there has been an increased demand for Aluminium Extrusion in product manufacturing and design. This led to an increase in the demand for a professional and reliable Aluminium Extrusion manufacturer.In the course of this article, we will talk about Aluminium Extrusion in detail. Aluminium Extrusion is a process that manufacturers use to create components and parts having certain cross-sectional profiles. To enhance both the properties and appearance of the aluminum, the manufacturer uses different mechanical and surface enhancement processes.
液冷板气密性检测合格,为何仍会出现渗液问题?
在液冷板生产制造过程中经过严密气密性测试,针对液冷板出现的渗液问题,本文分析了该问题产生的原因,并提出了相关的预防措施。
Two-component Non-silicone Thermal Conductive Structural Adhesive XK-D12 Series
型号- XK-D12 SERIES,XK-D12H,XK-D12L,XK-D12M
SUPU‘s Energy Storage Connector Products Shape Zero-carbon Future
SUPU, as a total solution provider of electrical connectivity, specializes in providing customers with safe and reliable energy storage connector products and solutions that are used in various energy storage system environments. With superior technology and full production capacity, SUPU‘s products are widely used by major energy storage customers.
Discussion on the Development of Battery Tray for New Energy Vehicles
The three major focuses of current new energy vehicle development - safety, lightweighting, and reliability - are closely related to the battery pack, and the battery housing is the load-bearing component of the battery system, which has a significant impact on the collision, energy consumption, and other aspects of the battery pack and even the entire vehicle.
服务
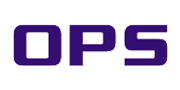
可烧录IC封装SOP/MSOP/SSOP/TSOP/TSSOP/PLCC/QFP/QFN/MLP/MLF/BGA/CSP/SOT/DFN;IC包装Tray/Tube/Tape;IC厂商不限,交期1-3天。支持IC测试(FT/SLT),管装、托盘装、卷带装包装转换,IC打印标记加工。
最小起订量: 1pcs 提交需求>
登录 | 立即注册
提交评论