An In-Depth Guide to Drone Motors
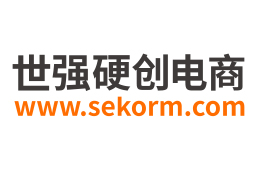
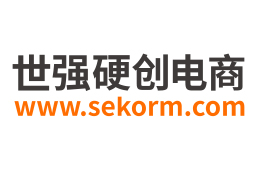
Drone motors are the heart of any drone's propulsion system, directly influencing the performance, efficiency, and reliability of the aircraft. The type, design, and specifications of a drone motor play essential roles in defining the drone's capabilities, from endurance and speed to payload capacity and agility. Understanding the intricacies of these motors is crucial for enthusiasts and professionals alike. This article explores the main types of drone motors, their operation, the key factors to consider in selection, and recent advancements in motor technology.
Types of Drone Motors
The primary types of drone motors are brushed and brushless motors, each with unique structures, performance characteristics, and applications. Here's a breakdown of each:
1. Brushed Motors
●Structure: Structure: Brushed DC motors consist of a simple design with a rotor that has windings and a commutator, along with brushes that maintain contact with the rotor to supply current.
●How they work: Brushed motors use carbon brushes to conduct electricity to the rotating armature. The brushes wear down over time, reducing the motor's lifespan.
●Performance: Brushed motors are less efficient and powerful than brushless motors, and they generate more heat. They are typically used in low-cost or toy drones where high performance is not critical.
2. Brushless Motors (BLDC)
●Structure: Brushless motors have a stator (stationary part) with copper windings and a rotor with permanent magnets. Instead of brushes, they use an electronic speed controller (ESC) to control the switching of current in the windings.
●How they work: Brushless motors use electronic speed controllers (ESCs) to switch the current to the stator windings, creating a rotating magnetic field that spins the rotor.
●Performance: Higher efficiency, durability, less heat generation, more power, and greater torque for weight. They are also quieter and support high-speed operation. They are used in most modern drones, from small quadcopters to large delivery drones.
Key Specifications for Selecting a Drone Motor
When selecting a motor for a drone, understanding the specifications and factors that influence thrust and efficiency is crucial. Here’s an outline of the main factors to consider:
●Motor Size: Drone motors are often specified by a number format like 2212, where the first two digits refer to stator diameter (in mm) and the last two refer to stator height. Larger stators generally produce more torque, which supports larger propellers. Smaller motors are lighter and more responsive but have lower thrust and power output.
●KV Rating: Measured in RPM per volt (RPM/V), this indicates the motor speed at a given voltage. Lower KV motors provide more torque, suitable for larger props and heavier drones; higher KV motors suit smaller, faster drones with smaller props.
KV Rating and RPM
The KV rating (RPM per volt) indicates how many revolutions per minute (RPM) a motor will turn for each volt applied. For example, a motor with a KV rating of 1000 will spin at 1000 RPM when supplied with 1 volt.
KV Rating and Torque
A higher KV motor produces less torque for the same current because the windings are typically optimized for high speed rather than high torque. Conversely, a lower KV motor has more windings, which increases resistance but allows for greater torque at lower speeds.
Higher torque enables faster changes in propeller speed, allowing the drone to respond more quickly to control inputs, which is essential for agile maneuvers and maintaining stability in windy conditions. However, excessive torque can lead to jerky movements and potential instability, especially in delicate maneuvers.Thus, balancing torque with efficiency is key for optimal drone performance, especially in designs focused on extended flight time.
●Maximum Continuous Current and Power Rating: This indicates the maximum amount of current the motor can handle continuously without overheating. A higher current rating allows for more powerful motors and longer flight times. Ensure that the motor’s current draw and power output match the battery and ESC (electronic speed controller) specifications. Exceeding these limits can overheat and damage the motor or ESC.
●Voltage Compatibility: Choose a motor that supports the battery voltage of the drone (e.g., 3S, 4S, 6S batteries, where ‘S’ indicates the number of cells). Higher voltages generally allow higher power outputs but must be compatible with the motor's design.
●Internal Resistance: Lower internal resistance leads to higher efficiency and better power output.
●Propeller Compatibility: The choice of propeller size and pitch must match the motor specifications to optimize thrust and efficiency. Larger propellers typically generate more thrust but require more power from the motor.
●Weight: The motor weight impacts the overall weight of the drone, which in turn affects flight time and maneuverability. Choose a motor that balances power with an acceptable weight for the drone’s purpose.
What Does The Number of Poles and Magnets (N And P) Mean?
We usually see terms like 12N14P in the motor parameters of drones. What does it mean? In fact, 12 represents the number of electromagnetic poles in the motor's stator. 14 indicates the number of permanent magnets installed on the rotor. In the context of drone motors, the terms "poles" and "magnets" are often used interchangeably, but they represent distinct components within the motor's construction.
●Poles: These are the electromagnetic coils in the stator (the stationary part of the motor) that generate a magnetic field when energized.Commonly, drone motors have between 4 and 24 poles, depending on their application. A higher pole count generally means smoother, more precise motor control, which is essential for applications like drone stabilization.
●Magnets: These are permanent magnets embedded in the rotor. The number of magnets is often close to the number of poles, though not necessarily identical, as it depends on the motor's design to create synchronous or asynchronous rotation patterns.
How N and P Impact Motor Efficiency?
The configuration of poles and magnets impacts motor efficiency and performance in several ways:
●Smoothness and Control: More poles and magnets can lead to smoother operation and better torque characteristics. This is because they allow for more frequent magnetic interactions, which can reduce cogging torque (the resistance to movement when the rotor is stationary) and enhance responsiveness during flight.
●Torque Production: A higher pole and magnet count generally increases the torque output and makes the motor more suitable for applications requiring greater thrust, like lifting heavier payloads or steady hovering in stable flight , as it allows the drone to respond quickly to control inputs without significant lag.
Efficiency and Speed: Motors with fewer poles and magnets typically spin at higher speeds with less torque. For high-speed drones, a low pole/magnet count is often chosen to achieve faster RPMs (revolutions per minute).
How Does The Size of the Propeller Affect the Motor?
Larger or higher-pitched propellers generate more lift but require more torque, meaning they pair best with low-KV, high-torque motors to avoid overload and maintain efficiency. Conversely, smaller or lower-pitched propellers work well with high-KV motors, favoring speed over lift. Larger propellers generally produce more thrust but may reduce speed and efficiency, while smaller propellers offer higher speeds but lower thrust. Propeller type—such as material (carbon fiber for rigidity, plastic for flexibility) and blade count—also impacts stability, thrust, and efficiency.
How Do Voltage and Current Requirements Affect Motor Selection and Battery Pairing?
Voltage and current requirements are fundamental in motor selection and battery pairing, as they determine the motor’s power output and efficiency. Motors rated for higher voltage can achieve higher RPMs, delivering more power, but they also demand a compatible battery with sufficient voltage output, such as a higher cell-count LiPo battery (e.g., 6S, 12S). Current, on the other hand, affects the motor's torque and responsiveness; higher current draw increases torque but also generates more heat, requiring both efficient cooling and a battery that can supply the necessary current without quickly depleting. Mismatching voltage or current capabilities can lead to reduced performance, motor damage, or even battery failure.
What Is the Role of The ESC in The Motor System of A Drone?
Electronic speed controllers (ESCs) are essential in drone motor systems, serving as the link between the flight controller, battery, and motors. ESCs regulate the power supplied to each motor by adjusting the voltage and current, which directly controls motor speed and ensures precise synchronization. They interpret signals from the flight controller to modulate motor RPMs, enabling smooth acceleration, braking, and directional adjustments, which are vital for stability and maneuverability. In brushless motors, ESCs convert direct current (DC) from the battery into three-phase alternating current (AC), which is necessary for motor operation. Each motor typically requires its own ESC, enabling independent speed adjustments that contribute to stable flight and maneuverability. Additionally, ESCs can incorporate features like active braking and battery management, enhancing overall performance by ensuring efficient power use and preventing battery damage.
What Are the Latest Advancements in Drone Motor Technology?
Recent advancements in drone motor technology focus on enhancing efficiency, power density, and control precision to improve flight performance. Innovations include the development of brushless motors with higher magnetic strength, which increase torque without significantly raising size or weight, resulting in more compact and powerful designs. Improved cooling mechanisms, such as integrated airflow systems and heat-resistant materials, allow motors to operate at higher current levels without overheating, crucial for sustained high-performance flights. Additionally, sensor-based technologies, like field-oriented control (FOC) and motor position sensors, provide smoother and more precise motor control, enhancing stability and responsiveness. Besides, improvements in electronic speed controllers (ESCs) have enabled more precise control and responsiveness, facilitating better flight performance. These improvements allow drones to achieve longer flight times, better stability in challenging conditions, and optimized performance in specialized applications like heavy lifting, racing, and aerial photography.
How to Choose a Motor for Specific Applications?
Drones are now widely used in various applications such as racing, aerial photography, industry, and logistics. How do you choose the right motor for different drone applications?
●Racing Drones: High-KV, high-RPM motors for agility and speed.
●Aerial Photography: Low-KV, high-torque motors for smooth, stable flight with large props.
●Industrial Drones: Low-KV motors with high torque for lifting payloads and maintaining stability.
●Delivery Drones: Efficient, high-thrust motors for carrying payloads over long distances.
In each case, proper motor selection ensures that the drone meets the demands of its intended use, balancing speed, efficiency, and thrust capacity.
Drone motors come in a variety of types and configurations, each with unique advantages. Understanding how each motor type functions, along with key specifications like KV rating, thrust, and ESC compatibility, is essential in selecting the right motor. As drone technology continues to evolve, motor advancements will likely play a pivotal role in achieving higher efficiency, greater power, and more specialized functionality across a wide range of drone applications. Grepow offers UAV batteries and semi-solid state batteries ranging from 4S (14.8V) to 18S (68.4V) with capacities up to 84Ah, designed to support a wide variety of applications and compatible with drones equipped with diverse motor setups.
- |
- +1 赞 0
- 收藏
- 评论 0
本文由飞猫警长转载自Grepow Official Website,原文标题为:An In-Depth Guide to Drone Motors,本站所有转载文章系出于传递更多信息之目的,且明确注明来源,不希望被转载的媒体或个人可与我们联系,我们将立即进行删除处理。
相关推荐
What is the Impact of Long Coldness on Agriculture Spraying UAVs Batteries and How to Deal with it
Agricultural drones are not only used for spraying and applying medicine, but also for spreading fertilizer, seeds, and feeds to meet the diversified needs of farmers and improve production efficiency.
What Is a Semi-Solid State Battery?
Semi-solid state batteries are a type of rechargeable battery that uses a semi-solid electrolyte instead of the liquid or gel electrolytes found in traditional lithium-ion batteries. The semi-solid electrolyte is typically composed of a solid, conductive material suspended in a liquid electrolyte. This unique composition offers several advantages over conventional battery designs.
What Batteries are Used for AGVs and AMRs?
With AGVs offering structured, reliable performance and AMRs delivering flexibility and autonomy, these mobile industrial robots are revolutionizing the way materials are handled. The choice of battery plays a crucial role in their performance, and as the industry evolves, we can expect to see further innovations in battery technology that will enhance the capabilities of both AGVs and AMRs. As a global leading lipo battery manufacturer, Grepow offers high-energy-density semi-solid state batteries and lipo batteries that perfectly meet the needs of AGVs and AMRs.
Tips for maintenance and emergency disposal of agriculture drone battery
In this article, Grepow talks about how the agriculture drone battery is daily maintained, and how to dispose of it when there is an emergency.
What are the Drone Smart Battery Protocols?
Smart drone batteries, equipped with advanced communication protocols, play a pivotal role in ensuring safety, reliability, and extended flight times. This article delves into the various protocols used in drone smart batteries, examining how they work, their specific use cases, and how they interact with other drone systems to enhance overall functionality.
Low Altitude Economy Benchmarking Enterprise | Grepow Gained Two Major Awards
On January 7th, the ‘2024 National UAV and Unmanned Systems Industry Spring Festival Gathering and the Ninth UAV Hundred People Summit‘ concluded successfully at Shenzhen‘s Window of the World Caesar‘s Palace. Nearly a thousand industry experts and UAV entrepreneurs from across the country gathered to discuss new strategies for low-altitude eco+nomic growth and explore emerging trends in UAV development.
Multirotor vs Fixed Wing vs VTOL UAV: What’s the Difference?
As a global leading lipo battery manufacturer, Grepow offers professional customizable UAV battery solutions to meet the needs of all knids of multirotor, fixed-wing and VTOL drone applications.
3D Mapping Drone Helps Create The Popular Game Black Myth: Wukong
The use of drone 3D mapping in the creation of Black Myth: Wukong exemplifies the transformative impact of modern technology on the gaming industry. By combining advanced photogrammetry and 3D modeling techniques, developers can now bring rich, detailed environments to life with unprecedented accuracy and efficiency. This not only enhances the visual quality and immersion of games but also significantly reduces the time and cost associated with traditional modeling methods.
NMC Battery vs. LCO Battery: What’s the Difference?
When it comes to lithium-ion batteries, two of the most commonly discussed chemistries are NMC (Nickel Manganese Cobalt) and LCO (Lithium Cobalt Oxide). Both are widely used in a variety of applications, from electric vehicles to consumer electronics, but they differ significantly in terms of chemical composition, energy density, cycle life, and cost. Understanding the key differences between NMC and LCO batteries is essential for choosing the right battery for specific applications, whether you‘re powering a smartphone or an electric vehicle.
Grepow‘s New Fast-charge Battery NMC 532 Increases UAV Charging Speed By 60%
NMC 532 is a Grepow Inc. new fast-charge battery produced by utilizing a new formula. This material ratio gives a charging rate up to 5C.
What Is A 12S Lipo Battery?
A 12s LiPo battery is a high-voltage, rechargeable power source commonly used in various applications, particularly in drones, electric vehicles, and RC models. The “12s“ designation indicates that the battery consists of 12 cells connected in series. Each cell in a LiPo battery typically has a nominal voltage of 3.7 volts. Therefore, a 12s configuration means the total nominal voltage of the battery is 12 times 3.7 volts, providing substantial power output suitable for high-demand applications.
Grepow Newly Released Dual Channel Smart Chargers TA7200 and TA9000PRO for Industrial UAV/Drones
The high charging efficiency of the TA7200 and TA9000PRO ensures that drone batteries are quickly recharged, maintaining continuous and efficient operation of agricultural spraying drones, thereby significantly improving agricultural productivity and management efficiency.
Grepow Unveils Newest Product at UAV EXPO! Exclusive On-Site Showcase!
At booth 9B53 of the UAV EXPO, Mr. Chen Bohai, Deputy General Manager of Grepow Batteries, is introducing Grepow‘s latest products to everyone. Grepow has launched three new products within less than a year, with two flagship products specifically designed for agricultural spraying drones.
New NMC 811 Battery is The Reliable Energy for Drones Tattu with An Energy Density of 275 Wh/Kg
The new NMC 811 battery from Grepow has a long life cycle of over 600 cycles, and it has an energy density of 275 Wh/Kg.
格瑞普电池选型表
格瑞普锂电池,磷酸铁锂电池,高压锂电池,镍氢电池,低温锂电池,快充电池,三元锂电池选型表。倍率(C):1~50C,容量(mAh):48~40000mAh,电压:1.2V~4.35V
产品型号
|
品类
|
倍率Rate(C)
|
Thickness(mm)
|
Width(mm)
|
Length(mm)
|
容量(mAh、mA)
|
Voltage(V)
|
CP6431122-R1A
|
三元锂电池
|
1C
|
6.4mm
|
31mm
|
122mm
|
3000mAh
|
3.7V
|
选型表 - 格瑞普 立即选型
电子商城
服务
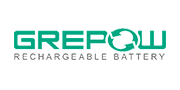
可自由定制电池形状,锂离子聚合物/磷酸铁锂成分,放电倍率Max. 50C (持续放电倍率) / 150C (脉冲放电倍率),充电倍率:Max. 5,厚度可达0.5mm。
最小起订量: 5000 提交需求>
登录 | 立即注册
提交评论