Heat Sink Selection and Mechanical Criteria
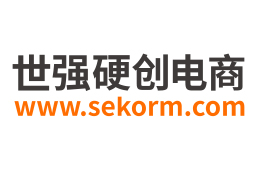
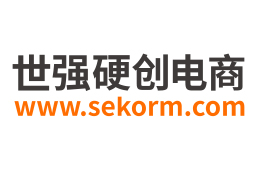
Heat sink selection, taking into account mechanical conditions and requirements other than thermal criteria, is also decisive for the long-term reliable function of devices, modules or systems.
It no longer suffices to restrict heat sink selection to dimensions such as length, width and height. It is equally important for quality assessment purposes, to understand the correlation that decisively influences the overall quality in the design and planning phase.
Heat sinks made of aluminium alloy as extrusion profiles (extruded sections) are partly subject to other criteria than those applicable to pressure die-cast parts or bent metal parts and other conditions must be taken into account during machining. It is therefore often necessary to take this criteria of considerable importance into account during the development phase.
In the total concept of a device, the heat sink is a part that must match different components. It is therefore important during design to take into account that deviations from the nominal dimensions, i.e. tolerances, can be considerable during extrusion. An extruded section is produced by a heated aluminium block, the extrusion billet, being pushed through a tool, the die, with negative shaping of the contour to be produced . ( Photo 1 )
The high deformation forces that occur require correspondingly high section tolerances, so that considerable effort is necessary to minimise these tolerances.
Reference DIN standards define a ± tolerance zone from a few tenths up to several millimetres, depending on the size of the section; not only dimensions such as length, width and height must be taken into account, angular displacement (inclination), distortion and plane-parallelism as well as wall thickness tolerance or curvature of the cross-section are also important assessment criteria. The standards DIN 17615 and 1748 contain exact specifications and it is recommended to become familiar with them.
DIN 17615 is entitled :"Precision profiles of AlMgSi05" and contains the limit deviations for extrusion profiles of sections not exceeding that which can be circumscribed by a circle of 300 mm diameter. DIN 1748 applies to sections greater than 300 mm (Fig. 1).
The manufacture of profiles with restricted tolerances results in considerable additional costs due to a lower output per unit of time, and higher discard as a consequence of increased selection expenditure.
The following example clearly illustrates that this expenditure may also have to be taken into account:
According to DIN, the planeness of a heat sink (here, the curvature of the cross-section and linear distortion) to which the components, e.g. IGBT, are screwed, is for example ±1 mm. However, the required planeness for good thermal contact of the IGBT should not exceed ±0.5 mm. Two options are available: a) additional machining (milling) of the profile base produces a planeness of ±0.2 mm and costs the sum of x; b) purchasing a heat sink from a well known manufacturer who produces profiles with a reduced tolerance zone, e.g. half the limit deviations specified in DIN. The profile price a) is less than b), however, profile b) can be used partly or wholly without additional machining and therefore saves considerable costs.
This applies in general and naturally refers also to other limit deviations such as angular displacement, plane-parallelism, etc.
This restricted tolerance zone is of significant importance, for example, also when a heat sink profile is used as an integral part of an enclosure and all aforementioned conditions must contribute to dimensionally and optically perfect function, but milling work is to be avoided. (Fig. 2).
When machining a heat sink , e.g. contour milling, drilling or thread cutting, etc., general tolerances according to DIN 7168 or DIN ISO 2768 apply unless otherwise specified on the drawing; the tolerance class m = medium is used, i.e. DIN 7168.
To clearly illustrate using an example (Fig. 3) it can be shown how the general tolerances from press tolerances and manufacturing tolerances can be favourably structured by appropriate dimensioning.
Shifting the zero point from the outside edge to the profile centre alone can considerably reduce the tolerance band, in this example referenced to the axis of symmetry, by the amount of 1.1 mm. In order to eliminate the deflections of extrusion profiles, the base areas of the heat sink can be milled.
The baseplate becomes thinner with material removal, which must be taken into account in the determination of drilling and thread depths as well as blind holes (Photo 2).
In the example shown (Fig. 4), the baseplate can be up to 0.8 mm thinner than the nominal value after surface milling, since the profile tolerances are 0.2 mm convex (crowned) and 0.8 mm concave (hollow).
Machining according to DIN 74 is shown in the extracts for example:
A) Clearance hole according to DIN 74 A m 3, counterbore on base side and fin undercut.
B) Clearance hole with fin undercut according to DIN 74 H m 4 and counterbore from the fin side.
C) Thread M6, thread depth calculated as: Thread dimension multiplied by 1.6 plus 2 mm trepanning depth results in 11.6 mm. Hole at fin base undercut and spotfaced -- 12x0.5 on the base side.
D) Blind thread M4, thread depth 4x1.6 = 6.4 mm plus 2 mm results in a drilling depth of 8.4 mm.
Larger areas on heat sinks must be surface milled in order to achieve good planeness. If the cutter diameter should be smaller than the area to be milled due to the manufacturing process, so-called milling edges appear due to parallel milling.
These are edges in the one thousandth, at a maximum one hundredth millimetre range which normally have no influence on the function of heat transmission or assembly. (Fig. 5).
If these milling paths are to remain invisible, it is practical to specify in the drawing, areas in which no milling edges are required; this requirement is met as far as technically feasible.If these milling paths are to remain invisible, it is practical to specify in the drawing, areas in which no milling edges are required; this requirement is met as far as technically feasible.
The given explanations show that the classification and assignment of press and manufacturing tolerances is unproblematic when the available influencing options are used in a knowledgeable manner. A compilation of selection criteria, based on the area of application of the heat sink enables costs and delivery times to be reduced.
The given explanations show that the classification and assignment of press and manufacturing tolerances is unproblematic when the available influencing options are used in a knowledgeable manner. A compilation of selection criteria, based on the area of application of the heat sink enables costs and delivery times to be reduced.
- |
- +1 赞 0
- 收藏
- 评论 0
本文由耳神666转载自Walmate News,原文标题为:Heat sink selection and mechanical criteria,本站所有转载文章系出于传递更多信息之目的,且明确注明来源,不希望被转载的媒体或个人可与我们联系,我们将立即进行删除处理。
相关推荐
Thermal Design Challenges and Heatsinks Manufacturing
Heat sink is the most commonly used heat dissipation strengthening component in electronic device thermal design. Its strengthening principle is to increase the heat exchange area. When designing, it is generally necessary to consider the heat flux density of the heat source, the temperature requirements of the heating components, the internal space size of the product, the installation and appearance design of the heat sink, and other requirements.
How To Select A Suitable Heat Sink To Effectively Increase The Mass And Surface Area Of Their Heat-dissipating Junctions
Power transistors and modules, many power-supply regulator assemblies, and high-current diodes typically generate more heat than their own mass can safely dissipate. For this reason, power devices must securely fasten to a suitable heat sink to effectively increase the mass and surface area of their heat-dissipating junctions.
How to Design A Rectangular Fin Heatsink
In applications where volumetric power density and heat flux density requirements are not high, rectangular fin heatsinks are favored by engineers due to their simple structure, reasonable manufacturing cost, and good heat dissipation performance.
OBIS LX/LS散热器带风扇的散热器,用于热管理
该资料介绍了OBIS LX/LS激光器的散热器(Heat Sink)及其附件。散热器具有紧凑的设计,可提供热管理和方便的激光束高度调整。它支持垂直或水平极化安装,并配备了集成风扇和振动隔离功能。
COHERENT - 散热片,HEAT SINK,1193289,OBIS LX,OBIS LS
What Is the Purpose of a Heat Sink in a Transistor Circuit?
In this article, Yuanyang will introduce how heat sinks work and why they are essential in transistor circuits.
How to Maintain the Heat Sink?
With the continuous upgrading of electronic products, the importance of the heat sink has become increasingly prominent. In order to ensure its efficient heat dissipation and extend its service life, it is essential to regularly maintain the Heat Sink. This article introduces how to maintain the heat sink.
Do Walmate have any quality certifications?
Walmate is a ISO 9001 & IATF 16949 & ISO 14001 Certified Factory.
A custom Heat Sink Manufacturer YY Thermal Provides Customers with Professional Custom Heat Sink Manufacturing, Design, and Solutions
YY Thermal as a custom heatsink manufacturer, YY Thermal’s engineering team can provide a custom heat sink design using the most appropriate manufacturing process according to customer requirements, or provide custom heat sink manufacturing according to customer’s drawing.
Can Walmate provide CMM report?
Walmate does not provide design services, so you will have to have a CAD file ready to use our service. You are responsible for submitting 2D and 3D CAD drawings, and we can then provide a Design for Manufacturing (DFM) review upon receiving your order.
How does Walmate ensure the quality of my parts?
Walmate takes a proactive approach to customer’s quality concerns from the initial communication, providing cost-effective and rationalized advice from designs, materials, production processes, manufacturability, etc. Once your order is confirmed, we will perform a full Design for Manufacturing (DFM) review to point out any issues that our engineers feel may affect the quality of your parts. We have the ability to share inspection data with you in real-time so we can work together to address any quality issues you may have during production. All incoming materials will meet your design specifications. Final inspection reports before shipment.
Can Walmate make design drawings for me?
Walmate does not provide design services, so you will have to have a CAD file ready to use our service. You are responsible for submitting 2D and 3D CAD drawings, and we can then provide a Design for Manufacturing (DFM) review upon receiving your order.
Do Walmate offer OQC reports? Like material cert and FAQ?
Walmate offers OQC reports upon request.If required, we can produce additional documentation on material certs, inspection reports, certificates of conformance, etc. We just ask that this information is requested upfront on the order as it becomes very difficult to get something like a material cert afterward!
电子商城
现货市场
登录 | 立即注册
提交评论