High-Power Burn-In Testing in 2023: How to Overcome the Extreme

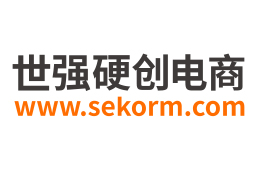

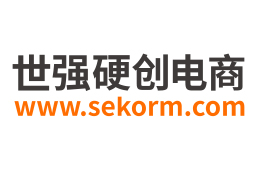
The tech zeitgeist is all about the extreme. The more advanced our devices become by the day, the more they evolve – and consumers’ expectations of them.
Today’s consumers have an unflinching expectation for reliability in their devices, especially critical ones like those in the military or medical fields.
To ensure the reliability of these devices, they have to be tested in the same extreme environments they will be used in. And to ensure these devices fulfill their purpose, the internal components must successfully withstand the extreme temperatures and conditions we’re seeing today.
Semiconductor devices are running at such heat, it can be difficult to establish a balance of temperature with the right components within the application. Which internal pieces will be able to ensure high functionality and longevity through the heat? As an industry, we look to next-generation electronics to fill that gap with reliable high-power burn-in sockets that can withstand these unprecedented temperatures and conditions.
Let’s talk about burn-in testing today, how it’s multi-faceted, and how it should come with an answer to overcoming the extreme.
Thermal Simulation and Analysis Prior to Burn-In
A common gap in today’s semiconductor reliability testing is thermal simulation and analysis of the problem. Why is the device overheating or not functioning as it should? You can’t move forward into testing and prototyping without a firm grasp of the issue – no matter how complex.
This lack of knowledge impacts businesses from the ground up, especially in industries like edge computing (which is a part of many other industries). One mistake could take down an entire system, wasting valuable time and money, and losing customers.
In the past, getting this knowledge was a great deal of iterative guesswork. Today, we conduct thermal testing, which helps us witness the engineering behavior of the inner components and predict on the front end where the efficiency level could go up – no more guessing. This took away a lot of the extra iteration, and now we know specifically where to make changes and adjustments for the best outcome.
Burn-In Testing 101
Once Smiths Interconnect knows the problem and establishes solutions unique to your application, Smiths Interconnect starts putting your product to the test, moving into the burn-in phase. Burn-in testing – or high-temperature operating life (HTOL) testing – is a testing process designed to detect early failures in components and reduce the potential for defects and failures in the field. During burn-in, the component endures extreme operating conditions, including temperature extremes, high-use cycles, and high voltages.
Through this process, Smiths Interconnect aim to eliminate defective components or those with short lifespans before they can become a factor in a system failure. Components have the potential to fail at three points in their lifespan.
1. First stage: Typically due to improper specification or a manufacturing problem with the component
2. Second state: Often a random failure attributable to a materials problem or an operational irregularity
3. Third stage: Components fail due to age as the product reaches the end of its useful lifespan
Burn-In Testing Components and the Role of High-Power Sockets
To conduct a burn-in test, you need the device you’re testing, a printed circuit board (PCB), a socket, and a burn-in oven. The key to ensuring the device’s success lies in the high-power socket – a non-permanent connection from a PCB to a semiconductor device.
The interface at the PCB can either be permanent (soldered) or compression-mounted (semi-permanent). The interface to the device under test (DUT) is always semi-permanent. This means the DUT can be removed and replaced with another DUT when the test interval has been completed. The burn-in process can then be repeated.
In some burn-in processes, the DUT is removed after a few minutes and then the process is repeated with a different DUT. In other cases, the DUT is only removed after thousands of hours of testing.
Whether testing is a few minutes or hours, the socket used must work each time another DUT is attached. Sockets typically are made with high-temperature plastics, conductive metal contacts, and various springs and hardware.
Looking for reliable socket solutions for your test and burn-in challenges?
Testing Under Today’s Extreme Semiconductor Temperatures
A burn-in oven, one of the other components needed in semiconductor reliability testing, provides a stressful test environment by circulating heat around the DUT. The DUT will also generate its own heat within the oven as it processes electrical signals. This is another part of the burn-in test adapting to the times.
Smiths Interconnect burn-in ovens have evolved to accommodate the increasing temperatures needed to simulate harsh environmental operating conditions. In the recent past, temperatures ranged between 125°C (257°F) and 150°C (150°F), with an occasional 180°C (356°F). The automotive industry, for example, has been regularly pushing for burn-in temperatures of up to 175°C (347°F).
At Smiths Interconnect, they’re now handling devices that run 15 to 20 times hotter than ever before – up to 200℃ (392℉), for packages that have up to 2,000 watts.
What to Look for in Semiconductor Burn-In Reliability Testing
Some of the most impactful tech companies today, like Apple, Dell, IBM, LG, HP, and more, are facing the strictest standards. Device failures are nearly out of the question, but if they happen, they can lead to costly repairs, recalls, negative customer feedback, and damage to a business’s reputation.
Choose a partner who takes a unique step-by-step approach that keeps costs down and starts from where you’re at, and gets you where you want to go.
Uniquely, Smiths Interconnect High-Power Burn-In Testing Process and Solutions Include:
Thermal simulations: Smiths Interconnect conducts thermal simulations early to identify the issue and make solid predictions for improving efficiency within each socket’s makeup.
Components built to handle the extreme: Smiths Interconnect socket solutions can handle up to 200℃ (392℉) and accommodate higher pin counts, making them suitable for high-performance electronic devices.
Improved electrical performance: Plastronic socket solutions offer enhanced electrical performance, with better signal integrity, lower crosstalk, and better impedance control.
Customization: Smiths Interconnect offers greater design flexibility, allowing for customization and optimization of the socket design to meet specific application requirements (for cooling and heating inter-components, for example).
Cost- and time-effectiveness: Sockets are produced through automated assembly, reducing manufacturing time and costs.
Expert engineering support: Smiths Interconnect US-based experts can work in real-time (also global).
Frequently Asked Questions
What is the process of a burn-in test?
Burn-in testing is designed to detect early device failures to avoid defects in the field. During burn-in, the component endures extreme operating conditions, including temperature extremes, high-use cycles, and high voltages.
Is a burn-in test necessary?
Yes. Burn-in testing is critical to the success of a business and its electronic products. Without proper burn-in testing, there’s a high probability of failures in products, especially critical devices used in extreme environments (like medical or military).
What is the burn-in temperature for electronics?
In the recent past, temperatures have most commonly ranged between 125℃ (257℉) and 150℃ (150℉), with an occasional 180℃ (356℉). However, at Smiths Interconnect for example, they’re now handling devices that run 15 to 20 times hotter than ever before – up to 200℃ (392℉), for packages of up to 2,000 watts.
- |
- +1 赞 0
- 收藏
- 评论 0
本文由涂抹转载自Smiths Interconnect Blogs,原文标题为:High-Power Burn-In Testing in 2023: How to Overcome the Extreme,本站所有转载文章系出于传递更多信息之目的,且明确注明来源,不希望被转载的媒体或个人可与我们联系,我们将立即进行删除处理。
相关推荐
Smiths Interconnect is Transforming New Product Development with “CAD-to-FAB“
‘CAD-to-FAB’ - CAD stands for ‘computer-aided design’ and FAB for ‘digitised fabrication.’ Combined, this process can streamline and clean up the entire production line, from concept to customer-ready unit.
Smiths Interconnect Has Invested in A Comprehensive Range of Environmental Tests at Dundee Facility to Replicate Deep Space Environment
Smiths Interconnect, a global supplier of cutting-edge connectivity solutions, has invested in a comprehensive range of environmental tests at their Dundee facility. This offers an important capability to customers not prepared to negotiate on fundamental reliability and insist on demonstrable compliance.
Equalizing the Slope Gain in Your Next RF&Microwave Design, Smiths Interconnect Support the Trends and Technology of the Future
When looking at key design trends for RF & microwave components such as higher frequency, increased bandwidth, and larger component counts, it becomes apparent that RF/microwave engineers will have to look for new ways to deal with inherent challenges in gain slope that are exhibited by many RF components.
What is Thermal Simulation and Why is it Important to Reliability Burn-in Testing?
Not every semiconductor manufacturer utilizes thermal simulation in their reliability testing setup. Lower power burn-in allows for an acceptable temperature rise within the package/die in a traditional burn-in chamber running at 125℃. As packages in burn-in are moving to higher power output, socket, and burn-in systems may need to have enhanced features to manage the desired target die temps.
Smiths Interconnect 衰减器选型表
Smiths Interconnect推出高可靠性无源温补衰减器系列产品和固定衰减器系列产品,无源温补衰减器系列产品:产品可覆盖DC-40G,具备高的衰减精度,衰减值从0~10dB可选。固定衰减器系列:0.1到400W的功率等级,0~30dB的衰减值可选,并具有贴片、法兰、同轴等多封装类型。
产品型号
|
品类
|
Size(mm)
|
Impedance(Ω)
|
Frequency Range(GHz)
|
TCA Tolerance(dB/dB/˚C)
|
VSWR (Typical)
|
Power Rating(W、mW)
|
Operating Temperature(℃)
|
Substrate
|
Resistive Material
|
Terminal Material
|
TVA0500N07W1S
|
ATTENUATOR
|
1.52mmx1.91mm[0.060inx0.075in]
|
50Ω
|
DC-6GHz
|
±0.001dB/dB/˚C
|
1.30@1GHz
|
2.0W
|
-55˚C to 150˚C
|
Alumina
|
Thick Film
|
Thick Film, Nickel Barrier with Solder Plate or Lead Free Finish Gold and Wire Bondable Options Available
|
选型表 - Smiths Interconnect 立即选型
Smiths Interconnect高频Mini-Lock连接器SMPM,具有紧凑型、轻量化且坚固的设计
Smiths Interconnect的SMPM系列高频Mini-Lock连接器是一种高频率、紧凑型、轻量化且坚固的设计,适用于需要卓越电气可靠性的应用。该系列连接器可与Smiths Interconnect高频电缆组件配合使用,确保在各种应用之间实现可靠的信号完整性和完美的数据传输。
Smiths Interconnect将更新其当前定价
描述- Smiths Interconnect将于2024年12月18日起更新其当前定价,并附上更新后的分销价格表。公司承诺通过持续改进制造设施来控制未来价格变动的影响,以保持市场竞争力。分销商如需利用当前定价,请在有效日期前与销售团队合作。
Smiths Interconnect的温补衰减器解决方案介绍
温度补偿衰减器:性能卓越的信号调节神器 背景:射频增益模块(如功率放大器、低噪声放大器等,统称为增益模块)一般可用于RF、IF或LO信号路径,能够提供良好的增益平坦度和回波损耗。在不同温度条件下,其增益会出现变化,导致无法满足客户对稳定射频信号输出的要求。此外,由于不同方案使用不同的芯片模块和线路设计,其增益变化量也各不相同。
Smiths Interconnect SpaceNXT™ Q系列:高性能太空应用同轴电缆组件
Smiths Interconnect的SpaceNXT™ Q系列同轴电缆组件专为下一代太空应用设计,提供卓越的电气性能和高可靠性。该系列产品经过严格的资格验证测试,符合NASA/ESA的挥发性规格,适用于低地球轨道(LEO)、中地球轨道(MEO)和地球同步轨道(GEO)卫星平台。
Smiths Interconnect 光纤电缆选型指南
目录- Multimode fiber cables product Table General fiber optic information Optical fiber cables
型号- 500-00080,500-00021,500-00043,500-00020,500-00284,500-00085,500-00283,500-00003,500-00002,500-00266,500-00265,500-00022,500-00007,500-00205,500-00268,500-00219,500-00091,500-00274,500-00251,500-00250,500-00271,500-00277,500-00276,500-00017,500-00215,500-00258,500-00257,500-00279,500-00207
Smiths Interconnect New Hypertac Green Connect Contact Technology is Designed to Reduce Power Loss
Smiths Interconnect announced today the introduction of Hypertac Green ConnectTM, a new Lead-free and Beryllium-free hyperboloid high-power contact technology, to its established high relibility contact technologies for demanding applications.
Smiths Interconnect Lab-Flex®系列同轴电缆组件,支持最高达50GHz的频率
Smiths Interconnect的Lab-Flex®系列同轴电缆组件采用低损耗PTFE绝缘材料和实心银镀铜中心导体,确保最小的信号衰减和最高的测量稳定性。该系列产品具有悠久的历史,在高冲击和振动应用(如导弹技术)以及测试与测量环境中表现出色。常见的产品尺寸包括125、160、190、200和290,适用于多种现代应用。
史密斯互联Hypertac股份有限公司
描述- Smiths Interconnect Hypertac GmbH已委托TÜV SÜD America进行IRIS: ISO/TS 22163和ISO9001:2015认证审核,预计于2020年6月13日进行后续审核。审核通过后,将提交审核包进行审查,成功完成后将颁发证书。如有关于认证状态的疑问,请联系Michael Gürtler。
Smiths Interconnect Has a Very Large Portfolio of Existing Coaxial Isolators and Circulators for Space or Defence Applications
As it is impractical to solder the piece parts externally and pass the assembly into the cavity, Smiths Interconnect uses a contactless induction soldering and inspect the resultant solder joints using a Smiths Interconnect in-house 3D x-ray machine, whose 160keV beam makes short work of up to 5mm of steel.
电子商城
品牌:Smiths Interconnect
品类:TEMPERATURE VARIABLE CHIP ATTENUATOR
价格:¥37.0712
现货: 3,100
品牌:Smiths Interconnect
品类:TEMP VARIABLE ATTENUATOR
价格:¥11.5897
现货: 2,677
品牌:Smiths Interconnect
品类:TEMPERATURE VARIABLE ATTENUATOR
价格:¥12.7608
现货: 1,879
登录 | 立即注册
提交评论